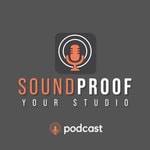
Soundproof Your Studio (Wilson Harwood)
Explore every episode of Soundproof Your Studio
Pub. Date | Title | Duration | |
---|---|---|---|
11 Apr 2022 | Which Type Of Glass Is Best For Soundproofing? | 00:13:11 | |
FREE Soundproofing Course: https://www.soundproofyourstudio.com/ Learn the four types of glass you could use for soundproofing a window and which ones I recommend. In this video we will also talk about the pros and cons of each type of glass as well as how to decide what thickness of glass to use. Link to Home Recording Studio: Build It Like The Pros: https://amzn.to/3vFI8OD Link to Allstar Glass: https://www.allstarglasstn.com/ Link to Better Soundproofing Article: https://bettersoundproofing.com/plexiglass-vs-glass-for-soundproofing/ | |||
18 Apr 2022 | Should You Build Your Soundproof Studio Or Hire It Out? | 00:16:23 | |
Download Your FREE Soundproof Studio Budget Calculator: https://www.soundproofyourstudio.com/... Have you been trying to decide whether you should hire out building your soundproof studio or do it yourself? In this video we clear up the dilemma by going over the pros and cons of each. 0:00 - Intro 1:47 - Pros To Hiring Out The Work 3:05 - Less Responsibility 4:01 - Great Finished Product 4:23 - Don't Have To Deal With Permits 4:56 - Cons To Hiring A Contractor 6:15 - Still Must Do Research 6:45 - Still Must Order Special Soundproofing Materials 7:31 - It Will Cost Way More 8:17 - Quality of the work could be lower 8:54 - The Pros To Doing It Yourself 10:06 - Intimate Knowledge Of Your Studio 10:26 - Full Over site of the Soundproofing Process 11:06 - It Will Be Cheaper 11:39 - You Will Have A Higher Quality Product 12:31 - The Cons Of Doing It Yourself 13:18 - Could Lead To More Stress 14:57 - Will Have To Deal With Codes and Permits | |||
22 Apr 2022 | How To Soundproof A Room | 00:10:12 | |
Learn what it takes to soundproof a room. Enroll in our free soundproofing course: https://www.soundproofyourstudio.com/ Home Recording Studio: Build It Like The Pros by Rod Gervais: https://www.amazon.com/Home-Recording-Studio-Build-Like/dp/143545717X or great advice and info on soundproofing materials check out: https://www.soundproofingcompany.com/ | |||
25 Apr 2022 | Is Quietrock Good For Soundproofing? | 00:16:38 | |
FREE Soundproofing Course - www.soundproofyourstudio.com In this episode we go over the pros and cons of using Quietrock versus two layers of drywall with Green Glue in the middle. | |||
04 May 2022 | Does Sonarworks Really Work? | 00:23:37 | |
FREE Room Acoustic Treatment Guide In this episode I go through an entire set up of sonarworks and show you how the software works. I give you some of my own feedback on using it over the last couple years and why I recommend every studio use this product. | |||
09 May 2022 | How To Build A Soundproof Baffle Box | 00:17:05 | |
FREE Soundproofing Course - https://www.soundproofyourstudio.com/ Learn how to design, build and install a soundproof baffle box. Link to stick pins - http://metrosupplycollc.com/gemco-insulation-hanger-self-stick-perforated-pins.html#PERFORATED%20BASE%20HANGERS | |||
16 May 2022 | What Is An ERV and Why You Need One In Your Soundproof Studio | 00:15:27 | |
FREE Soundproofing Course/Workshop - Learn what an ERV is and why I recommend one in your soundproof studio build. Don't make this big mistake I made and learn how an ERV helps with bringing in fresh air and pulling out stale air. | |||
23 May 2022 | How To Soundproof A Floor In An Apartment | 00:08:00 | |
Learn how to build an affordable soundproof floor in your apartment or bedroom. Home Recording Studio Build It Like The Pros - | |||
30 May 2022 | Backyard Soundproof Recording Studio Tour: Concrete Block Design | 00:18:17 | |
In this episode I visit a new soundproof studio build in Nashville built with concrete blocks. I interview Eric about the build and we see his finished studio. This is a follow up video to the original video I did documenting the build of his studio. | |||
06 Jun 2022 | Three Soundproof Door Designs For Your Home Studio | 00:06:44 | |
In this video I go over three soundproof door designs that you can choose to use in your home recording studio design. I talk about some of the pros and cons so you can decide which door is best for you. | |||
13 Jun 2022 | Three Reasons Building A Soundproof Studio Changed My Life | 00:08:00 | |
In this podcast I go over three reasons building a soundproof home recording studio changed my life! This video will get you excited and motivated to begin building your own home studio. | |||
20 Jun 2022 | Do Soundproofing Curtains Really Work? | 00:13:38 | |
- FREE Soundproofing Workshop - I have always been skeptical about using "soundproofing" curtains. In this video I show you the research and science behind the marketing so you can make an informed decision on if these curtains are right for your studio or home. | |||
27 Jun 2022 | How To Soundproof Existing Walls | 00:10:04 | |
In this podcast I go over how to soundproof walls that are fully finished in your home, garage or basement. You will learn which walls I recommend, how to build two types of walls and my conclusion on how you should go about soundproofing existing walls. | |||
08 Jul 2022 | Should You Use An ERV or an HRV to Ventilate Your Soundproof Recording Studio | 00:10:43 | |
FREE Soundproofing Course/Workshop - https://www.soundproofyourstudio.com/ Soundproof Your Studio Blog - https://www.soundproofyourstudio.com/blog Learn what the difference is between an ERV and an HRV and which one you should use for your soundproof home recording studio. Link to the Exhaust and Intake Hoods: https://www.supplyhouse.com/Fantech-COM4P-COM4P-Plastic-Supply-Exhaust-Hood-Combination-Pair-4-Duct?utm_source=google_ad&utm_medium=shopping_neutral&utm_campaign=Shopping_Neutral_MPLTV&gclid=CjwKCAjw7IeUBhBbEiwADhiEMe_9Yrp6DLG2aE5txPOsiwVqQg9z4TqMcQJXX3y7I8jJrAfLTsbiYhoCX-0QAvD_BwE Link to how to build a ventilation system: https://youtu.be/slv9J_v1Gc8
| |||
11 Jul 2022 | What Are STC Ratings In Soundproofing? | 00:08:30 | |
FREE Soundproofing Course/Workshop - https://www.soundproofyourstudio.com/ Soundproof Your Studio Blog - https://www.soundproofyourstudio.com/blog Learn what an STC Rating is and some of the misconceptions around it. In this video you will gain insight into the pros and cons of STC ratings and how you can use them as a tool and not get fooled by their trickery! | |||
18 Jul 2022 | Should You Use Acoustic Foam Panels? | 00:09:07 | |
FREE Home Studio Acoustic Guide - https://www.soundproofyourstudio.com/acoustic In this podcast I go over why I would or would not use acoustic foam, I compare acoustic foam to fiberglass acoustic panels, and I give you some guidelines so you purchase the right type of acoustic foam. | |||
25 Jul 2022 | Should You Buy Soundproof Windows Or Build Your Own? | 00:10:34 | |
Download The Studio Budget Calculator - https://www.soundproofyourstudio.com/calculator Read The Blog - https://www.soundproofyourstudio.com/blog Are you trying to decide if you should buy soundproof windows or try to build your own? Then this video is for you. We will go over the pros of building your own windows and how much they cost. We will look at the pros to buying your own windows and how much they cost. I will also give you my conclusion about which I would recommend. How To Build Your Own Soundproof Windows - https://youtu.be/JQiozaQcTkk What Are STC Ratings - https://youtu.be/WfIAVnCyv1U Acoustical Solutions: https://acousticalsolutions.com/ Soundproof Windows Inc: https://www.soundproofwindows.com/ Watch The Video Version Of This Podcast: https://youtu.be/yabsjdJlFfY | |||
01 Aug 2022 | How To Soundproof An HVAC System | 00:12:27 | |
FREE Soundproofing Workshop https://www.soundproofyourstudio.com/ Learn four key principles to creating a soundproof HVAC system. We talk about the importance of sizing ducts correctly, what right angles do to sound in ducts, and when to use a baffle box and how to build one. How To Ventilate Your Studio: https://youtu.be/slv9J_v1Gc8 Best HVAC Systems For Soundproofing: https://youtu.be/bPltObdECtE Insulation In Baffle Box: https://www.jm.com/en/hvac/duct-liner/linacoustic-r-300/ Nailor Industries Registers (71 DH Supple and 7145H Return): https://nailor.com/products/air-distribution/grilles-registers/airfoil-blade-grilles-registers/supply/model-series-71d-and-71s Check out the Mr Cool Mini Split here: https://mrcool.com/ | |||
08 Aug 2022 | Soundproofing Basics | 00:10:22 | |
FREE Soundproofing Course/Workshop - Learn the basics of soundproofing so you have a rock solid foundation before you learn more. If you are building a recording studio or if you just want to keep out noisy neighbors then this video is for you! | |||
15 Aug 2022 | Why Is Soundproofing So Expensive? | 00:05:34 | |
Download The Studio Budget Calculator - https://www.soundproofyourstudio.com/calculator Read The Blog - https://www.soundproofyourstudio.com/blog Are you wondering why in the world soundproofing costs so much? In this video I break down exactly why soundproofing is such a big investment. Hopefully this lesson will help you decide if you are ready to make the leap to soundproof your studio or a room in your house. How To Build Your Own Soundproof Windows - https://youtu.be/JQiozaQcTkk 0:00 - Intro 1:11 - Construction Costs 2:13 - Soundproof Specific Products 3:46 - Pre Built Soundproof Doors and Windows 4:31 - Overview | |||
22 Aug 2022 | What Is The Best Soundproof Door? | 00:08:07 | |
FREE Soundproofing Course/Workshop - https://www.soundproofyourstudio.com/ Soundproof Your Studio Blog - https://www.soundproofyourstudio.com/blog Learn which door design offers the most soundproofing for your home recording studio. We go over three door designs and then go more in depth on which one I believe will give you the best results. How To Build A Soundproof Door: https://youtu.be/bbzO_bRLmc8 Three Door Design Options: https://youtu.be/-yzsP03JJe8 ***Affiliate Links**** Home Recording Studio: Build It Like The Pros by Rod Gervais - https://amzn.to/3vFI8OD Improve your mixing and listening experience in your studio with Sonarworks: https://www.sonarworks.com/soundid-reference/overview?oid=2&affid=254&sub1=affiliate&utm_medium=affiliate
0:00 - Intro 1:05 - Three Door Options 3:25 - When To Use The Airlock System 4:24 - How The Airlock Works 6:29 - Conclusion | |||
29 Aug 2022 | How To Acoustically Treat Low Bass Frequencies | 00:12:15 | |
FREE Home Studio Acoustic Guide - https://www.soundproofyourstudio.com/acoustic Learn how to treat low frequencies in your home recording studio. I go over the basics of setting up bass traps and more advanced techniques of using tuned bass traps to improve specific frequency absorption. How To Build Your Own Acoustic Panels - https://www.youtube.com/watch?v=bWqoRYnYlqE&t=1s&ab_channel=SoundproofYourStudio GIK Acoustics - https://gikacoustics.com/product-category/bass-traps/ Room EQ Wizard - https://www.roomeqwizard.com/ **Affiliate Links** Sonarworks - https://www.sonarworks.com/soundid-reference/overview?oid=2&affid=254&sub1=affiliate&utm_medium=affiliate Home Recording Studio Build It Like The Pros - https://amzn.to/3vFI8OD
0:00 - Intro 1:11 - The Two Types of Bass Traps 2:24 - Broadband Bass Traps 4:00 - Room Testing Software 6:04 - Pressure Based Absorption 7:23 - Hemholtz Resonator 8:31 - Slat Absorber 9:31 - Should I Build Or Buy My Own? 11:05 - Conclusion
| |||
05 Sep 2022 | What Materials Do You Need To Soundproof A Room? | 00:08:07 | |
FREE Soundproofing Course/Workshop - https://www.soundproofyourstudio.com/ Soundproof Your Studio Blog - https://www.soundproofyourstudio.com/blog Many soundproofing construction products are not used in regular home construction. In this video I go over the main unique products we used when building my home recording studio. Acoustic Putty Pads: https://www.tmsoundproofing.com/Acoustical-Putty-Pads.html IB-3 Clips: https://shop.soundproofingcompany.com/products/ib-3-decoupling-bracket?variant=33155431891079 IB-1 Clips: https://shop.soundproofingcompany.com/products/ib-1-soundproofing-clip?variant=33155367960711 Green Glue:https://www.greengluecompany.com/ Magnetic Weather Stripping: https://www.amazon.com/Magnetic-Weather-Stripping-Doors-White/dp/B07MGHTZTH Zero Industries Door Seals: https://www.trudoor.com/zero/870aa-adjustable-perimeter-gasketing-acoustic-door-seal-set/ Door Bottom Seal: https://www.americanbuildersoutlet.com/zero-367-automatic-door-bottom-heavy-duty-acoustic-sound-reduction.html 0:00 - Intro 0:50 - Acoustic Putty Pads 1:36 - IB-3 Clips 2:10 - IB-1 Clips and Hat Channels 3:01 - 5/8" Drywall 3:31 - Green Glue 4:17 - Acoustic Caulk 5:26 - Tempered Glass 5:53 - Solid Core Doors 6:29 - Weather Stripping | |||
12 Sep 2022 | One Key Secret That Will Improve Your Mixes | 00:06:51 | |
Download Our Free Acoustic Treatment Guide We all have done this. You go out to your car after finishing a great mix and turn on the mix in your car only to find in horror that it doesn't sound anything like what you mixed in your studio. The reason? Bad room acoustics. Now there are two solutions to this. One acoustically treat your studio to reduce audio problems in your room. Two, use a room correction software on your speakers to flatten the response curve you hear from your speakers. Let's take a closer look at the second option. | |||
19 Sep 2022 | How To Soundproof A Ceiling | 00:09:42 | |
FREE Soundproofing Workshop - https://www.soundproofyourstudio.com/ Learn how to soundproof a ceiling using my easy to follow formula. Get results and learn from the pros. IB-1 Clips: https://shop.soundproofingcompany.com/products/ib-1-soundproofing-clip?variant=33155367960711 Green Glue:https://www.greengluecompany.com/ ***Affiliate Link**** Home Recording Studio: Build It Like The Pros by Rod Gervais - https://amzn.to/3vFI8OD 0:00 - Intro 1:05 - Overview 5:09 - Adding Mass To Your Ceiling 6:58 - Installing The Hat Channel System
| |||
26 Sep 2022 | Room Acoustics Explained In Plain English | 00:08:36 | |
FREE Home Studio Acoustic Guide - https://www.soundproofyourstudio.com/acoustic Understand the basics of room acoustics explained in easy to understand language. It doesn't need to be complicated and you can get great results in your home studio. Learn how to make your room sound better.
How To Build Your Own Acoustic Panels - https://www.youtube.com/watch?v=bWqoRYnYlqE&t=1s&ab_channel=SoundproofYourStudio **Affiliate Links** Sonarworks - https://www.sonarworks.com/soundid-reference/overview?oid=2&affid=254&sub1=affiliate&utm_medium=affiliate Home Recording Studio Build It Like The Pros - https://amzn.to/3vFI8OD 0:00 - Intro 1:16 - The Basics Of Room Acoustics 4:08 - Room Acoustic Solutions 7:38 - Conclusion | |||
03 Oct 2022 | How To Soundproof On A Budget | 00:12:29 | |
Download The Studio Budget Calculator - https://www.soundproofyourstudio.com/calculator Do you need to soundproof, but don't want to spend thousands of dollars? Then this video is for you. Learn some key techniques to reduce sound coming in and out of your room while spending way less than it would take to normally soundproof a room. Indow Window Inserts: https://indowwindows.com/ Acoustical Solutions Door Kit: https://www.asistorefront.com/p-221-soundproof-door-kit-standard.aspx Solid Core Door: https://www.homedepot.com/p/Steves-Sons-36-in-x-80-in-Composite-Unfinished-Flush-Interior-Door-Slab-Q68FHFCNAC99/100086151 Frost King: https://www.homedepot.com/s/frost+king%20weather%20stripping?NCNI-5 Door Bottom: https://www.trudoor.com/zero/361aa-heavy-duty-surface-mounted-automatic-door-bottom/ Metal Flashing:https://www.homedepot.com/p/Everbilt-1-1-2-in-x-96-in-Aluminum-Angle-with-1-16-in-Thick-802597/204273989 Plexiglass:https://www.professionalplastics.com/PLEXIGLASS-ACRYLICSHEET-EXTRUDED 0:00 - Intro 1:54 - How To Soundproof Your Door 5:47 - Total Cost of Soundproof Door 6:16 - Soundproofing Your Windows 9:21 - Total Cost of Windows 9:40 - Two Other Options 11:11 - Disclaimer
| |||
10 Oct 2022 | Is Soundbreak Good For Soundproofing | 00:11:16 | |
FREE Soundproofing Workshop - https://www.soundproofyourstudio.com/ When soundproofing there are a few companies selling specialty drywall to help with acoustic sound isolation. One of those products is Soundbreak XP sold by National Gypsum. In this podcast we are going to look at what Soundbreak is, how is compares to regular drywall in terms of its acoustical properties and the cost compared to regular drywall. Green Glue:https://www.greengluecompany.com/ ***Affiliate Link**** Home Recording Studio: Build It Like The Pros by Rod Gervais - https://amzn.to/3vFI8OD 0:00 - Intro 1:26 - What Is Soundbreak? 3:44 - Comparing STC Levels 6:35 - Cost Comparison 9:39 - Conclusion | |||
17 Oct 2022 | How To Build A Soundproof Beam | 00:05:11 | |
FREE Soundproofing Workshop - https://www.soundproofyourstudio.com/ Learn how we made a soundproof beam in my home recording studio. ***Affiliate Link**** Home Recording Studio: Build It Like The Pros by Rod Gervais - https://amzn.to/3vFI8OD
0:00 - Intro 1:04 - Overall Design 1:34 - IB-3 Clips and attaching the beam 2:10 - Adding wood spacers for side wall attachment 2:55 - Scribing side of beam 3:30 - Adding Green Glue 3:51 - Conclusion
| |||
24 Oct 2022 | Soundproofing Vs. Acoustic Treatment | 00:02:10 | |
Join the free soundproofing workshop - www.soundproofyourstudio.com
Learn the difference between soundproofing and acoustic treatment. | |||
31 Oct 2022 | Should You Soundproof or Move? | 00:10:25 | |
FREE Soundproofing Workshop - https://www.soundproofyourstudio.com/ FREE Soundproofing Budget Calculator: https://www.soundproofyourstudio.com/calculator These are some key things you should decide before soundproofing. Learn what to think about to decide it it is better to soundproof or move. ***Affiliate Link**** Home Recording Studio: Build It Like The Pros by Rod Gervais - https://amzn.to/3vFI8OD 0:00 - Intro 1:10 - The Cost Of Soundproofing 5:04 - The Time It Takes To Soundproof 7:19 - Will You Get Your Desired Results
| |||
07 Nov 2022 | Is Soundproofing Worth It? | 00:07:00 | |
FREE Soundproofing Workshop - https://www.soundproofyourstudio.com/ FREE Soundproofing Budget Calculator: https://www.soundproofyourstudio.com/calculator Is it worth it to spend all that time and money soundproofing your studio? In this video we go over three pros and three cons to soundproofing. ***Affiliate Link**** Home Recording Studio: Build It Like The Pros by Rod Gervais - https://amzn.to/3vFI8OD 0:00 - Intro 1:07 - Easier and Faster Work 1:34 - Clients Take You More Seriously 2:17 - Play Loud Music Whenever You Want 3:04 - You Don't Have The Budget 4:22 - Don't Cut Corners 5:00 - Live In A Noisy Area | |||
14 Nov 2022 | How To Soundproof Windows | 00:10:55 | |
FREE Soundproofing Workshop - www.soundproofyourstudio.com Learn the ins and outs of how to build a soundproof window. | |||
21 Nov 2022 | How Heavy Is A Soundproof Door? | 00:07:45 | |
FREE Soundproofing Workshop - https://www.soundproofyourstudio.com/ A soundproof door needs to be really heavy to stop sound, but how heavy is heavy enough? Today we will answer that question. ***Affiliate Link**** Home Recording Studio: Build It Like The Pros by Rod Gervais - https://amzn.to/3vFI8OD
| |||
28 Nov 2022 | How To Build A Soundproof Sand Filled Door | 00:07:07 | |
FREE Soundproofing Workshop - https://www.soundproofyourstudio.com/ You can build a door from scratch and fill it with sand to create a soundproof door. In this article we will go over how to build your door. Materials 3-5 bags of dry sand Lots of Wood Glue 2 Sheets of 1/4" or 3/8" Plywood 2 Sheets of plywood hardwood veneer 3-5 seven foot 2x4 studs How To Build The Door 1) Start by cutting all of your 2x4's lengthwise so the boards are now 2x2's or really 1.5" x 1.75" nominally. 2) Cut 1 piece of plywood so that it fits the size of your doorway minus 1/8" or 3mm on all four sides. 3) Attach the 2x2's to your plywood building a frame for the door. Use cross braces at the top and bottom and in the middle to keep the door square. 3) Measure 36" from the bottom and create 3 pieces of 2x2's for your lockset. These are the three middle studs you see in the picture above. 4) Next pour the sand into your door where the spaces are. 5) Glue and staple the top piece of plywood over the sand filled door. 6) Finally glue the hardwood veneer to both the front and back of your door. This door will be very heavy so make sure to use multiple people to lift it and use at least 4-6 hinges when hanging it. https://jhbrandt.net/ ***Affiliate Link**** Home Recording Studio: Build It Like The Pros by Rod Gervais - https://amzn.to/3vFI8OD 0:00 - Intro 1:15 - What Materials You Need 2:24 - How To Build The Door 5:48 - Conclusion | |||
05 Dec 2022 | Where To Use Acoustic Caulk When Soundproofing | 00:06:00 | |
FREE Soundproofing Workshop - https://www.soundproofyourstudio.com/ I have had many of my soundproofing students ask me where to use acoustic caulk. This is one of those important but often glanced over parts of soundproofing. In this article I will teach you exactly where to use acoustic caulk for your soundproof studio. 1) Where The Walls Meet The Floor Anywhere the drywall meets the floor you need to run a bead of acoustic caulk along that seem. You can also leave an 1/8" gap between the drywall layers and the floor and push in backer rod into the gap and then fill it with acoustic caulk. This will give you just a bit more isolation from the floor and the wall. 2) Where your walls meet in the corners of your room Anywhere you have two layers of drywall meeting in a corner you need to place acoustic caulk along that seem. If you want a bit more isolation with your walls you can leave an 1/8" air gap between your first layer of drywall and put in backer rod and acoustic caulk. Then you can do the same thing with the second layer, adding backer rod and acoustic caulk. This will help isolate your walls from each other. 3) Where The Walls and Ceiling Meet Anywhere your walls meet your ceiling you will need to place a bead of acoustic caulk along that seam. Again, to add isolation you can leave an 1/8" air gap and place some backer rod and acoustic caulk in between both layers of drywall. 4) Anywhere there are small holes or cracks Construction is not perfect, but your room needs to be airtight. To accomplish this we need to use acoustic caulk around all electrical boxes for lights or light switches or plugs. Use acoustic caulk where the drywall and boxes meet. You can use it around small holes like we did when running an ethernet cable through the wall. Use your best common sense when it comes to ceiling up any holes in your room. ***Affiliate Link**** Home Recording Studio: Build It Like The Pros by Rod Gervais - https://amzn.to/3vFI8OD
| |||
12 Dec 2022 | Using Brick, Plaster, Or Concrete For Soundproof Walls | 00:08:45 | |
FREE Soundproofing Workshop - https://www.soundproofyourstudio.com/ It is important to note that masonry walls will transmit impulse noise through their structure more easily than gypsum board so isolating the wall from outside sources or other parts of your structure is important. Adding mortar or compacted sand inside concrete blocks will increase isolation. Creating a double wall system with glass fiber in the air gap will also increase isolation. Summary Of STC Walls In the chart below from Master Handbook Of Acoustics by F. Alton Everest and Ken C. Pohlman, we can see that the best isolation is from double concrete block walls spaced 6" apart. This system will work really well, but uses a ton of square footage in your studio. A double wall with drywall and wood framing can achieve an STC of 63, so single masonry walls for studios are not as good as a double wall system. However, single masonry walls are much better than single drywall and wood framing. A single wall in a typical home only has an STC of 36. Comparing Concrete Walls If we look at another diagram from the Master Handbook of Acoustics we find that a single 12" concrete wall has an STC of 51 and two concrete walls spaced 6" apart has an STC of 59. The double wall system is clearly better than a single concrete wall. Remember adding insulation in the air gap will increase the STC as would adding more mass to the outsides of both or either wall. Also remember that although the STC is not comparable to our wood framed double wall the low frequency transmission loss is going to be greater in a concrete wall than a wood framed wall. If we look at a third diagram from the Master Handbook of Acoustics we can see how different brick wall designs perform. Notice that a single brick wall is not ideal. Adding wood, furring channels or gypsum board to a brick wall will increase transmission loss. The two brick walls with glass fiber in the middle will give the best transmission loss across the frequency spectrum. Using Masonry Walls and Wood Framing Together I believe the best option when soundproofing is to use a masonry wall as your outside wall to the world or the rest of your house and then frame an inside wall with at least a 1" airgap using wood framing and two layers of drywall with green glue in the middle. This will give you an STC in the 65 or higher range and will also increase your low frequency isolation. I also believe this system will save you in materials cost and floor space in your studio design.
| |||
19 Dec 2022 | 10 Reasons You Should Not Build A Soundproof Studio | 00:06:57 | |
FREE Soundproofing Workshop - https://www.soundproofyourstudio.com/ FREE Soundproofing Budget Calculator: https://www.soundproofyourstudio.com/calculator
Today I want to give you 10 reasons you may not be ready to jump into building your dream soundproof home recording studio. This article is meant to give you pause and address some things you may not have thought of with the goal of saving you time and money.
10) You Don't Own The PropertyIf you don't own your house or apartment then do not plan on building a soundproof studio. Soundproofing requires a lot of construction and cost and you want to put that into a house you own. 9) You Don't Know The Difference Between Soundproofing And Acoustic TreatmentSoundproofing is the method of construction that decreases the amount of sound that comes through floors, walls, ceilings, windows and doors. Acoustic treatment are figerglass panels that you hang on your walls to reduce acoustic reflections in your room thus making it sound better. You want to get these terms straight before jumping into a studio build. 8) You Don't Have A BudgetBefore you take on a project of this size you need to have a rock solid idea of how much it is going to cost. Otherwise, you will end up owing more money than you have and never finish the project. Make sure you have a budget in place and have agreed upon that budget with your contractor. Don't have a budget: Use our FREE Soundproofing Budget Calculator to make one. 7) You Have Researched Endlessly But Are Still UnsureIf you keep on researching, watching youtube videos, reading blogs, reading books and still don't feel rock solid on your plan than you are not ready to build your soundproof studio. You want to be certain what you are going to build will in fact be soundproof. 6) You Only Want To Build One Soundproof WallIt is logical to think that the wall with all the noise on the other side of it is the one you need to soundproof. This is logical, but not correct. A soundproof room is an all or nothing endeavor. It is lie a fishbowl. One small leak and the whole bowl will drain. If you have one small whole in your soundproof room the whole room will be compromised. 5) You Don't Have A Team To Help YouYou cannot build a full soundproof studio alone. At the very least you will need some construction help even if you are doing it yourself. You must have a great contractor, electrician, and HVAC specialist. If you have not gotten your team together then you are not ready to soundproof your studio. 4) You Don't Have A Plan For Acoustically Treating Your RoomIf you build a soundproof studio, but do not acoustically treat it then you will just have a really isolated echo chamber. To finish your studio correctly you must know what panels to use and where to place them. If you don't know how to acoustically treat your room then you are not ready to soundproof. 3) You Don't Want To Install VentilationIf you don't think you need fresh air in your new airtight soundproof studio then think again. We exhale C02 and a buildup of C02 can cause headaches and fatigue. You don't want stale air in your new studio. If you don't have a plan for ventilating your studio then put on the breaks on your build. 2) You Are Overwhelmed With Decision FatigueIf you are exhausted from endless research and still can't decide on how to build your studio then you need some outside help. It is time to look for a resource that will guide you step by step towards building your soundproof studio. 1) You Want To Cut Corners To Save Time and MoneyIt is tempting, but soundproofing is an all or nothing endeavor. You must commit to doing it right or else all of your hard work and money will be wasted and you will not get the results you desire. | |||
26 Dec 2022 | How To Build A Plywood Soundproof Floating Floor | 00:05:38 | |
FREE Soundproofing Workshop - https://www.soundproofyourstudio.com/ Owens Corning: https://www.buyinsulationproductstore.com/owens-corning-703-fiberglass-acoustic-board-2-3/ Iso-Pads: https://www.soundaway.com/IsoTrack-stud-isolator-250pk-p/16203.htm 0:00- Intro 0:41- Why You Shouldn't Float A Floor 1:59 - Iso Pads 2:42 - Fiber Glass 3:26 - Perimeter Board 3:56 - Two Layers Of Plywood 4:20 - Caulk Around Perimeter 4:39 - Add Finished Flooring | |||
02 Jan 2023 | How To Build A Budget Floating Floor | 00:06:49 | |
FREE Soundproofing Workshop: https://www.soundproofyourstudio.com/workshop Owens Corning: https://www.buyinsulationproductstore.com/owens-corning-703-fiberglass-acoustic-board-2-3/ If you want to save some money and can't build a concrete floor then this budget floor option is for you. A Word Of Warning!Now, I know soundproofing and the term "floating floor" are almost synonymous, but the truth is that a floating floor is not always the best option. In fact, a concrete slab will always be the best way to soundproof a room. The reason is that concrete has a ton of mass and will do a better job of isolation across the entire frequency spectrum. For this reason I always recommend you start with a concrete slab. However, sometimes a concrete slab is just not an option. If you are building on a second story, on top of a crawl space or simply don't have the budget to pour a concrete slab then a floating floor is for you. How To Build The Budget Floating Floor
1) Use Rigid Fiberglass First, lay down a layer of rigid fiberglass insulation across your entire floor, but leave a gap between the wall and your fiberglass. I like to use Owens Corning 703 and I would use the 4" or two layers of the 2" to giv you the most isolation. You also don't want the fiberglass fully compressing to the existing floor when you add weight on top of it. 2) Add 1x4 Strapping Add 1x4's in a pattern throughout the room to attach the drywall too. These could be every 16" on center or 24" on center depending on building codes and your budget. 3) Add Two Layers of 5/8" Drywall Add two layers of 5/8" Drywall on top of the fiberglass and 1x4" boards. Screw the drywall into the strapping boards and make sure to lay the drywall boards in opposite directions for each layers so the seams don't line up. *As a bonus you can add Green Glue in between the two layers of drywall to increase your soundproofing. 4) Add Turned Up Glass Fiber Around The Edges Add a layer of turned up glass fiber around all the edges of your room to ensure the floating floor does not touch your walls. 5) Add Your Finishing Floor Add your flooring on top of the drywall. This could be laminate flooring, carpeting, hardwood or engineered hardwood. 6) Add Base Board and Acoustic Caulk Lastly, you will add your base board on top of the fiberglass insulation. Leave a small gap between the base board and your finished floor and run a bead of acoustic caulk along the air-gap. This will ensure your room is still airtight while also not transferring vibrational noise through the baseboard to your floor.
| |||
09 Jan 2023 | Soundproof Ceiling Using Isolation Hangers | 00:12:24 | |
FREE Soundproofing Workshop: https://www.soundproofyourstudio.com/workshop Soundproof Ceiling With Hat Channels: https://youtu.be/tnNu9bFD4ck There are several options when it comes to soundproofing your ceiling. In this article I am going to explain the isolation hanger method. This will give you superior results when compared to the hat channel system, but may cost more and requires doing some basic math before diving in. Let's take a look at how to build an isolated hanging ceiling. 1) Overview Of The DesignThe basic way this soundproofing method works is that the hanger when activated with the right amount of weight will isolate your ceiling from the rest of the structure. You can see in the diagram below how the isolation hangers hold up 2x4's that span your room and then you drill in two layers of 5/8" drywall into the 2x4's. This way your ceiling is completely detached from the floor above. Sound does not travel through the hangers thus making your ceiling soundproof.
2) Calculating What Hangers You NeedIn his book, Home Recording Studio: Build It Like The Pros, Rod Gervais recommends using Mason Industries WHR Hangers. These hangers come in different colors based on the weight of the ceiling you are hanging. A way to calculate the amount of hangers you need is to look at the weight load in a 4ftx8ft area of your ceiling. Drywall comes in these dimensions so it makes the math a bit easier. Now if your current ceiling joists are placed every 16" OC then you will likely need four hangers per 4ft by 8ft area of your ceiling. This means we need to calculate the weight of the wood holding our drywall plus the weight of the drywall to determine the total load on our hangers. Here is the math: Two sheets of 5/8" Drywall = 140.8Lbs Two spans of 2x4 at 4' in length = 9lbs The total load for that 4'x8' area = 149.8lbs Now that we have the total load let's divide that by the load per hanger. To figure that out we simply divide the total load by 4 and get 37.5lbs per hanger. If we look at the mason industries website we know we will need to buy the Green hangers with a maximum capacity of 60lbs per hanger. 3) Constructing Your Hanging CeilingBuilding the ceiling is relatively straight forward. You want to hang your clips in the middle of each bay using 1/4" hook bolts. (See the diagram below to get a visual). Next, attach 1/4" hook bolts to your new 2x4 ceiling joist and attach it to the WHR Ceiling Hanger. Add insulation to both the underside of the floor and in the new cavity of the hanging ceiling. Lastly, attach two layers of drywall to the hanging ceiling joists. Finish up by using acoustic caulk where the ceiling meets your walls to make the gap airtight.
ConclusionOverall this is a great soundproof ceiling design. The main things to think about are how much ceiling height you are willing to lose with the hangers and how much isolation you need. This design will probably deliver better isolation than the hat channel style design I used in my studio. The downsides are potential added cost and the extra work of calculating the total weight of your ceiling.
| |||
16 Jan 2023 | Soundproofing A Floor With Concrete | 00:10:06 | |
FREE Soundproofing Workshop: https://www.soundproofyourstudio.com/workshop Soundproof Ceiling With Hat Channels: https://youtu.be/tnNu9bFD4ck
You can significantly increase the isolation of your ceiling or floor by adding a layer of concrete onto either your floor of your recording studio or the floor above the ceiling of your recording studio. In this article I will explain the method for doing this and compare the STC ratings of different designs with and without concrete. 1) Using Hat Channels and IB-1 Clips to Soundproof Your CeilingIn my studio we used IB-1 isolation clips and 7/8" furring channel attached to our ceiling joists to decouple the drywall from the outside structure. We drilled two layers of 5/8" drywall into the furring channel to isolate the ceiling from the roof above. Below is a diagram of this design. You can increase the sound isolation of this design by adding a layer of self leveling gypsum concrete or cellular concrete to the floor above your soundproof ceiling. This will especially help with impact noise and low frequency transmission from kick drums and bass. 2) Comparison Of Using Concrete With and Without Resilient ChannelIn this diagram below from The Master Handbook Of Acoustics Sixth Edition we can see that adding a 1.5" layer of cellular concrete with a density of 105-120 lb/ft3 will increase your STC Rating and especially help in the low frequency spectrum. For comparison, a recording studio wall can get as high as STC 63 so to keep your floor roughly in line with that wall an STC of 59 is much better than an STC of 49. Remember, any weak link in your room will compromise the STC of the entire room. So having walls with a rating of 63 is only as good as your floor, door and window STC ratings. In this diagram we see that having access to both the ceiling below your floor and the floor above will give you the greatest isolation. If you live in an apartment with only one floor this may reduce your ability to isolate your floor and ceilings using this design.
3) Comparison Of Using Concrete vs No ConcreteIn this diagram from The Master Handbook Of Acoustics we can see that when both systems are using resilient channel, but one has the concrete on the floor above the concrete floor performs better across the entire frequency spectrum. From this diagram we can see that the resilient channel and 5/8" drywall gives you an STC of 47 while the added concrete above with the resillient channel and drywall gives you an STC of 59. Notice how you get 10db of added transmission loss at 125 Hz with the concrete. You also get 15db of added loss at 500Hz and 20db at 2KHz and above. There is a huge benefit in adding mass to your floor above to get greater isolation. ConclusionFirst, we learned that adding mass in the form of concrete to the floor above will increase your STC ratings across the frequency spectrum. We also learned that to get the maximum isolation you ideally would have access to the floor and ceiling below. Lastly, it is important to consult with a structural engineer before adding the concrete to ensure your floor can handle the extra load.
| |||
23 Jan 2023 | Single Vs. Double Pane Windows For Soundproofing | 00:10:47 | |
FREE Soundproofing Workshop: https://www.soundproofyourstudio.com/workshop How To Build Soundproof Windows: https://youtu.be/JQiozaQcTkk I have been asked is it is better to use single pane or double pane windows when soundproofing. In this article I will go over which type of window is best and what I recommend for your soundproof recording studio. 1) Single Pane WindowsSingle pane windows also known as single leaf or single glazed windows are what most residential windows are. They are not good for soundproofing and should be avoided. Single pane windows only offer an STC of 25, which is far below the ideal recording studio window that would have an STC of 50+. It is important to note, that if you do have to use a single pane window then the thicker the glass the better. As you can see in the graph from The Master Handbook of Acoustics, the sound transmission loss increases as the glass thickness increases.
Lastly, if you can fully seal a window, meaning you can't open it, then your transmission loss will increase by another 3-5db.
2) Double Pane WindowsDouble pane windows also known as double glazed or double leaf windows are better at soundproofing, but still not ideal. A readily available double pane window from your window retailer will only have an STC of 38. This is still far less than needed for a recording studio. For this reason I highly recommend buying a soundproof window from a commercial acoustic window supplier like Overly or Soundproof Windows Inc. You can also build your own soundproof windows. Here is a link from my youtube channel on how to build Soundproof Windows: https://youtu.be/JQiozaQcTkk. In the figure below you can see how differing thickness of glass can improve your double pane window design.
Conclusion
Remember, don't waste money buying "normal windows." To keep your room soundproof you must use a commercial soundproof window or follow my video and build your own.
| |||
30 Jan 2023 | What Are Acoustic Holes In Glass? | 00:12:32 | |
FREE Soundproofing Workshop: https://www.soundproofyourstudio.com/workshop How To Build Soundproof Windows: https://youtu.be/JQiozaQcTkk
If you have ever wondered why soundproof windows are designed the way they are then this lesson is for you. This is also a great article on what acoustic holes are in windows.
1) Mass-Air-Mass ResonanceMass-air-mass resonance is when sound hits the outside pane of glass which then translates to the airspace between the two panes of glass. The air space acts like a spring and translates that sound to the second pane of glass. This transmission of sound waves causes a dip in the transmission loss of the window at a certain frequency. The frequency where that dip occurs depends on the thickness of the glass and the airspace between the two panes of glass. In the diagram below from The Master Handbook Of Acoustics, you can see how increasing glass thickness and increasing the airspace between the glass panes will decrease the frequency where the mass-air-mass resonance occurs. The goal is to get that frequency as low as possible for your recording studio design.
In the next diagram of my own recording studio windows you can see that I used thick pieces of glass with a large air gap to reduce the frequency at which the Mass-Air-Mass resonance occurs.
2) Coincidence ResonanceThe second type of acoustic hole that happens with glass is known as the coincidence effect. This phenomenon occurs when the speed of the sound wave moving through air matches the speed of the sound wave already in the glass. This will cause an acoustic hole at that specific sound wave speed also known as the frequency. The acoustic hole will cause a dip in transmission loss letting that specific frequency through at a greater volume than other frequencies near by. The figure below from the Master Handbook Of Acoustics shows that with two panes of 1/8" thick glass with a 1/4" air-gap the coincidence frequency happens at 4k. This means sound at 4k will travel more easily through the window than frequencies above and below 4k.
The formula for estimating the coincidence frequency is: f=500/t f= the coincidence frequency t= the thickness of the glass If we look at my two studio windows the coincidence frequency of the 1/2" pane is 1000Hz and the coincidence frequency of the 3/8" pane is 1333Hz. The two dissimilar panes of glass make it so the coincidence frequency of one pane of glass cannot make it through the other and vice versa. This is a solution to preventing an acoustic hole in your soundproof window.
3) Standing WavesStanding waves occur when two wave forms collide with each other head on either increasing the amplitude of the two waves, decreasing the amplitude or completely cancelling the wave out. Standing waves occur in the airspace between to panes of glass and can increase the resonance at certain frequencies thus causing acoustic holes. To combat standing waves, we put glass fiber on the inside our windows in the air space to absorb the sound waves that bounce around inside the airspace. This will help with some of the standing waves inside your window airspace.
Conclusion
I hope this article has helped you understand why we build the soundproof windows the way we do. If you would like to learn how to build a soundproof window like I did in my studio you can check out this video: https://youtu.be/JQiozaQcTkk
| |||
06 Feb 2023 | How To Build A Recording Studio In A Garage | 00:17:54 | |
FREE Soundproofing Workshop: https://www.soundproofyourstudio.com/workshop Sonarworks: https://www.sonarworks.com/soundid-reference/overview?oid=2&affid=254&sub1=affiliate&utm_medium=affiliate
A garage is an excellent place to build a recording studio. In this article we will look at the process and a simple design showing how I would build my studio in a garage.
The Studio DesignBelow is a mock up of how I would design my studio. This is not to scale, but it gives you an idea of the major elements we will talk about in this article.
1) Room SizeFirst, I chose my room dimensions using the Sepmeyer room equation. The sepmeyer equations are based off room dimensions that will reduce the amount of room modes in a room. Room modes are bad when it comes to acoustics, so starting with an ideal room size to begin with will make acoustically treating the room that much easier. For my studio I chose 18.64ft x 12.8ft x 8ft (celing height). You can use the calculator at this link: https://www.odometer.org/misc/ht/. This room size also leaves space in the garage to be...well a garage for storage, parking a car and extra space for my ERV and baffle boxes. More on that to come!
2) Concrete FloorThe floor of a garage is usually concrete. This is all you need to soundproof a floor. Yup, no floating floors here. Just lay down a carpet, some laminate flooring or hardwood flooring and you are good to go. 3) WallsFor my walls, I would use a double wall system. This would offer excellent soundproofing. I would use nice wood paneling on my front wall and left side wall for both acoustics and vibe. You can trade out drywall for wood whenever you want. It is all about the mass. As long as you get mass on your walls you will be fine. I would put green glue in between my drywall layers to maximize the soundproofing.
4) CeilingFor the ceiling I would use a hat channel system. I would want to make sure that my ceiling height is truly 8 feet when the hat channels and two layers of drywall are installed. If my ceiling height ends up being less than 8 feet then I would want to change my inside wall dimensions. To install my ceiling I would install I-B1 acoustic clips wit 7/8" furring channel and attach the two layers of drywall with green glue to my ceiling. If I had the space I could also build a free standing ceiling off my inside walls using new bracing and this would be the most soundproof option.
5) DoorI would use a communicating door system to soudnproof my entryway. The comunnicating doors use two solid core doors that open opposite to each other. It is important that the doors are airtight. I would buy a door sealant kit from acoustical solutions. You could also maybe save some money buying door seals directly from zero industries too.
6) Heating and CoolingFor heating and cooling I would install a Mr. Cool Minisplit. For a room this small I would install a 1200 BTU model. I would run the lines for the Mini Split through my walls and connect them to the compressor outside.
7) VentilationMany people forget about the need for fresh air. The mini split doesn't provide fresh air, so we need a separate system. I would install an ERV to provide fresh air in my studio. I would run the fresh air and exhaust air through two separate baffle boxes attached to the outside wall of my studio. This would ensure that the air is not heard and that the two big holes in your wall won't ruin your soundproof room.
8) Bass TrapsOnce I finish building the soundproof shell of my room then I will install the acoustic panels. First, I would put bass trap panels in all four corners of my room spanning from the floor to the ceiling.
9) Reflection Free ZoneNext, I would create a reflection free zone or RFZ. This is around the area where I will be listening, mixing and mastering my music. To create the RFZ I will hand acoustic panels on either side of me on both walls and hang an acoustic cloud over my head. This will ensure that the sound I am hearing from my speakers is not distorted by reflections off my walls and ceiling.
10) Diffusion PanelsNext, I would put diffusion panels across my entire back wall from roughly 2 feet off the ground. This will ensure that any sound-waves that hit the back wall will be evenly dispersed back into the room. This will make my speakers sound clearer and more focused.
11) Set Up My DeskThen I would set up my desk so that my listening spot is 38% of the length of the room. This is the ideal location to listen to your speakers in a rectangular room. In my room that listening spot would be at 7.08Ft.
12) Set Up My SpeakersI would then set up my speakers to they create an equilateral triangle from my listening spot. I would angle them so that they are pointing directly towards my listening spot. It is important to make sure that if your speakers are say 5 ft apart that both speakers would also be 5 feet from your listening spot. It is important to note that your head will most likely sit just in front of the peak of that equilateral triangle. Use your ears to dial in the exact spot. You will know when it sounds perfect!
13) Speaker CalibrationLastly, I would use Sonarworks speaker calibration software called Sound ID to calibrate my speakers to get them as flat as possible. This will make up for any problems in my room that the acoustic treatment couldn't fix. After that my studio would be finished and ready for recording, mixing and mastering.
ConclusionIf you found that to be a great overview, but feel like I should have gone more in depth, well you are right. The devil is in the details as they say. So reach out to me if you would like to learn more and need some help building your professional DIY home recording studio. | |||
13 Feb 2023 | How To Build A Soundproof Studio In A Shed - Part 1 | 00:10:19 | |
FREE Soundproofing Workshop: https://www.soundproofyourstudio.com/workshop Rod Gervais Book - https://amzn.to/3vFI8OD How To Soundproof Walls: https://youtu.be/m4G8l4RUydE
When I was first thinking about building my own home recording studio I wanted to build it in a pre-fabricated shed. The reason? It is cheaper and easier to just have a shed delivered and then soundproof the inside of it. In theory this is a great plan, but there are two main things we will talk about in this article that make your shed design potentially a disaster.
1) Case Study - Nashville Shed Recording StudioCurrently, my friend and builder, Henry Thompson, is building a soundproof recording studio here in Nashville for a drummer/producer. The studio is a big barn style shed. The goal is to soundproof his pre-fab shed so that he can play drums without bothering his neighbors and produce clients in a professional home recording studio. 2) The Problems With A ShedThis shed was placed on an existing concrete slab in Taylor, the owners, driveway. The company who sells the shed came in and built the full shed in a day or two. That is an incredible deal, but there are two big problems with using a shed that was built on site. First, the shed was built with a wood deck floor on top of the concrete driveway. Second the shed walls or sheathing are very thin. This is part of the reason it is cheaper than traditional building methods, but this is also why it is not ideal for soundproofing. In soundproofing we want mass, and thin walls mean way less mass.
3) So What Are The Solutions?The first thing you must do is remove the wood deck floor. To do this you must remove the plywood from the floor and cut out all the wood cross bracing on the floor. You must use the concrete slab as your floor for it to be properly soundproofed. For the the thin walls the key is to add mass to those existing walls. To this I recommend adding two layers of 5/8" drywall to the inside bays of your existing sheathing. To save money, I would have taken the plywood from the original shed floor and cut it down to size to add mass to the outside walls. Below is a diagram from Home Recording Studio: Build It Like The Pros by Rod Gervais.
Notice in this diagram that he recommends adding two layers of 5/8" drywall with a small gap around the drywall. Fill the small gap with backer rod and acoustic caulk to seal the added drywall to the sheathing. Then you can add a 1" cleat over the backer rod and caulk to ensure the new drywall is fully sealed and airtight. This method will ensure your outside walls match the mass of your inside walls and is crucial to achieving the STC ratings we need for recording studio design.
ConclusionYou can build a professional recording studio in a pre-fabricated shed, The key is to build it on top of a level concrete slab and to beef up the interior walls and ceilings of your building so that you are starting with an excellent structure. Then when you add the soundproofing techniques on top of that structure you will get professional results.
| |||
20 Feb 2023 | How To Soundproof Existing Windows | 00:10:15 | |
FREE Soundproofing Workshop: https://www.soundproofyourstudio.com/workshop Rod Gervais Book - https://amzn.to/3vFI8OD Master Handbook of Acoustics: https://tinyurl.com/y6sdpz4n How To Build Soundproof Windows: https://youtu.be/JQiozaQcTkk Roto Metals: https://www.rotometals.com/ Door Seal Kit: https://acousticalsolutions.com/product/privacyshield-soundproofing-door-seal-kit-complete-set/ Do you have existing windows in the room where you want to build a soundproof home recording studio? If you don't want to remove them entirely this article will show you two ways to create soundproof window inserts.
1) Seal The Window With Particle BoardI learned this method from the Master Handbook of Acoustics by Ken C. Pohlmann and F. Alton Everest. This design involves building a seal either in front of or behind your existing window in the window cavity. The idea is to use four layers of 3/4" particle board sandwiched together. You can see in the diagram below how this works.
You place the particle board in a wood frame and use four carriage bolts to secure the board together. The last board creates a full seal around the window opening and must be airtight for the system to work.
2) Creating A Door In Front or Behind Your WindowThe second design is from Home Recording Studio: Build It Like The Pros by Rod Gervais. This design allows you to open or close a massive door in front of or behind your existing window. This design involves installing a solid core door cut to the size of your window opening. You then attach the door using two to three hinges. You add more mass to this mini door by sandwiching 8psf of sheet lead between the door and 3/4 plywood.
Next, you need to build two gaskets to seal both the solid core door and the 3/4 plywood add on. It is best to add a third final seal. This can be magnetic weather stripping or a door seal kit like this one: Door Seal Kit. This system will allow you to open or close your window door when you are recording or not.
3) ConclusionIf you want to keep your existing windows as is then either of these designs will work to isolate your window for home recording. The downside will be the window will be blocked during times when you need maximum isolation. These means you won't get any natural light. The benefit of the door method is that you can open your window and allow fresh air into your studio on nice days. This is something even professional studios do not usually have and could be a nice plus to your home studio design.
| |||
27 Feb 2023 | Do Not Use MLV When Soundproofing | 00:10:03 | |
FREE Soundproofing Workshop: https://www.soundproofyourstudio.com/workshop Yup, you read that right. Don't do it! I am trying to stir up the internet on purpose. MLV is not as good at stopping sound as Green Glue with two layers of 5/8" drywall. I also am going to argue in the article that your soundproof room is only as strong as its weakest link, which in all rooms will most likely be the door.
1) You Are Only As Strong As Your Weakest LinkIt is so important to understand that a soundproof wall with an STC rating of 63 and a soundproof door with an STC rating of 57 means that your room will have an overall STC of 57. Your wall will block a lot of sound, but those same sounds will come in your door that were blocked by your wall. With this in mind it is extremely important to build your door so that it matches the STC of your wall. So what does this have to do with MLV. Let me explain.
2) MLV and Green Glue Increase Your Walls STCThat is a good thing right? Well, not so fast. If you build a doublle wall with just two layers of 5/8" drywall on both sides and achieve an STC of 63 then your door must also equal an STC of 63. To do this you must by a $5,000 plus door from a soundproof door supplier or build your own. To build your own you must match the mass of your two walls. So, two walls with an a combined STC of 63 means you have 4.4lb/sqft on one side and 4.4lb/sqft on the other side. If you build a single door it must equal 8.8lb/sqft. Lets say your door is 36" x 80" or 20 sqft. Then your door must weight 176lb at least. This is the minimum and more is better. Now, if you add Green Glue to your walls then we know that is the equivalent of adding 2 more layers of drywall to your wall. The reason we know this is from lab testing and this information is also in Rod Gervais's book: Home Recording Studio: Build It Like the Pros. This would double our mass needed on our door to 352lb's. Yes, that is a very heavy door. If you add MLV you will need to figure out how the added weight and damping effect of MLV will increase your soundproofing and adjust the door mass accordingly. Since Green Glue performs better than MLV my guess is you could build a slightly lighter door. My point is that you may get enough soundproofing from just the two layers of drywall on each wall. This would mean you are wasting money on Green Glue or MLV. Or if you do use the damping products you must increase the mass of your doors and windows accordingly. This will increase cost overall and may, again not be needed.
3) Green Glue performs better than MLVAccording to Lab Tests done by the Green Glue company with a private third party lab, Green Glue simply performs better than MLV. Look at this graph from the Green Glue company below.
You can see that Green Glue outperforms MLV except at 125hz. It performs better than MLV in general over the entire frequency spectrum. So, my question to you is why would you use MLV over Green Glue? Why would you use MLV over just two layers of 5/8" drywall? Is it because MLV is advertised well all over the internet? That is true and most searches for soundproofing will lead you to MLV. That is called great SEO and it makes MLV suppliers a lot of money. The bummer is that you are the one losing out, not them. ConclusionMy point is that adding damping in the form of MLV or Green Glue will improve the STC and Transmission Loss of your walls, but do you have the means to also increase the STC and TL of your door as well? If not, then do not bother with either MLV or Green Glue. Next, we know from lab tests that Green Glue performs better so if you are going to add a damping layer to your soundproof design please use Green Glue and not MLV.
| |||
06 Mar 2023 | Do You Need Green Glue? | 00:10:22 | |
FREE Soundproofing Workshop: https://www.soundproofyourstudio.com/workshop Lately I have been thinking a lot about if Green Glue is really necessary in a soundproof studio build. The first hint, was that Rod Gervais only mentions Green Glue in a small section of his book. His entire process involves 5/8" drywall with specific construction techniques. So, why then do we need Green Glue? This is what I will answer in this article.
1) What Is Green GlueGreen Glue is a damping system. Damping involves reducing sound energy by converting it to heat by reducing the vibrations in the material. There are many damping materials on the market, the most notable competitor to Green Glue being Mass Loaded Vinyl or MLV. In his book Home Recording Studio: Build It Like The Pros, Rod Gervais states the following: "There are a large number of damping systems on the market...But the only one that has caught my attention (providing not only greater isolation at low frequencies than standard drywall, while maintaining a cost performance that is reasonable) is a product called Green Glue..." (Gervais Chapter 4 Floor, Wall and Ceiling Construction Details pg.89).
2) How Green Glue Increases IsolationTo understand how Green Glue works we need to compare it to the mass needed to get the same isolation without using Green Glue. To understand this we need to look at Mass Law. Mass Law states that each doubling of mass adds 6dB of additional isolation, but in the real world that number is closer to 5dB. (Gervais Chapter 4 Floor, Wall and Ceiling Construction Details pg.89). So, if you have two sheets of drywall on each side of your wall the next step is four sheets on each side to increase the isolation by 5dB. Gervais shares a graph in his book from lab tests done by the Green Glue Company. These tests were done by a reputable third party lab with no connections to the Green Glue Company. In the diagram below you can see that the top two lines in the graph show the Green Glue Assembly (two layers of drywall with green glue in the middle on a single stud wall) and the estimated performance of 4 layers of drywall per side.
What is important to note is first, the Green Glue simply outperforms the four layers of drywall across the entire frequency spectrum from 250Hz upward. Starting around 125Hz and below the green glue is superior to the four layers of drywall. If we look at two layers of drywall without Green Glue it is clear that the Green Glue certainly outperforms the two layers of drywall across the entire frequency spectrum.
3) How Much Isolation Do You Need?Now the initial instinct after looking at the graph is to say, great! Let me use Green Glue because it clearly gets the best results. Before you jump to that conclusion you need to ask yourself how much isolation you really need. If you are primarily recording acoustic instruments and listening back to your speakers at a normal listening volume then you probably don't need to spend the extra money on Green Glue. However, if you are playing drums at all hours of the day or rehearsing with a heavy metal band at full blast then you would be wise to use Green Glue to get the maximum isolation possible.
4) Your Studio Is Only As Soundproof As Its Weakest LinkThe next logical step is to think if your walls are getting really great isolation then you are good to go. However, if you use Green Glue and your walls have a really high STC value, but your doors and windows do not then you will not have a soundproof room with an STC as high as your walls. Your room is only as soundproof as the least soundproof assembly in it. This means if your walls get an STC of 73, but your door gets an STC of 57 then you probably did not need to spend all that money adding Green Glue to your walls. STC is not even the best way to compare the door and the walls. The best way is to look at the Transmission Loss over the entire frequency spectrum. For example, let's look at the transmission loss of the best Overly Acoustical Door. This door gets an STC of 57. Overly, by the way, is one of the most reputable soundproof door companies on the market. Below is a diagram from the Overly door product catalog.
If we compare the frequencies of the transmission loss chart to the double wall with Green Glue we can see some comparisons. Now remember, the graph from the Green Glue company shows a single stud wall. In studios it is best to use a double stud wall so your transmission loss will be even better. This said, this high end door achieves really good results across the frequency spectrum and would perform better than the drywall with Green Glue in the low end. The only downside is this door probably costs upwards of $5,000. If you build your own door you need to try and match the weight of your walls with your door. If you are using Green Glue, remember the mass of your walls will be close to the equivalent of four layers of drywall on each side. For a double door system that means both doors need to weigh close to 176 LBs or more to match the mass of your walls.
ConclusionFor most DIY soundproofing projects Green Glue may be overkill. However, if you are a drummer or a very loud band then I would consider Green Glue and building a very heavy door or buying a professionally built one. The key is to remember your soundproofing is only as good as your weakest link. Companies like Green Glue want to sell you their product, but be aware of the bias towards getting superior results without taking into account your doors and windows as well.
Works Cited: Gervais, Rod. “Chapter 4 Floor, Wall and Ceiling Construction Details.” Home Recording Studio: Build It like the Pros, Delmar, Clifton Park, NY, 2011. “Product Catalog.” Overly Door Company, https://door.overly.com/products?PT_Guid=d942747f-96d5-4dc3-8b3b-58a3b5b70a55&PM_Guid=2f9a63cb-9c60-4b12-8cc9-8c852003606e&PA_Guid=b5b287a4-917d-4771-bac9-07cc0941bd0c.
| |||
13 Mar 2023 | The Best Soundproof Floor Design | 00:05:21 | |
FREE Soundproofing Workshop: https://www.soundproofyourstudio.com/workshop When most people think of soundproofing they think of foam, a room within a room and a floating floor. Now there are a lot of myths out there about floating floors and today I want to clear it up by telling you that floating a floor in almost all situations is a bad soundproofing option.
1) What Is The Best Floor Design For Soundproofing?The best option is to build on a concrete slab. This option offers you the best soundproofing for your home recording studio. The reason a concrete slab is the best option is because it sits on the earth which offers great insulation around the slab and that the slab itself has so much mass that it can stop sound from entering your studio.
2) Where Should You Build Your Soundproof Floor?If you are building a soundproof studio in your home then you should build your studio in your basement if it has an existing concrete slab or in your garage. If you are planning to do what I did and build a studio in your backyard then you can pour a concrete slab and build your studio on top of it.
3) Dealing With Multiple RoomsIf you want to have more than one soundproof room in your home recording studio then the best option is to pour isolated concrete slabs. You can see in this diagram below that isolated concrete slabs allow you to have adjacent rooms that are not connected by the same floor. This means sound will not travel from one concrete slab to the other.
An expansion joint and some caulk fills the space between the two slabs. I would recommend you find a concrete specialist who has experience pouring isolated slabs before you choose this option.
4) But What If I Don't Have The Option To Build On A Concrete SlabWell, this is a common problem. My first gut reaction is find a different location where you can. The amount of money and expertise needed to properly float a floor is beyond the scope of a home studio. If you absolutely must float your floor then you will have to live with the fact that your floor will be a weak link in your soundproof room. A weak link means you will not know until you are finished if your studio will be soundproof enough for your goals. This means gambling tens of thousands of dollars on a soundproofing job that might not work.
ConclusionIf you are building a soundproof home recording studio stick to using a concrete slab as your floor. It will start you off with the best soundproof floor possible. I don't recommend building a home recording studio on a floating floor and would recommend you move or change the location of your studio before going down that path. | |||
20 Mar 2023 | Acoustics Of A Professional Mastering Studio | 00:12:37 | |
FREE Acoustic Treatment Guide: https://www.soundproofyourstudio.com/acoustic Hire Duncan Ferguson: https://thevoltageexchange.com/
This week's video and article is a bit different from my usual teaching. I recently had coffee with my new friend, Duncan Ferguson who is a professional mastering engineer and owner of the studio, The Voltage Exchange. We toured his studio and talked about his acoustic treatment build out. Here are some key takeaways.
1) His Studio Is Not SoundproofDuncan weighed his costs with this build and decided to put his money into the acoustics not the soundproofing. 2) This Is A "Beta" Studio DesignDuncan says it himself, this design was born from his experience with a masters degree in acoustics, running sound testing for stadium shows and his years as a professional mastering room. He does have a lot of knowledge, but this was his first studio design. 3) Mastering Studio AcousticsAcoustics vary depending on the usage of the room. In Duncan's case he needs an extremely flat and accurate frequency response in his room. For this reason it may be more dead or in some cases "boring" than a live room in a studio. His studio design is based off the control room principal where all acoustic decisions are made to get the most accurate listening experience possible. It is good to keep this in mind as you watch the video, since not all rooms should be acoustically treated the same way. I also find that acoustic design is more of an artform than a science in much the same way mixing and mastering is. Ultimately, we need to follow some ground rules, but the real beauty of the sonics of a room is in the ear of the beholder. If you are designing a recording studio then check out my FREE Acoustic Treatment Guide to get all the best tips on acoustically treating your home recording studio.
| |||
27 Mar 2023 | How Soundproof Is My Studio? | 00:14:21 | |
FREE Soundproofing Workshop: https://www.soundproofyourstudio.com/workshop
In 2020 I built a soundproof studio in my backyard. I had no prior experience building studios and I primarily used Rod Gervai's book, Home Recording Studio: Build It Like The Pros and the advice from The Soundproofing Company to design and build my studio. In this article I want to show you how soundproof my studio actually is, so you know what level of soundproofing you can achieve with these methods.
1) Taking SPL MeasurementsBefore you build your studio you can take SPL measurements as many times as possible each day for 7 days to see what the highest reading you get is. This will be the SPL reading you need to soundproof against. In my studio I recorded an SPL of around 26dB. I took this measurement at 9:17am on a Monday morning. I then went outside and measure the ambient SPL of my neighborhood right outside the front door of my recording studio. The peak readings I got while outside was 57.6dB. So my transmission loss, or TL for short, was 31.6dB. Now it is important to note that not all frequencies have the same TL. So low bass frequencies will pass through my soundproof structure more easily than higher frequencies. Our goal with soundproofing is to try and reduce the sound outside as much as possible, while also reducing the loud sounds in our studio from coming out into the neighborhood. The best way to do SPL measurements for your studio is to take as many as possible at different times of the day. For example if you hear a siren passing by, pull out your SPL meter and record the level. This will help you get an idea for peak SPL levels in your studio.
2) What About Loud Music In My Studio?So in this test I did while playing my monitors, I reached an SPL of 87.6. When I closed my door while the speakers were still blasting the SPL outside dropped to 48dB. That means there was a TL of 39.6db. We also know that 48db was the ambient SPL of my backyard, so essentially my studio blocked out all the sound of the speakers at a very high listening level. I would never mix or listen back as loud as I was playing them. For drums there would certainly be a higher SPL in the studio and thus maybe a higher SPL right outside. I will have to do that experiment the next time I have drums in the studio.
3) Okay, so what do I hear in my studio?After working in my studio for 2 and a half years I can say that a take has never been ruined due to outside sound. That is not something I can say for my home studios previously. I can also say that when we play with drums or a full band in the studio the neighbors have never complained. I do not use the studio at all hours of the night, but I am confident it would not be a problem. Now I do hear some noises. Super powerful sub bass from cars in the apartment complex behind my house will enter the studio, but only in very low frequencies like 40hz and below. That is annoying, but you can EQ that off in most recordings. It is also fairly rare. I can hear thunder, but again it is only the low frequencies and it really doesn't come through much. I cannot hear rain at all. If a helicopter is flying really low I might hear some of its lower frequency energy, but it is not super loud. Lastly, if they are mowing the lawn, it really doesn't matter unless they drive the lawnmower right by my door or directly up against the back wall. 4) How My Studio Could Improve SoundproofingMy door...oh my door. What a headache it has been. It has cost me so much time and money. If I could do it all over again I would have designed a communicating door system with Zero Industry seals going around each door. I also would have used the JH Brandt method of door construction not Gervais's. I would have used Corning 703 wrapped in fabric between the doors to increase transmission loss. One day I plan on adding a second door and better seals, but my budget currently does not allow for it and honestly it doesn't affect my work. It is more of a nerd and ego thing to make my door as soundproof as possible. This said, I am confident that I would hear even less if my door had been built better the first time through. I hope you have found this article insightful and helpful in understanding how soundproof a studio can be and how soundproof my studio is. Remember, you cannot eliminate all sound, but you can reduce it to an acceptable level for professional level recording.
| |||
03 Apr 2023 | You Cannot Build A Soundproof Studio For Less Than $10K | 00:10:17 | |
Download my FREE Budget Calculator: https://www.soundproofyourstudio.com/calculator Want Soundproof Consulting: https://www.soundproofyourstudio.com/consulting Many potential clients reach out to me saying they have less than $10K to build a studio. The problem is that unless your studio is a 8x10 square foot room or smaller, chances are you will need to spend more money on your soundproofing project. Next, if you add in the cost of properly acoustically treating your studio, you are looking at another couple thousand dollars as well. In the video above I go over several different studio sizes and different budgets and show you with my soundproof studio budget calculator, exactly how much a soundproof studio will cost both if you build it from the ground up or inside an existing structure. To download the soundproofing budget calculator simply click this link: https://www.soundproofyourstudio.com/calculator. | |||
10 Apr 2023 | Do Not Angle Your Recording Studio Walls | 00:08:02 | |
If you are interested in learning more about how to acoustically treat your recording studio, download my FREE Acoustic Treatment Guide to dial in your home studio acoustics. Yes, you read that right. This is a very controversial topic out on the internet and I wanted to confront it head on. Everyone, and I mean pretty much everyone, wants to angle their studio walls. However, it is a myth that has been perpetuated through the ages. In this article I will give you all the science behind what angling walls really does.
1) It Will Not Fix Room Mode Issues Splaying walls will not eliminate room modes, but it may shift them slightly and help a little with diffusion. (Everest and Pohlmann 257) Everest and Pohlmann also cite a study by Van Niewland and Weber in their book that shows that room modes in non-rectangular rooms are in fact still there, but are harder to predict. This means that choosing a rectangular room using a room ratio that falls within the range of some of science's best acousticians: Bolt, Boner, Volkmann, Sepmeyer and Louden, will give you a room that has a more uniform distribution of modal frequencies in a room. (Everest and Pohlmann 254) This means you can predict the room modes and more easily treat them with room acoustic treatment.
2) You Will Lose A Lot Of Space In Your Room This may be the main reason not to splay your walls. First, let's be clear you can angle walls in a control room after the initial rectangular shell is created. This can be done using smaller framing timber and creating what is known as a reflection free zone around your speakers. It is important to note that even when a studio seemingly has angled walls, the true soundproof wall behind the inner studio is still rectangular. Now, angling walls will help with one thing and that is flutter echo. Flutter echo occurs when sound bounces between two parallel walls. It is the pinging sound you hear when you clap your hands in a room. It is also not desirable for recording studios. However, you can easily treat flutter echo in a room using acoustic panels. It is far cheaper to hang panels then to angle a wall. If you are dead set on angling your walls then you must angle them the right amount. According to the Master Handbook of Acoustics most walls are splayed "between 1ft in 20ft and 1ft in 10ft." (Everest and Pohlmann 257) This means if you splay one wall in a room that is 20ft long you will lose 10 square feet of space. I don't know about you, but that space is really useful and expensive to build. It's also important to note that in a control room you cannot just spaly one wall. You want symmetry in your room, so you would need to splay two walls losing even more space. You can see that splaying walls is not really ideal for any studio and especially a home studio.
Conclusion There is not really much benefit to angling your walls in a recording studio. The cons far out weight the pros. One of the biggest factors in good room acoustics are using correct room ratios to start with and having rooms with large volumes. Splaying your walls will make it so you do not know the room modes and may actually make your room sound worse, and it will decrease the volume of your room, also making it sound worse. All problems with flutter echo and diffusion can be solved using carefully placed acoustic panels. You do not need to waste money and space angling walls. Works Cited: Everest, F. A., and Ken C. Pohlmann. Master Handbook Of Acoustics. 6th ed., McGraw Hill Education, 2015. pp. 257-259. | |||
17 Apr 2023 | What Is A Reflection Free Zone? | 00:08:52 | |
If you do some research on acoustics, chances are you will come across the term Reflection Free Zone or RFZ. In this article we will earn what it is and how to implement one in your own home recording studio.
1) What is an RFZ?The reflection free zone is an area in your room where you reduce all the first reflection off your side walls and ceiling, so that you get as clear of a listening field as possible. This concept really only applies to control rooms or home studios where you record and listen back in the same room. You can see in the image below from my own home studio that I have created an RFZ by hanging panels on both side walls and hanging an acoustic cloud directly above my head and slightly in front of me to absorb reflections off the ceiling.
2) How do you set up a reflection free zone?Once you have dialed in your listening position and your speaker placement then you are ready to treat the side walls and ceiling. To do this you will need a mirror and a friend to hold the mirror as you sit in your listening position. Because sound and light will both reflect off surfaces based on their angle of incidence, you can use a mirror to see where the sound waves will reflect on your side walls. Here is the process for finding where to hang your acoustic panels. 1) Sit in your listening position facing your speakers. 2) Have your friend hold the mirror directly against the wall in the front right corner. 3) Now have your friend move the mirror slowly along the wall towards the back wall. 4) Look at the mirror and wait until you see the front of your right speaker show up in the mirror. 5) At that location have your friend mark a pencil line on the wall at the left edge of the mirror. This is where you will hang your first acoustic panel. 6) Now have your friend continue moving the mirror along the wall until you no longer see the front of the right speaker in the mirror. 7) Mark the right edge of the mirror on the wall with a pencil. This will be the end of your acoustic treatment. Repeat this same process for the left wall. 3) Hang Your Acoustic TreatmentNow you will have a space on both side walls between your two pencil lines that will need to be filled with acoustic panels. I like to build my own panels. If you want to build panels, here is a great tutorial on how to make high quality affordable panels: https://www.youtube.com/watch?v=bWqoRYnYlqE Once you have bought or built your panels then you want to hang them so that the middle of the panel falls at your ears height when you are sitting at the listening position. 4) Hanging Your Acoustic CloudLastly, we want to reduce the reflections from the ceiling. To do this we need to hang several acoustic panels over our head. The lower you hang the panel the more low end attenuation you will get. You will have to decide how low you want to hang your panel for aesthetics and ease of use in the studio. Make sure to hang your panel from your ceiling studs to hold up the weight.
ConclusionThat is the theory and application of a reflection free zone. if done properly, it can greatly improve the clarity of your stereo field. If you are looking to acoustically treat your own home studio then download my FREE Acoustic Treatment Guide to get a full overview of how to treat your own studio. | |||
24 Apr 2023 | Do You Need Extreme Soundproofing? | 00:12:42 | |
FREE Soundproofing Workshop: https://www.soundproofyourstudio.com/workshop There are times when the most powerful soundproofing techniques are needed. In this article I will go over the techniques that yield the most isolation for your soundproof design. These techniques may be needed if you have an especially loud source, like drums, you need to isolate or if you live near an especially loud neighbor, like an airport, and need to keep those sounds out of your studio.
1) Let's Review The BasicsTo understand the best isolation techniques we need to revisit the fundamentals of sound isolation. To soundproof a room we need three things: a) Mass b) An airtight room c) decoupling from our outside structure Mass involves adding lots of weight to our floor, walls and ceiling. It really is as simple as that. The more weight your assemblies have, the better your sound isolation will be. The single most useful tool for increasing isolation is to add mass. Next, we have air. For a room to be soundproof it must be airtight. This means every possible hole must be filled with acoustic caulk, acoustic putty pads, or special acoustical seals around doors. Even a small hole will let in sound, so we must ensure the room is sealed completely. Lastly, it is important to fully decouple the outside structure from the inside structure. This is the common term "a room within a room." For extreme soundproofing we are going to use the best decoupling techniques to ensure sound does not travel through our structure into our soundproof room.
2) Extreme Soundproof FloorThe best soundproof floor is easy. It is a concrete slab poured over earth. Yup, no second stories here. For the best most extreme soundproofing you need to stay close to the ground. A concrete slab poured over earth will off you the best sound isolation period. Done deal!
3) Extreme Soundproof WallsIf you need to keep out the sound of a kick drum, an electric bass amp, or the rehearsal of a heavy metal band you are going to need some powerful walls. Now you may have heard a term STC. It is helpful, but misleading. The reason? STC only measures frequencies down to 125hz. The most complained about noises are always bass or low frequencies below 125hz. I know, this is a total bummer. It means we have no way of knowing for sure if our soundproofing will fully work in the low frequency range. Yup, it sucks and I wish the labs would measure lower, but I believe the reason is they cannot guarantee accurate results sub 100hz. Don't quote me on that, but I did read it on the internet and it would explain this issue with STC ratings. So, the best you can do is build the most soundproof wall within your budget and available space. Here are some ideas for a super soundproof wall. A) Two Concrete Walls with Compacted Sand Now, this is extreme but you could build two concrete block walls filled with dry compacted sand and achieve very high isolation. It is important to put fiberglass insulation between your two walls to achieve maximum isolation. The minimum distance recommended between the walls is 1", but you guessed it, the greater the air gap the greater the isolation. So, if you had the budget and space you could put a 1 foot air gap and really attenuate those low frequencies. B) A Double Walls System With 4 Layers of Drywall and Green Glue Now, this is hardcore! We know that a double of mass will increase isolation by about 5dB. It may not seem like much, but it does help, since we hear a halving of sound at 10dB. That's like turning the volume knob on your room. Here is the plan. Notice on the chart below that the best STC rating is the two walls with an air gap and two layers of drywall on each side with fiberglass insulation in the middle. To get even better isolation we can add two more layers of 5/8" drywall to each side. Now to go crazy, we can get even more attenuation by adding Green Glue in between the two layers of drywall on each side. Just like our concrete wall we can increase the air gap and achieve even more isolation. I am very confident that this would really deaden the sound of drums, loud band rehearsals and most of the low frequencies.
*A Word Of Warning - Soundproofing is not perfect. You could spend $150,000 building a concrete bunker and maybe still here 40hz. The goal is to turn down the volume of sound in your studio to an acceptable level for your neighbors and you.
4) Extreme Soundproof CeilingNow that our floor and walls are super soundproofed we need to tackle the ceiling. The best way to soundproof the ceiling will be to frame it off the inner walls. So, with our concrete blocks you can build a frame off the inner block walls and with the wood walls you need to frame of the inner wood wall. Now, it's best to consult with a professional if you don't know how much your new framed ceiling will hold. You guessed it, we are going to layer 4 layers of drywall on our ceiling to match our wall mass. Add that Green Glue for good measure if you like. It is important to remember that with soundproofing we are only as strong as our weakest link. This means we want our mass to be consistent on all four surfaces of our room and outside walls and roof. That said, the air gap and mass on your ceiling also applies here. We want to not only add four layers of drywall to our ceiling, but ideally have the same mass, air gap and fiberglass insulation above our ceiling as well. This could be in the form of an upstairs with extra plywood layered on the floor. You could add 4 layers of drywall under your upstairs floor, but either way the consistency is key. If it is a roof above you, then you can add mass to your roof.
ConclusionAs you can see Extreme Soundproofing is, well, extreme. It takes some drastic measures to stop low frequencies from entering and exiting your room. The key take away from this article is that you have two levers to pull to increase isolation. First, you can tug on the mass lever. This means just beefing up all your assemblies with more weight. 5/8" drywall is the typical choice for ease of use and budget, but really anything with mass will work. Second, you can increase the air gap. By moving your interior wall away from the exterior wall you will increase isolation. I did those in order on purpose. The mass lever is by for the more powerful of the two. Start with mass and then add air space between walls if you can. | |||
01 May 2023 | Is SONOpan Good For Soundproofing? | 00:17:37 | |
FREE Soundproofing Workshop - https://www.soundproofyourstudio.com/workshop It seems everyday a new soundproofing product is introduced to the internet. Some of these products can be helpful for soundproofing, while many others are simply a waste of money. Today I will go over a popular soundproofing product called SONpan and let you know if it is worth installing in your soundproofing project.
1) What is SONOpanAccording to their website, SONOpan is made from 100% recycled wood and 100% natural binders.I am not sure what the natural binders mean, but it might be the glue or adhesive that holds the wood pieces together. The company who makes SONOpan is MSL and they are a Canadian based manufacturing company.
2) How is SONOpan UsedAccording to their website, SONOpan is used directly on the studs of your walls and ceilings or over your existing drywall to "soundproof" your room. They also have a product called SONOpanX which is meant for floor installations. They claim it mostly helps with impact noise such as footfall noise or bowling balls dropping on a bowling lane, but not so much with airborne noise.
3) How does SONOpan stop sound transmissionOkay here is the real question. How does this stuff work and does it work? Again, according to their website they have trademarked the term "Noise Stop Technology." This means nothing technically, but is a good marketing tactic. Based on everything they say on their website it looks like SONOpan is really good at absorbing sound. This is similar to fiberglass insulation which has high absorption coefficients across the frequency spectrum. Here is how they say their panels work: "SONOpan has over 17,000 impressions in both sides of the panel resulting in a varying density throughout. When it comes to soundproofing, each frequency range has a corresponding sound wave where the peaks and valleys of that range are a certain size. The peaks and valleys in SONOpan are what make it extremely effective at soundproofing." - SONOpan Website Here is where they lose me. Soundproofing is not the same as sound absorption. Soundproofing involves adding mass to your walls, making sure they are air tight, using insulation in your walls, and making sure your walls are decoupled from the outside structure. SONOpan does none of those things. SONOpan may be good at helping the acoustics in your room, but I don't understand from simple physics how it could help with soundproofing. Next, fiberglass insulation can absorb frequencies down to 125hz. However, to absorb frequencies in a room below 100hz you need pressure based absorbers like helmholtz resonators or membrane absorbers. A piece of thin wood fiber will definitely not absorb low bass frequencies. "The peaks and valleys in SONOpan" are what help with high frequency absorption most likely above 500hz. Again, this product may be a good alternative to acoustic panels in your studio, but I would not use it for soundproofing. 4) What are the SONOpan STC ratingsSTC or Sound Transmission Class ratings are a way to compare different soundproofing assemblies with each other. The higher the STC rating the better that assembly is at attenuating sound between 125 hz and 4000 hz. This is roughly the frequency spectrum of human speech, but it does not account for frequencies from low bass, kick drums, trucks driving by, airplane rumble, helicopters buzzing, or lawnmowers nearby. So when we look at STC ratings claiming to soundproof a room we need to be aware that low bass frequencies are not being accounted for. The best way to attenuate low frequencies is to add mass to your assembly. The best way I recommend soundproofing a wall is to use what I call the double wall assembly. Here is what SONOpan says they get from: 2 layers of 5/8" drywall>wood studs> R13 insulation> 1" air gap > R13 Insulation> wood stud> SONOpan> 2 layers of 5/8" drywall. image source: SONOpan Website
Notice the STC rating is 68. As a side note, I did not find any lab test results for their STC ratings, which means we are taking their word for their data not an independent third party lab. When I reached out about their lab tests, they responded by telling me SONOpan is not yet available in the United States, which did not answer my question. Now let's look at the same wall STC rating without SONOpan.
Notice the same wall design without SONOpan gives you an STC rating of 63. Now can you hear the difference of 5 STC points? The answer is not really. STC ratings are not a perfect example of how we perceive soundproofing either, so small differences in numbering at not as noticeable as say an STC of 45 versus 68. Next, here is another STC chart from a company called The Soundproofing Company. This diagram is from the Soundproofing Company website.
This wall assembly is essentially the same design as the previous two accept that it includes two layers of Green Glue between the two layers of 5/8" drywall. As you can see the STC rating for this wall assembly is 73. This is better than 68 and 63. Again it would be best to double check these STC ratings with the verified lab test data just to make sure the data is accurate. The key takeaway is that the main thing "soundproofing" all three of these walls is drywall, the airspace, the insulation and making sure it is airtight using acoustic sealant. The Green Glue and SONOpan may add a few STC numbers, but it is not earth shatteringly different.
ConclusionWhen it comes to soundproofing there really isn't some secret technology that will suddenly make your sound go away. The design of your walls and ceilings and floors really comes down to some fairly simple design concepts. The use of additional soundproofing products like Green Glue and SONOpan may help a tiny bit, but consumers should really ask themselves if it is truly worth the added cost. The main cost of soundproofing your walls is going to be the cost of lumber, drywall and insulation. These materials will soundproof your wall if you build it correctly. Adding SONOpan seems like a waste of money to me. As of right now SONOpan costs $29.63 per 4ft x 8ft panel. 5/8" drywall costs $17.87 per 4ft by 8ft panel. I would always use 5/8" drywall over SONOpan because it adds mass. At the end of the day mass will help way more with soundproofing than anything else. Lastly, SONOpan has very little mass compared to 5/8" drywall. 5/8" drywall weights 70.4 Lbs whereas SONOpan only weighs 26 Lbs. To be completely honest, I don't see how SONOpan soundproofs at all. I could believe that it absorbs sound, but remember absorption is used for room acoustics not soundproofing. I would not recommend using SONOpan and I hope you now have some solid science and facts to prove why you should say no to some flashy soundproof marketing with SONOpan. | |||
08 May 2023 | How Much Fresh Air Do You Need In Your Soundproof Studio? | 00:07:25 | |
FREE Soundproofing Workshop: https://www.soundproofyourstudio.com/workshop If you have been following my youtube channel, emails or podcast for some time you may know that I am a big fan of having ventilation in your soundproof recording studio. The reason is that when you soundproof a room correctly the room will be airtight. This means you will not have any fresh air circulating in and out of the room. Contrary to popular belief, mini-splits and home HVAC systems do not provide fresh air unless you have a fresh air system in place. Most older homes do not have fresh air systems because they were not necessary. Older homes tend to have so many cracks and small holes that the air from outside can make its way in. Newer homes on the other hand are build tighter, meaning they are similar to our soundproof rooms and need fresh air systems incorporated into the design.
1) How Much Fresh Air Do You NeedAccording to Rod Gervais, the author of Home Recording Studio: Build It Like The Pros, a good rule of thumb is to provide 15cfm per person. CFM stands for cubic feet of air per minute. This is equal to 0.42 cubic meters per minute for my metric friends. Now the best way to provide fresh air to your home is to use either an ERV or HRV. This article will not go in depth into what they are, but just know that an ERV (Energy Recovery Ventilator) will help recover moisture and heat during ventilation while an HRV (Heat Recovery Ventilator) mainly helps recover heat during ventilation. So when you are buying your ERV or HRV you need to know what size you unit you will need.
2) Buying the Right Size Ventilation SystemSo for my studio I am usually the main person working in my space. I occasionally will have clients and studio musicians in the space, but this leads to a total of 3 people max. I would there for want an ERV that delivers around 45 CPM to satisfy my ventilation needs. Now if you have a studio that has full bands in the live room or control room you will need a larger unit. For example, five people would need 75 CFM of airflow.
3) Sizing The UnitWhen you are looking for the right ERV or HRV for your home studio build make sure to begin your search by sizing the right unit. If we go back to our example before, I would look for an ERV that provides 75 CFM. Just doing a quick google search I came up with a unit that would work for this example. The Fantech AEV80 provides 80 CFM and would adequately provide enough fresh air for 5 people. I have a Fantech ERV and it has worked wonderfully.
ConclusionSo, it is not so complicated, but you do want to remember that each person in your studio will need 15CFM of fresh air. By incorporating a fresh air system into your studio design you are setting yourself up for success and lasting health in your soundproof studio for years to come. | |||
15 May 2023 | How To Build A Soundproof Shed - Part 2 | 00:13:03 | |
FREE Soundproofing Workshop: https://www.soundproofyourstudio.com/workshop My contractor, Henry Thompson has been working on a soundproof studio here in Nashville that is built within a prefabricated shed. This is part two of the build series and it will go over the double walls, insulation, hat channels, drywall and installing the window. If you want to see part 1 of the series you can watch it here: https://www.youtube.com/watch?v=fuDgG2Wre9g
1) Double WallsIn part one we talked about adding mass to the outside wall. In this lesson we are going over the double wall system. Henry and his team built out a seperate wall 1 inch from the existing structure to soundproof all the walls. He used special acoustic clips called IB-3 clips to attach the inside wall to the existing structure. These clips are specially designed to reduce sound transmission traveling from the existing structure to your inside walls.
2) Spray FoamNow spray foam does not help with soundproofing, but it does help with moisture issues. Because the roof is not vented Henry opted to use spray foam on the entire existing shed walls and ceiling. This allows proper insulation so the ceiling does not have condensation build up. This also helps tremendously with ensuring the roof system is airtight. Traditionally a cathedral style ceiling like this one would need soffits to vent properly. The problem with this method is that it means your ceiling doesn't get the double wall system you need for proper soundproofing.
3) Putty Pads and InsulationAfter the spray foam was installed, Henry and his team installed putty pads around all outlets and electrical boxes. This ensures that sound cannot easily transfer through the boxes behind light switches, outlets and overhead lights. Next, the team installed regular pink insulation in all of the wall and ceiling cavities. This is an important part of the soundproof wall design and the spray foam is not enough for proper soundproofing.
4) Hat Channels and Loft Floating FloorHenry and his team installed hat channels and IB-1 acoustic clips on all of the ceilings in the studio and along the beam supporting the loft. The hat channels decouple the two layers of drywall from the ceiling making it soundproof. The loft posed a difficult soundproofing problem. In the end, Henry floated the loft floor using some U shaped auralex floor pads. These are not usually something I would recommend, but in this situation we had to improvise some to soundproof the loft as best as possible. Henry added mass to the loft floor to help isolate it from the entryway below. 5) Drywall, Green Glue and Acoustic CaulkOnce the insulation is in and the hat channels are installed the next step is adding the two layers of 5/8" drywall with Green Glue in the middle. The two layers of drywall add the needed mass to soundproof our walls and ceiling and the Green Glue helps stop lower frequencies and increase isolation due to damping. Once the drywall is in place they caulked the floor to wall, wall to ceiling and all corners with acoustic caulk to make sure the entire system is airtight.
6) Barn DoorsThe shed came with two barn doors. This also posed a challenge to our team because the doors are large and not very heavy. Henry came up with the solution of adding two layers of 5/8" drywall with Green Glue to the back of each door. The doors will not be soundproof until the project is complete, but this will add some much needed mass to the front door system.
7) Mini Split (Heating and Cooling)For heating and cooling needs, Henry and his team installed a Mr. Cool mini split on the back floor joist under the loft. This also allows plenty of space for the piping to run through the walls and out to the condenser. Remember, mini splits offer quiet heating and cooling, but they do not offer fresh air. For that you need a separate ventilation system.
8) WindowLastly, Henry and his team installed a large outside window on the front wall. This window is made of laminated glass and is thick to help stop sound. Henry created a frame for the window to sit in and then sealed any air gaps using DAP AMP, which is an all weather sealant. This sealant is important to keep the window airtight. Once the sealant was in place, Henry installed the outside trip around the window using a nail gun. | |||
22 May 2023 | Humidity Problems In Your Home Recording Studio | 00:12:16 | |
FREE Soundproofing Workshop: https://www.soundproofyourstudio.com/workshop HVAC is certainly the hardest part of building a soundproof home recording studio. An often overlooked part of your heating and cooling system is humidity control. In this article we are going to go over the best practices when designing your HVAC system to keep your relative humidity in the ideal range.
1) What is the ideal relative humidity?This is a debatable topic, but most books I have read and websites I researched said that 30-50% relative humidity is ideal. (Lennox)
2) Why do we use the term "relative" when talking about humidity?You might be wondering why we use the term "relative" when talking about humidity. The reason is that humidity is the amount of moisture air can hold at any point in time. The amount of moisture air can hold is not constant. It is dependent on the temperature and air pressure. However, the amount of water in a room does not change with temperature and air pressure. For example, when you blow up a balloon you put both air and some water vapor from your mouth. Now if you put that balloon in the freezer the balloon will shrink because the air is colder, but the amount of water droplets in that ballon will not change. This is similar to how relative humidity works in your studio.
3) Where does humidity come from?So most humidity issues will come from people exhaling in your studio and fresh air being brought in from the outside. In the winter months your studio may be too dry and in the summer months your studio may be too wet depending on your climate.
4) How do you get the right humidity in your room?This is the main question and there are a couple answers depending on your HVAC system. First, let's learn about sensible cooling loads and latent cooling loads. Sensible cooling loads: measure the ability of your unit to cool the air in your studio. Latent cooling loads: measure the ability of your unit to remove moisture from the air. Now calculating those loads is best left up to an HVAC specialist or contractor with experience in HVAC installs. However, you still can ask if the latent cooling load with be adequate if you have an ERV pumping in X amount of air per minute and X amount of people in your studio. Some contractors will oversize units either to make more money or simply out of ignorance and this can cause problems with your latent cooling load. The reason is that a unit that is too big for your home or studio will run in short bursts. This starting and stopping of the system does not give the unit enough time for the coil to reach dew point and for the air to have enough time to cycle the room through complete air exchanges. (Gervais, 139). This means the air will not pass over that coil and drip into the drip pan removing moisture from the air unless the unit runs for a long enough time. All in all, it is important to communicate with your HVAC tech or even a couple different ones to get opinions on how big your unit should be to properly remove moisture from your house/studio and keep the relative humidity between 30-50% year round.
5) What about mini-splits?I am a big fan of mini-splits and energy recovery ventilators working together to heat, cool and provide fresh air in your studio without adding any unwanted noise. The downside to this system is the humidity control can be a bit tricky. Now, my Mr. Cool mini-split does have a "Dry" mode, which does help remove moisture from the air. In dry mode the unit will end up cooling your room a bit more to help control humidity. This can be great, but I have found that sometimes the room feels a bit too cold to get down to lower humidity levels. The ERV will bring in fresh air from the outside, but on super wet days here in Nashville that air is still fairly humid when it enters the studio.
6) Use a dehumidifierIt might seem overly simplistic, but you can use a dehumidifier to help with any extra humidity problems you may be experiencing. Yes, these units might not be whisper quiet, but they can run at night or when you are not recording. You can also design your studio to have an air exchange room where the room next to the studio has a dehumidifier and air conditioner in it and the air is then sent into your studio room. This is not always possible, but it does allow for quiet in your studio at all times regardless of humidity issues.
ConclusionHumidity can be an issue depending on your climate and time of year. The main goal is to keep relative humidity between 30-50% year round. Remember to properly size your HVAC unit to achieve proper latent cooling loads. If you need some extra help you can always run a dehumidifier when you are not recording to help remove moisture from the air.
Works Cited Gervais, Rod. “Chapter 7: HVAC Design Concepts.” Home Recording Studio: Build It like the Pros, Second Edition, Course Technology PTR, 2010. “Three Signs Your Home Has Poor Indoor Humidity.” Lennox, 3 Mar. 2020, www.lennox.com/lennox-life/comfort-matters/getting-comfortable/three-signs-your-home-has-poor-indoor-humidity#:~:text=The%20ideal%20relative%20humidity%20for,of%20moisture%20it%20can%20contain. | |||
29 May 2023 | How To Properly Caulk A Soundproof Wall | 00:11:57 | |
FREE Soundproofing Workshop: https://www.soundproofyourstudio.com/workshop Acoustic Caulk is a key material in soundproofing. It is used to seal all possible air gaps in your soundproof wall design. The internet is full of lots of ways to do this, but what is the best way for your soundproof wall? In this article, we will dive into how to properly caulk your soundproof wall assembly so that it is airtight and will not fail when you finish your soundproofing build.
1) Why Use Acoustic Caulk and Not Regular Caulk or Silicone?Let's start with why we use acoustic caulk in the first place. Regular caulk or silicone hardens when it drys and is prone to cracking. Acoustic caulk, on the other hand, remains flexible even once it has dried. This means the airtight seal you need will remain many years down the road. Using regular caulk to save money means you risk having small air leaks in your soundproof room that could lead to less isolation over time.
2) Which Acoustic Caulk Should You Buy?When it comes to soundproofing people have some very strong opinions. I used Green Glue's Noiseproofing Sealant (this is not Green Glue Noiseproofing Compound). I think it worked well. Now some other brands you can research are TMS Acoustic Caulk, Auralex Acoustics STOPGAP, and Tremco Acoustical Sealant. Don't lose sleep over which brand to choose. I might recommend the cheapest so you save some money. They all are acoustically rated and will do the job you need them to do.
3) Caulking Your Bottom PlateNow, there are a lot of different recommendations when it comes to caulking your wall. In my studio I did not caulk underneath the bottom plate and it was totally fine. However, according to the The Soundproofing Company and Everkem Diversified Products (sealant manufacturer) you should use three beads of acoustic caulk under your bottom plate, one under your first layer of drywall and one under your second layer of drywall. (The Soundproofing Company, Matt Everkemp Products). Below is a diagram from the Soundproofing Company Website that demonstrates this design.
*From the Soundproofing Company Website
Now, I used rigid sill plate gasketing, which is a fancy word for foam that protects your bottom sill plate from moisture and rot. This can help decouple a bit too although that is all theoretical and not lab tested. We could have added acoustic caulk under the sill plate gasketing to add an extra layer of air tight sealant, but I don't think it was necessary in my build. I build my studio on a single concrete slab and am not worried about noise coming up through the earth, the slab and into my studio. However, if you are worried about noise transfer through your floor or slab then I would add the extra acoustic caulk just for good measure.
4) Should You Leave A Gap Where The Wall and Floor Meet?This is a common question I see on the internet. In my opinion it depends. Again, in my studio I was not worried about resonances from my slab to my drywall, so we put the drywall right onto the slab and used acoustic caulk along the entire perimeter where the drywall meets the floor. I think this is totally fine in this scenario. However, if you are worried about flanking noise paths from the floor to your inside wall then I would employ a different method. To get maximum isolation from your floor flanking paths I recommend leaving a 1/4" to 3/8" (6-9mm) gap between the drywall layers and your floor. Put backer rod under the drywall to fill the gap and then seal it fully with acoustic caulk. This will help reduce vibrations from the floor to your inside wall and will ensure your gap is airtight. You should do this on your outer wall too.
5) Should You Leave A Gap In Your CornersThe next question you might ask is, should my corner drywall panels touch. The answer, you guessed it, is it depends. In my studio I didn't worry about leaving a gap in my corners because the room is a standalone structure in my backyard. However, if you are worried about vibration from one wall that may have a lot of sound behind it transfering to other walls then creating a gap could help reduce the transfer of sound from wall to wall. To do this you should leave a 1/4" to 3/8" gap (6-9mm) between your first layer of drywall. Then add backer rod and acoustic caulk to the gap. Next, add your second layer of drywall and leave the same gap. Add backer rod and acoustic caulk to this gap as well. This will ensure the drywall is not touching and transferring sound, but that the gap is airtight and not letting sound through.
6) Should You Leave A Gap Where The Wall Meets The Ceiling?This is a good question too. If your ceiling is built off your inside wall and is what I call an "independently framed ceiling" then you do not need to leave a gap. The reason is that the frame your drywall is attached to is not connected to the roof or floor above. This means no sound will transfer. If however, you are using ceiling hangers or hat channels for your ceiling design then I think it is a good idea to leave a 1/4" to 3/8" gap (6-9mm) between your wall and ceiling drywall. Do the same design we did for the corners. Hang your first layer of drywall on your ceiling. Then put backer rod and acoustic caulk in the gap. Next, hang your second layer of drywall and put backer rod and acoustic caulk in the second gap as well. This will ensure that sound vibrations traveling from your wall will not connect to the ceiling and sound from the ceiling will not transfer to your walls. Below is a diagram from Home Recording Studio: Build It Like The Pros by Rod Gervais. (Gervais 264)
ConclusionCaulking your perimeters and beneath your bottom plates is a good idea. If you are worried about flanking paths and noise traveling from your floor to your walls, your walls to your ceiling or your ceiling to your walls then you should leave a 1/4" to 3/8" gap (6-9mm) and fill it with backer rod and acoustic caulk. I hope this article helped clarify this confusing topic about properly caulking your soundproof walls.
Works Cited: The Soundproofing Company. "Soundproof a wall: Best (Level 3)." The Soundproofing Company, 24 May 2023, https://www.soundproofingcompany.com/soundproofing-solutions/soundproof-walls/spc-solution-3-double-stud-wall. Matt. "SIMPLIFYING SOUND REDUCTION: FLANKING NOISE AND ACOUSTICAL SEALANTS." Everkem Diversified Products, 9 Oct. 2017, https://everkemproducts.com/sound-reduction-flanking-noise-acoustical-sealants/. Gervais, Rod. Home Recording Studio: Build It Like The Pros. 2nd Edition, Course Technology Cengage Learning, 2011. | |||
05 Jun 2023 | Is Your Soundproof Studio A Health Hazard? | 00:11:10 | |
FREE Soundproofing Workshop: https://www.soundproofyourstudio.com/workshop If you don't build your soundproof studio correctly you may be introducing some health hazards into your space. In this article I will discuss three common issues with a soundproof room that many DIY builders forget to do that can lead to headaches, fatigue, fire risk, and mold sickness.
1) FirestopsWhen I work with my soundproofing clients I often find that they have not thought about fire stops. Fire stops are an important part of a soundproof room built using the double wall design. Without fire stops your double wall system acts like a chimney. A fire could start in the walls and expand up into the ceiling within seconds without anyone in the room even knowing there was a fire. The fire could then jump to other rooms in the house or building very quickly. To prevent this from happening we install firestops at the top of the double wall assembly to block the smoke and flames from entering other parts of your structure. The diagram below shows a typical firestop design.
Notice how the compressed rockwool and fire caulk create a sound barrier from the wood stud and 1/2" drywall. The drywall sits across both studs and seals the 1" air cavity between your two walls. When done properly a firestop will prevent flames from moving into your ceiling.
2) VentilationWhen you build an airtight room you must ventilate it with fresh air. To properly soundproof a room it must be airtight. This means that fresh air from outside the room does not enter into your soundproof structure. Mini Splits and home HVAC units do not provide fresh air unless you install a fresh air intake system. When building your soundproof studio it is very important to install some sort of ventilation system to provide fresh air (ideally from the outside) to your soundproof room. The reason we need fresh air in an airtight room is that there is a build up of C02 that accumulates in soundproof rooms. When we exhale we breathe out C02 and the build up of C02 has been shown to cause: headaches, dizziness, restlessness, a tingling pins and needles feeling, difficulty breathing, sweating, tiredness, increased heart rate, elevated blood pressure, coma, asphyxia, and convulsions. (Wisconsin Department of Health Services) Now, the amount of C02 directly impacts the health risk. In most soundproof rooms you would need to go to the bathroom before it became deadly. However, the fatigue, headaches and drowsiness are a real issue at much lower levels. Let's take a look at these numbers from the Wisconsin Department of Health Website: The levels of CO2 in the air and potential health problems are:
(Wisconsin Department of Health Services) In my studio I have a CO2 reader. When I first built my studio the levels would easily reach into the 1,000-2,000 ppm range when it was just me in the studio. When we had 3-4 people in there for a couple hours levels would reach around 2,000-5,000 ppm. This is all to say that you don't want stagnant stale air in your studio that leads to headaches, sleepiness and poor concentration.
3) HumidityLastly, an often overlooked concern is mold growth from high humidity levels. According to the North Carolina Department of Health and Human Services: mold will almost certainly grow if relative humidity stays at 70% or higher for extended periods of time (NC Department of Health and Human Services). According to Rod Gervais in his book Home Recording Studio: Build It Like the Pros, ideal relative humidity levels for comfort and your musical instruments should be in the range of 30-50% with 45% being ideal relative humidity (Gervais 136). When designing your soundproof studio it is important to think about how you can mitigate mold growth. The first way is to properly size your HVAC or mini split unit. An oversized unit runs on shorter cycles making it less efficient at pulling excess moisture out of the air. This will lead to high RH in your studio and home. The second way to remove excess water vapor in your room is to install a dehumidifier. I have a dehumidifier in my studio and it works great, but it is loud. During sessions I have to turn it off. A better solution is to install your dehumidifier in a separate room and connect the rooms using a baffle box. This way fresh dehumidified air can enter your soundproof room without the noise of the unit.
ConclusionWhen building a soundproof studio it is important to design for fire safety, healthy air and healthy levels of humidity. If you do not follow these guidelines then you run the risk of introducing serious fire risk, the potential for headaches and poor concentration as well as the risk for mold toxins in your studio. Now that you are aware of the risks make sure to design firestops, ventilation systems and humidity regulation in your studio. This way you will ensure you have a comfortable, safe and healthy environment to create music in.
Works Cited: “Carbon Dioxide.” Wisconsin Department of Health Services, 29 Mar. 2023, www.dhs.wisconsin.gov/chemical/carbondioxide.htm#:~:text=Exposure%20to%20CO2%20can,coma%2C%20asphyxia%2C%20and%20convulsions. Public Health, Epidemiology. “Mold.” NC DPH: Occupational and Environmental Epidemiology: Conditions That Promote Mold Growth, epi.dph.ncdhhs.gov/oee/mold/conditions.html#:~:text=If%20there%20are%20no%20cold,mold%20will%20almost%20certainly%20grow. Accessed 29 May 2023. Gervais, Rod. Home Recording Studio: Build It Like The Pros. 2nd Edition, Course Technology Cengage Learning, 2011. | |||
12 Jun 2023 | Should You Buy A Whisper Room Vocal Booth? | 00:15:55 | |
Free Soundproofing Budget Calculator: https://www.soundproofyourstudio.com/calculator I recently had someone in our community reach out about the Whisper Room Vocal Booth. I was curious to do a review and see if I could help them and you with some advice on is the Whisper Room Vocal Booth a good choice for your studio.
1) What Is The Whisper Room Vocal Booth?Let's start with an overview of what this booth is and how it is made. They come in two models for isolation needed. They have a single wall model and a double wall model. The double wall model will provide more isolation and should be used for loud bands or drummers and perhaps a producer with speakers and a subwoofer. The coolest part of these booths is that they can be installed quickly and moved to different rooms over time. A soundproof construction job is permanent and cannot be moved. Each Whisper Room booth comes with a door with a window and the option for ventilation. It also comes with some 2" thick Auralex foam panels to control reflections in your booth.
2) How Well Does It Soundproof?This is the number one question and the answer is okay depending on your needs. They say on their website that their booths are not completely soundproof, but do provide "outstanding sound isolation." This is true of all soundproof rooms. The question is how well do the isolate across the frequency spectrum. On their website they have a cool calculator to estimate the transmission loss (drop in decibels) at certain frequencies. The frequencies they measure for are 125hz-4000hz. This frequency range is the common range for the human voice, but it does not account for bass frequencies from speakers, bass guitar, and kickdrums that will easily reach below 100hz. For those low frequencies we don't really know how well the Whisper Room will perform. I recommend you play around with calculator. The important thing is to measure your room with a decibel meter app on your phone and learn what the general noise floor is in your room. For most homes this will probably be in the range of 40-70dB. You want to isolate for the loudest sounds. A good recording studio will have a noise floor of 30dB or less across the frequency spectrum. For purposes of this article let's say our loudest noises in our room are around 70dB. This is the sound of a vacuum cleaner. The Whisper Room calculator says you would get the following.
We can see that with the standard wall you get 27dB of reduction at 4k Hz which would mean your noise floor in the booth would be 43dB instead of 70dB at 4k. At 125Hz your noise floor in the booth would be 49dB. For reference a 10dB change is perceived as either a doubling or halving of loudness to the human ear. Now to put 43dB-49dB in perspective that is somewhere in the range of a library on the low end and a conversation in a home at the high end according to their website. Now if someone is vacuuming right next to your booth you most likely will not want to record. However, these booths probably are great for reducing isolation in an already fairly quiet environment like the inside of a control room, a TV studio or a house basement on a fairly quiet street. I don't think these booths would work well for drums, bass amps, or a studio with speakers that can easily reach below 125Hz. Lastly, they don't offer any STC ratings, which make it hard to compare to other soundproof assemblies.
3) How Much Does It Cost?This is the next logical question. They are not cheap, but neither is soundproofing a room. The Voice Over Deluxe Package is a 4ftx4ft booth with double walls and ventilation included and it costs $11,118.80. That does not include shipping or tax. To compare the cost of building your own vocal booth I am going to use my Soundproof Budget Calculator. To get the better isolation that their booths and build your own 4ft by 4ft booth I estimate is would cost $3,454.80. That is a difference of $7,664. Now, you are paying for convenience, you don't need to know how to build a soundproof booth, and you can have it delivered right to your doorstep. There is something to be said for how easy that is, but is it worth the extra seven thousand dollars? That is up to you to decide.
4) Do I Recommend You Buy A Whisper BoothFor most people, no, I would not recommend you buy a Whisper Booth. The ideal person who should get a whisper booth will have a large budget, not want to do any construction or deal with any design planning, only need the booth for voice over work and ideally live in a fairly quite house already. If you are in a busy office, on a super loud street or needing to isolate against lower frequencies then I don't think the Whisper Booth will do the trick. I think the Whisper Booth is a solid product with decades of experience, but it is a premium price on something many of you could do DIY and get potentially better results. Lastly, I think another downside to the booth is how it looks. If you don't like the look of their product then you don't really have a choice. If you build your own booth then you get the freedom to design it exactly how you want it.
| |||
19 Jun 2023 | Where To Buy Soundproofing Supplies In Europe | 00:12:04 | |
FREE Soundproofing Workshop: https://www.soundproofyourstudio.com/workshop Many Europeans in our community have commented that it is hard to source the right materials in Europe. In this article I will share some resources that I recommend for our European friends.
1) What materials do you really need?If you go to most soundproofing store websites they will have dozens of soundproofing supplies. The truth is you don't need much if you are building a soundproof room. Most of the stuff they sell is not really necessary, but does make them money. Here are the supplies you definitely will need:
Here are the supplies that you might need:
Everything else you see on their websites, in my opinion, is not needed for soundproofing a room. Pretty easy right? So in my reviews of these different online stores these were the materials I was looking for.
2) Noise STOP SystemsNoise Stop Systems is based out of the UK. They supply:
They do not have any door seals. I would recommend them as a possible choice for your soundproof supplier.
3) The Soundproofing StoreThey are another UK store. They supply:
If you need to get door bottom seals I would recommend this store. They are a good option since you can get pretty much everything you need from them.
4) Acoustic BlockThis is, you guessed it, another UK based soundproofing company. They supply:
I would only go with this store if the price is right. They don't have what most people will need.
5) Soundproof CowNow this is an American company, but they do ship internationally. However, you must call them for international orders. They supply:
6) Mason IndustriesWhen it comes to soundproofing products Mason Industries is the highest quality. I recommend their WIC isolation clip or DNSB clip for heavier wall and door assemblies. These clips are excellent choices as a sway brace for your double wall assembly. They have dealers in Europe where you can buy their products.
The main takeaway is to remember that most soundproofing stores what to sell you stuff. They can't make money off of telling you the best way to soundproof just the way that uses their materials. Be wary of any supplier saying you need a ton of materials when you know you don't. | |||
26 Jun 2023 | How Loud Is My Mr Cool Mini Split? | 00:05:10 | |
FREE Soundproofing Workshop: https://www.soundproofyourstudio.com/workshop In this podcast I am using my Decibel X app on my phone to record the decibel levels at various spots in my studio while the mini split is on, off and in silent mode. The goal of this video is to give you some solid numbers and video audio to base off your decision to purchase a Mr. Cool Mini Split. In my experience the mini split is plenty quiete for recording vocals, acoustic guitar and other softer instruments. I also give you a bonus set of videos showing how loud my ventilation system is. In the end I still recommend the Mr. Cool Mini Split in most studio builds because it works and is affordable. Yes, a ducted mini split would be quieter, but would also cost several thousand dollars more. | |||
03 Jul 2023 | What Is The Ideal Ceiling Height For A Recording Studio? | 00:15:39 | |
FREE Acoustic Treatment Guide: https://www.soundproofyourstudio.com/acoustic You may have visited some professional recording studios and noticed that the rooms had high ceilings, especially the tracking room. Now in your home studio do you need a high ceiling? In this article I will talk about why higher ceilings are beneficial and some of the room acoustic theory behind recording studio room design.
1) High Ceilings Are Great For Drum RecordingA very basic, but important reason large pro studios have high ceilings in the tracking room is to give the wave forms enough space to develop before hitting a surface and reflecting back to the microphones and your ears. This is especially true when recording drums or large ensembles like an orchestra. In most home studios an 8 foot ceiling barely gives you enough height to place the overhead mics. You will mostly pick up the cymbals in a lower studio and the reflections from the ceiling will create a "harsh" tone. This is a very practical reason for having larger ceilings, but what about the physics of room acoustics? How do room acoustics improve with higher ceilings?
2) Room ModesTo really grasp why higher ceilings are beneficial in a room, we must first understand some basic room acoustic physics. All rooms create reflections where sound waves bounce off of. When sound emanates from a source, say a speaker, the air in the room is excited by the sound waves. The sound travels in all directions from the speaker and bounces of the walls, ceiling and floor. When the sound bounces off the surfaces it then returns back into the room. The reflected waves then encounter new sound waves coming from the speaker and they interact with each other. The sound waves either create a boost because of constructive interference or they create a null known as destructive interference. These peaks and nulls in the sound waves create acoustic distortions. Now, there is a slight difference in how higher frequency sounds behave versus lower frequency sounds. Sound waves above 250Hz perform more like a "ray." Meaning they travel in a direct line and don't have as much energy as sound waves below 250Hz. Sound waves below 250Hz and especially below 100Hz have much more energy and have much longer wavelengths. These sound waves create what we call room modes. These room modes or are areas of high or low pressure due to those sound waves running into themselves after bouncing off your rooms surfaces. Okay, that was a bit complicated, but it is very important to understanding why high ceilings are important. The reason is that we ultimately want larger rooms to allow for enough space for those low frequency waves to fully form or at least form as much as they can before hitting a surface. Depending on the distance the waves travel from a source (speaker) and a surface (ceiling) the room modes will change.
3) Room RatiosThis brings us to the next point about ceiling height. The ceiling is only one part of the room. We must also consider the length and width of our room when designing a recording studio. Over the years some acousticians have come up with room ratios that create a pleasing acoustic environment for sound reproduction. These room ratios should be considered a starting point and are by no means the end all be all of acoustic design. You may be wondering as I did why we don't know the way to design the perfect room for a recording studio. After all, if we can measure room modes and use room ratios to reduce them why not build the perfect mathematically correct studio? The answer is that, acoustics is as much an art as it is a science. Just because one room sounds good to one person does not mean it will sound good to another. In fact, the way we perceive sound is uniquely human. We do not hear everything the way the math works out in physics. We hear how our ears and brain perceive sound in a room. This makes the job of designing your studio that much less precise, but also gives you the freedom to design a room that is pleasing and does the job you need it to. All this said, we can use room ratios to get us in the ballpark with a room that will have less acoustic problems and thus cost less to acoustically treat in the long run. Some common room ratios are from the acousticians, Sepmeyer, Louden, Volkman and Boner. Below is a diagram of some of their room ratios.
4) The Problem With Small RoomsNow you can use these ratios, but you are not guaranteed great results if your room is still small. The reason is that if your rooms dimensions are comparable to the wavelengths of audible sound then may have problems with "excessive separation between modes." (Everest,Pohlmann 261) The large separation between modes leads to unpleasant acoustic distortion in your room. To get uniform spacing between room modes and avoid coincidences (where modes pile up on top of eachother) you need more room volume. This means larger rooms are generally thought of as sounding better and are preferred for tracking rooms and control rooms. However, in control rooms the reverb time must be lower and all reflections must be treated to create a flat listening response. 5) ConclusionIt is very important to remember that "there is no ideal ratio of dimensions" for a room. (Everest,Pohlmann 256). As studio designers we can only create a good starting point and then measure and analyze the room once it is built. For most of you reading this, I would assume you are working with rooms you already have or may be able to build a studio in your backyard. Either way it is important to remember that the larger the volume the better your room will sound and if you use room ratios you will have a better starting point. In a basement studio this could mean building a wall in the existing basement to create an ideal room ratio. In a studio build in a backyard it could mean building a larger studio to help with even distribution of room modes and avoiding coincidences. To answer our original question. The ideal ceiling height is probably the tallest ceiling you can afford while making sure it fits within a good room ratio for the least acoustic distortions caused by room modes. In the end don't lose sleep over this, but know that understanding room modes is an important aspect of getting your room to sound as good as it can from the start.
Works Cites: Everest, Frederick A., and Ken C. Pohlmann. “Modal Resonances.” Master Handbook of Acoustics, McGraw-Hill, New York, 2015.
| |||
10 Jul 2023 | Soundproofing Your Home Studio 101 | 00:13:35 | |
FREE Soundproofing Workshop: https://www.soundproofyourstudio.com/workshop This week things are a little different. This video is actually the visual part of a blog article I wrote for the Sonicscoop blog. If you have not heard of Sonicscoop they are a great resources for all things home recording related. You can read the full blog article at - https://sonicscoop.com/soundproofing-your-home-studio-101/ 0:00 - Intro 1:44 - Soundproofing vs Acoustic Treatment 3:12 - The Three Pillars Of Soundproofing 5:36 - The Best Soundproof Floor 6:37 - The Best Soundproof Wall 8:14 - The Best Soundproof Ceiling 9:00 - The Importance of Fresh Air 10:07 - Soundproof Doors and Windows 12:46 - Conclusion | |||
17 Jul 2023 | What Are Noise Criteria Levels? | 00:10:01 | |
FREE Soundproofing Workshop: https://www.soundproofyourstudio.com/workshop
When designing a soundproof room, acoustic designers will use Noise Criterion Curves or NC curves for short to ensure the room meets proper sound isolation guidelines. In this article I will go over what NC curves are and how to use them as a guide for your own studio build.
1) What are NC LevelsNoise Criteria levels are benchmarks we can use to get our soundproof rooms to an industry standard. Here are some guidelines for NC Levels for various applications: NC 15-20: Broadcasting Studios, Concert Halls, Recording Studios and Music Rooms NC 30: Residences, Theaters, Libraries, Executive Offices NC 35: Private Offices, Schools, Hotel Rooms, Churches, Hospitals NC 40: Labs, Dining Rooms, General Office Use NC 45: Retail Stores, Lobby Areas, Reception Areas NC 50+: Computer Rooms, Print Machine Rooms Studio designer and soundproofing expert, Rod Gervais states that his goal when designing professional recording studios is to shoot for NC 20 or below and preferably NC 15 if possible. (Gervais 158) Each of these NC levels represents acceptable sound pressure levels at eight octave band center frequencies. Below is a diagram from Home Recording Studio: Build It Like The Pros by Rod Gervais.
Notice for a studio to fall in the NC15 range you must get 47 dB at 63Hz, 36dB or below at 125Hz and so on. Now that you understand the concepts behind NC levels you might be wondering how to calculate these levels in your own home studio.
2) How To Calculate NC LevelsNC levels are not easy to calculate without the right tools and experience. For this reason I recommend using the chart above as a guide and using your smart phone to record levels. Although, this is not a great method for professionals for the average DIY studio build getting some general ideas of how much isolation you need is helpful. I recommend using the DecibelX app. You can download it for free and can pay for an upgrade if you want. This app allows you to measure the average dB level in your room and you can see the dB range over the frequency spectrum. This will help you see where you may have potential problems in your soundproofing design. If you want a professional level test done then you will either need to hire someone with the right experience running NC level tests or rent the right gear and read the guidelines. The American National Standards Institute (ANSI) provides guidelines for getting accurate measurements. You can look those up at ANSI S1.13-1971 (R 1986) American National Standard Methods for the Measurement of Sound Pressure Levels (Everest Pohlmann 313). If you do your own measurements you will need to calibrate your SPL meter. You will also need a meter that can measure octave band frequencies and it should be mounted on a tripod for accurate results. As you can see, there is a reason professionals do this work. It must meet stringent standards to qualify as credible data. The choice is up to you if you want to try measuring NC level at all. I find the knowledge useful in understanding benchmarks for professional studio design, but probably overkill for the average DIY home studio build. Works Cited Everest, Frederick A., and Ken C. Pohlmann. “Modal Resonances.” Master Handbook of Acoustics, McGraw-Hill, New York, 2015. Gervais, Rod. Home Recording Studio: Build It Like The Pros. 2nd Edition, Course Technology Cengage Learning, 2011.
| |||
24 Jul 2023 | Should You Use HushFrame Rafts To Soundproof? | 00:11:05 | |
FREE Soundproofing Workshop: https://www.soundproofyourstudio.com/workshop A member of our soundproofing community recently asked me about a product called HushFrame Rafts. I had never heard of them before so I did some research. In this article I am going over the benefit of using HushFrame Rafts, the cost comparison to other similar products and what they are. 1) What Are HushFrame RaftsI am usually very skeptical about soundproofing products. These Hushframe rafts are interesting though. They are a wood isolator used to decouple drywall from walls and ceilings using hat channels or wood channels. One of the biggest benefits to Hushfram rafts is that you can use wood as a furring channel not just metal, and you can save some space when using the Hushframe Rafts. According to their website, HushFrame rafts use Vi-Bridge Technology to reduce noise transfer through the clip into your drywall. Now that sounds like some fancy naming for a patented technology. That is okay as long as it works. According to their website they can achieve 80% noise reduction, and an STC of 66. However, we don't know what 80% noise reduction really means, especially for bass frequencies and we don't know how the wall was built to achieve an STC of 66. All this said, I would trust that these clips do in fact decouple drywall when installed correctly. So next let's look at another comparable product.
2) How Do HushFrame Rafts Compare To Other Iso-ClipsNow the biggest difference in HushFrame Clips versus the IB-1 Iso Clips I used in my studio are price and the total depth of the clip. First, let's take a look at price. HushFrame Rafts are available at the ISOSTORE online for $4.95/clip. The iso-clips I recommend I found for $1.79 at Buildcorpdirect.com. The first important factor is to look at price. The A237 Resilimount Clip is $3.16 cheaper than the HushFrame Rafts. This could add up depending on how many clips you need. Most studios will need dozens of clips, so cost could be a factor. Second we want to look at the amount of space each clip adds to the wall assembly. The Hushframe Raft as you can see below uses up to 1" of space if using 3/4" wood furring or 1 1/8" if using 7/8" furring channel. Source Image: HushFrame Website Now if you are using the IB-1 or A237 Clip (they are the same with different names) then you will have a 7/8" furring channel sitting in the clip with a few 16ths of an inch below the furring channel. I am not 100% certain on that exact height but it should be around 1" to maybe 1" 1/8". Either way, I believe the space saved using the HushFrame Raft is pretty minimal. Below is a diagram of the A237 Clip: Now let's look at a diagram from the Soundproofing Company Website that shows different STC ratings using the IB-1 iso clips and 7/8" furring channel. You can see that if you use Green Glue between the layers and two layers of drywall with Green Glue on the backside you get an STC of 71. With one layer of drywall on one side and the hat channel system on the other side with Green Glue you get an STC of 67. If you use two layers of drywall without Green Glue you get an STC of 58. Those are all better than the HushFrame Rafts accept the STC of 58. However, remember we really don't know what wall system they were referring to. If you added another layer of drywall to the outside of the wall it would increase the STC regardless of your iso clip.
3) ConclusionWould I use the HushFrame Rafts in a soundproof studio build? Probably not because I can get the same STC rating using a cheaper clip and the space saved is pretty negligible. The only time I might recommend the use of Hushframe Rafts is to create a decoupled vent through your wall. I could see how using the rafts to build a custom ventilation system could be useful, but other than that I would stick with the cheaper clips and put your money on more drywall and Green Glue. | |||
31 Jul 2023 | Pressure Vs. Velocity Acoustic Absorbers | 00:10:52 | |
Free Acoustic Treatment Guide - https://www.soundproofyourstudio.com/acoustic When acoustically treating a room we have two major forms of acoustic treatment. The first method is using velocity absorbers and the second method is using pressure absorbers. To fully treat and balance a room we need to use both tools for two different purposes. In this article I will go over what each absorber is and how to use them.
1) Velocity AbsorbersVelocity absorbers are what you most likely think of when you think of acoustic panels. They use insulation and an air gap to absorb sound waves and reduce reflections back in your room. Velocity absorbers also include foam panels which absorb sound through transfer to heat much like fiberglass insulation.
2) How Are Velocity Absorbers UsedVelocity absorbers are great and affordable for treating your room, however they do have limitations. They are great at absorbing higher frequencies above 125Hz, but do very little at absorbing frequencies below 125Hz. The key attribute all velocity absorbers have is a porous composition. The air space within the material is what turns sound energy into heat because the fibers vibrate and create frictional resistance, which is then transferred to heat energy (Everest, Pohlmann 191). 3) Effect Of Thickness With Porous Velocity AbsorbersAccording to The Master Handbook of Acoustics, "there is little difference above 500Hz as thickness is increased (Everest, Pohlmann 195). However, there is "considerable improvement below 500 Hz as thickness is increased" (Everest, Pohlmann 195). A four inch thick fiberglass panel of 3-lb/ft3 density has nearly perfect absorption over the 125-4k Hz region (Everest, Pohlmann 195).
4) Effect Of Airspace Behind Porous Acoustic PanelsAdding a three inch airspace behind panels will increase its absorption. It is a best practice to leave an air gap between the fiberglass and your wall. In general the farther the panel is placed from the wall the lower frequencies it should absorb. As a general rule with velocity based traps a panel placed a 1/4 wavelength from the wall is where absorption is greatest (Everest, Pohlmann 195). For example, if we estimate the speed of sound to be 1,125 ft/second in our room then a 100 hz wavelength = 11.25ft (1,125 ft/sec / 100 Hz). A quarter wavelength of 100 Hz is then 11.25/4= 2.8125 feet. This would mean your velocity panel would need to have a nearly three foot air gap behind it to maximally absorb 100 Hz. Now most people cannot give up 3 feet on all their walls and ceilings to absorb down to 100 Hz. This is where pressure traps come in. However, before I dive into pressure traps. It is important to realize that velocity traps, although not efficient at absorbing sound below 100 Hz still absorb some in that area. This is very important because our goal as acoustic designers is to get the room as good as possible with velocity based absorbers as we can and then move to pressure based traps to sniper out some of the low frequency problems in our room.
5) What Are Pressure Based Absorbers?Pressure based absorbers also known as resonant or reactive absorbers use a different method than velocity absorbers to absorb sound. There are two main types of pressure absorbers: Panel or Diaphragmatic absorbers and Helmholtz Resonators. These two types of tools can pinpoint problem frequencies in your room below 125 Hz where our 4" thick velocity traps are not as efficient. Notice that I said pin point. The down side to pressure traps is that they have a narrow frequency band that they absorb. They can be tuned to attenuate specific problem frequencies in your room. For this reason, I always recommend that designers begin by treating their room with plenty of porous absorbers before going down the path of using pressure traps. Pressure traps are great at reducing room mode issues. Every room will have low frequency resonances that can muddy how we hear the bass in our room from what is actually coming out of our monitor speakers. In order to fix these low bass mud issues we can target a specific room mode issue with a tuned trap. 6) Panel (Diaphragmatic) AbsorbersPanel traps are great at absorbing lower frequencies. They are essentially a wooden sealed box with a layer of fiberglass inside. The mass of the panel and the air spring created will absorb sound as the material is flexed and vibrates. There is additional absorption through damping by the insulation (Everest, Pohlmann 195). Another form of panel absorption are Polycylindrical absorbers, which work the same as a flat panel absorber, but have the added benefit of creating a diffuse sound field because of their semi cylindrical bulkheads.
7) Helmholtz ResonatorsHelmholtz resonators are cylindrical tubes much like a bottle. They absorb sound by using the air in the cavity as a spring that creates a resonant system. Just like blowing across the top of a bottle produces a resonant tone, helmholtz resonators also have a resonant tone and absorption is maximal at that resonant frequency. Helmholtz resonators can be tuned to target specific problem frequencies in your room. I will say, in my research many people have warned that Helmholtz resonators are not easy to make and small errors in construction can render them useless. 8) ConclusionAcoustically treating a room is like an onion. You start on the outside and get good results and gradually work your way towards the center getting more precise and more complicated as you go. For most DIY studios using velocity based traps will go a tremendously long way towards fixing your room issues. I also love room eq software like Sonarworks Sound ID to correct your speakers to fix issues in the low end. This can help mitigate problems when you are mixing or mastering. However, once you get your room dialed in as best as you can with velocity porous absorbers, next you will need pressure traps to reach those lower problematic room modes. To find your room modes you will need to test your room using a measurement mic and software like Room EQ Wizard. This will tell you what is wrong at your listening position and what room modes are ringing out at your listening position. From there you can build pressure traps to target those specific problem frequencies.
Works Cited Everest, Frederick A., and Ken C. Pohlmann. “Absorption.” Master Handbook of Acoustics, McGraw-Hill, New York, 2015.
| |||
07 Aug 2023 | Why Room Ratios Don't Work...most of the time | 00:23:09 | |
Free Acoustic Treatment Guide - www.soundproofyourstudio.com/acoustic If you are reading this, you may be facing some room ratio madness yourself. If you are trying to find the perfect room ratio, reading obsessively about room modes and genuinely feel like you have gone down a rabbit hole then you are in the right place. In this article I will ease your stress around room modes, and room ratios and hopefully send you back out in the world with a plan for your home recording studio.
1) Why Room Ratios Don't Work...most of the timeRoom ratios were created to give acoustic designers (aka you) the ability to design rooms with relatively small volumes that will still sound "good." I write good in quotes because we can never achieve a perfect room. Even the best room ratios will have flaws that need to be addressed. This said you may have jumped on a few room ratio calculators on the internet and found that with your ceiling height the room ratio given leads to a very small room. This is a common problem with using room ratios in basement, bedroom or garage home studio designs. We are always held back by our ceiling height because the ratio is based off of ceiling height to width to length and a low ceiling height means smaller length and widths to meet the ratio numbers. Meaning, if we can't raise up our ceiling height we can't get a big enough room to do our work in. Totally maddening...I know! So what is the solution. Well let me tell you, but first let's learn what makes a room "good" to begin with.
2) What Makes A Room Sound "Good"There has been a lot of research on what makes a room sound pleasing or good to the human ear. This is a subjective term and has been argued over the years by some of the world's top acousticians. One thing that makes a room sound good is having what is known as an even distribution of modes. (Now I am not going to get into what a room mode is in this article, but if you don't know, take a break and google it real quick.) Okay great, so an even distribution of modes means that modes are spaced evenly through each 1/3 octave frequency band. The human ear perceives sound based on a logarithmic scale and acousticians have plotted frequencies based on this scale. The key here is to know how to read it, not try to fully comprehend the science. Next, another thing that makes a room sound "good" is to never have modes fall on top of each other. This means two different types of modes (axial, tangential, oblique) line up at exactly the same frequency thus causing that frequency to ring out more in your room making your room sound "bad." To do this I am going to show you a really good room ratio and a very very bad room ratio. This will help you see what an even distribution of modes looks like and what the lining up or coincidence of modes looks like. 3) Arguably, The Best Room RatioArguably, one of the best room ratios is Sepmeyer's first ratio of 1: 1.14 : 1.39. Now, we will see in a moment how best can be misleading, but stick with me here. The image below is from the AMROC room mode calculator. It shows Sepmeyer's first ratio with a ceiling height of 15 feet.
Now we don't really need to look at anything above 125 Hz. The reason is that we can easily treat those frequencies with velocity based acoustic panels. What is harder to treat are room modes below 125 Hz. Now what we notice first is that in the lower frequencies we have a relatively even spacing of room modes. That is good! In a second you will see what big gaps will look like. We also want to look at the Bonello chart. It shows a smooth increase in modes per 1/3 octave. That is also considered "good." If that number goes up then drops down, then your room will not sound as good.
3) Size Matters!I know I hate seeing that statement too, but in room acoustics the volume of our room also matters. You could use that awesome Sepmeyer ratio, but if you have an 8 foot ceiling it will not sound as good. Let me show you why. Below is another screen shot from the same Sepmeyer ratio we used on the 15 foot tall room. However, this chart shows the room modes for an 8 foot tall room.
At first glance they look the same, right? But wait! The relative distribution, meaning the spacing between the modes is the same, but where the modes fall on the musical scale has changed. In a smaller room those same modes have been shifted up in the low end. This means we have more problem modes in our audible bass frequencies than we did with the larger room. Notice how the first mode in our 15 foot room started well below 30Hz - barely in the audible spectrum of hearing, while that same mode falls at 50Hz in our 8 foot room, right in the middle of your kick drums thump! This is why bigger rooms meaning taller ceilings are better for music spaces. Because the problem modes get shifted lower and lower. This means treating our room becomes easier and less expensive because we have less low modal issues we need to smooth out.
4) A Truly Crappy Room RatioThe worst room you could possibly build is a cube. If the dimensions are 1:1:1 then your room will sound bad. Your room will also sound bad if you use even multiples like 1:2:3. So for the sake of learning how to read the AMROC calculator let's now look at that dreadful cube room.
Gross! I mean that is just repulsive looking. Okay I kid, but yes this room will definitely sound bad and will be difficult to acoustically treat. Why? Well, first we have large gaps between those modes in the low end. Notice how our 8 foot tall room above has more lines in the low frequencies. Well, that is a good thing and we want them spaced evenly. Next, the Bonello criterion shows that we have a drop in modes from 3 to 1 and then a huge jump to 12. Considering ideally we want those numbers slowly increasing or at least staying the same, this is also a problem. Lastly, we didn't talk about this yet, but notice how there are a lot of bunched up lines that are red, blue and purple in the Sepmeyer rooms? Notice also how they start bunching together at lower frequencies than the cube? The bunching of lines is what we want. That actually makes the room sound more smooth and even. The big gaps make the room sound wonky because certain notes are louder than others or they may disappear completely depending where you stand in the room. Ideally, our low end would have a ton of lines too, but we just can't get that due to physics. Bummer I know! So, a good room will have those bunched lines start clumping together as low as possible. This is known as the Schroeder Frequency. That is just a fancy term that states when your sound waves stops behaving like waves and act more like rays. We want the sound in your room to behave like a ray at as low a frequency as possible because it is easier to treat with velocity acoustic panels. So, all you need to know is that the lower the Schroeder Frequency the better. Simple! Okay, sorry if I lost you there, but all you need to know is: bunching together good. Bunching together at lower frequencies good. The more bunching the better and bunching evenly is the best! Yay! Lastly, in our cube room several of the modes in the low end happen at the same frequency. Remember these are bad and will mean certain notes in your room will ring out more leading to an uneven listening and recording environment. Ahhhh but, Wilson, I am still reading and you have not offered me a solution yet. I know, but I need to teach you how to read the calculator so you can move beyond the room ratios. More on that in a second. 5) What About That Pesky Bolt Area?You may have noticed a little box labeled Bolt Area in the bottom right of the diagrams I have shown you. You may also have noticed that none of the rooms I have shown you fall in the bolt area. First, The Bolt Area was a diagram created by Bolt (acoustician dude) who wanted to make it easy to find good room ratios. Before computers you could look at his graph and pick some room ratios that fit your design and would just hope that the room modes were evenly spaced. The problem is that people have found many room ratios in the bolt area that really are not so great. This lead to other graphs being created. Here is a super handy tool you can use to dive deeper on room ratio graphs. This link - https://www.acoustic.ua/forms/rr.en.html The link above will show you where your room ratio falls according to the Bolt Area, The European Broadcasting Recommendations and the IEC Recommendations for room ratios. On top of that the acoustician Trevor Cox did an analysis of rooms and found out some more cool stuff. He says that if your room falls in the gray or black area of the graph then you will have a nice room. If it falls in the white area then things will go south for you. Dang! Notice that the calculator has a drop down menu for "room cubing." Make sure to set that number to your rooms volume. So for our situation it should be at 100 cubic meters not 50. Let's take a look at our 15 foot Sepmeyer room on this calculator.
Now it's hard to see, but I think we fall on a grey area. However, we really don't fall within any of the other recommended areas. You can see how this is all maddening. Remember, these calculators are meant as tools and a guide. The best room for you will be one that has as smooth a mode spacing as possible, has a slowly rising mode count per 1/3 octave band, and most importantly is big enough for you to do the work you need to do in there. Conclusion - So What Now?I have just taught you how to read these calculators and diagrams. What I propose you do is put in your ideal dimensions and adjust those dimensions slightly to try and get your room to meet the criteria I mentioned. Stay away from 1:1:1 and 1:2:3 ratios. Another little trick if you have bad dimensions, say 8x8x8, is to increase and decrease two dimensions by 5%. So you could decrease the width by 5% and increase the length by 5% and your room would be much better. (Myth: Modes and Room Ratios: “I Have Too Many Modes! I Need a Better Ratio to Get Rid of Them” - Soundman2020 - Studio Design Forum) If you can raise your ceiling height do it. If you are building from scratch choose the first Sepmeyer ratio and move on. Or you could look at Louden, but don't get too hung up on it. If you use a room ratio you are light years ahead of most home studios. You could also choose to plot a room on the dark area of the Cox calculator. Then you could check it on AMROC and see how the mode separation looks in the low end. Then you could make sure it meets Bonello's Criterion. The goal is to do the best you can with what you have and not lose sleep over it. There is no perfect room. I repeat, there is no perfect room. Your design must use these tools and still meet your needs. My advice is to pick a room size as best as you can and move on. Don't waste weeks and weeks calculating room sizes. In the end you will still need acoustic treatment no matter what. One last thing...don't build a cube.
Works Cited Room Sizes Compliance With International Standards and Recommendations. www.acoustic.ua/forms/rr.en.html. “Amroc - THE Room Mode Calculator.” Mag. Andreas Melcher, amcoustics.com/tools/amroc. Myth: Modes and Room Ratios: “I Have Too Many Modes! I Need a Better Ratio to Get Rid of Them” - Soundman2020 - Studio Design Forum. digistar.cl/Forum/viewtopic.php?t=557. Everest, Frederick A., and Ken C. Pohlmann. “Modal Resonances.” Master Handbook of Acoustics, McGraw-Hill, New York, 2015.
| |||
14 Aug 2023 | Do Not Use Rockwool To Soundproof Walls | 00:10:00 | |
FREE Soundproofing Workshop: https://www.soundproofyourstudio.com/workshop Many people come to me saying they will use Rockwool to soundproof their walls. First, this is not really necessary. Second, if you build a normal wall with Rockwool it will only marginally improve the sound isolation. In this article I will argue why the cheapest insulation that provides adequate climate control for your location is the best choice for your wall.
1) Soundproofing Is All About SystemsWhen we build a soundproof wall it is soundproof because of the sum of its parts, not a single material. Many people believe that adding Rockwool, which boasts enhanced acoustic properties will help improve the STC rating on their wall. The truth is that is will mostly hurt your wallet without adding any noticeable change in sound isolation. Below is a diagram of several different wall designs.
Notice that the wall to the far right has the best sound isolation. This is due to the wall construction not the individual parts. To prove this interesting point, the wall the third from the left has an STC of 40. This involves the same 4 layers of drywall, wood studs, and insulation, however by moving the drywall to the two outside walls and leaving an airspace in the middle the STC rating improves by 23 points! My point is that the insulation is important, but not a huge game changer when it comes to soundproofing. What matters most is having some form of fiberglass insulation in the wall and building it the correct way so that you have a mass spring mass system.
2) Safe N Sound Does Not Have an R ValueSo the first thing that we need to do when properly insulating our walls regardless of soundproofing is to get the right R Value for our climate. Below is a chart for the USA for different recommended R Values depending on the region you are building in. Now this would be important for a stand alone structure build in your backyard, roof insulation, or any wall that touches the outside of your home or garage.
For example, my studio needs insulation on all walls and in the ceiling for walls that touch that outside. According to this chart, I could use R38 in my attic and R13 to R15 in my walls. We actually used R30 insulation for my entire studio build, so be sure to confirm with your contractor what is best for your specific build. The key point is that Safe N Sound is meant for interior wall construction only and does not have a tested R Value. This means is is created for sound control, but not holding in heat and air conditioning. This is a huge flaw for many builds and is one reason I don't recommend Rockwool Safe N Sound to my soundproofing clients.
3) Using Other Insulation Could Save You Hundreds of DollarsThe truth is that Rockwool is more expensive than most other insulations on the market. Now if you are not building a double wall or a wall using a hat channel system then by all means use Rockwool. It will help some with sound reduction. However, if you are building a true soundproof wall system then the Rockwool is a waste of money. Let's look at the costs comparison. Rockwool Safe N Sound - $0.95 per sq/ft (Home Depot in 2023) Owens Corning R13 Kraft Insulation - $0.55 per sq/ft (Home Depot in 2023) You save $0.40 per square foot which can add up. If you are building a 300 square foot studio with 10 foot ceilings then you would spend: Rockwool Safe N Sound = $1,045 Owens Corning R13 = $605 That is a savings of $440! Most people want to save money where they can during a big construction project. This is a place where that money could go towards another purpose. I always recommend spending more money on mass when you can. So putting that savings towards another layer of drywall would be far better spent than on Safe N Sound.
4) ConclusionDon't get me wrong, Rockwool is great for acoustic panels it just really doesn't help in a soundproof wall system. If you are building a wall in your home and you are not soundproofing that wall then use Safe N Sound. However, if you are building a recording studio or any serious soundproof room I do not recommend wasting money on Safe N Sound insulation.
| |||
21 Aug 2023 | How Much Does It Cost To Soundproof A Room? | 00:12:06 | |
FREE Soundproofing Budget Calculator: https://www.soundproofyourstudio.com/calculator If you are soundproofing a room one of the first questions you will ask yourself is how much will it cost. Unlike traditional construction, soundproofing requires some extra costs. I have a soundproof budget calculator that can help you figure out your soundproof room budget based on square footage or square meters. You can download the free soundproof budget calculator at this link: https://www.soundproofyourstudio.com/calculator
1) What Size Room Do You WantThe most important factor in building a soundproof room is the size. If you only have $10,000 than you will only be able to build a 100 sq/ft room. So, if you have a really tight budget your best bet is to compromise on space. I know...not what you wanted to hear.
2) What Makes Soundproofing So Dang Expensive!Regular construction say for a remodel in a home according to Forbes is $140 per sq/ft. (Bartolone) Soundproofing averages closer to $180 per square foot for new construction and $105 for an existing structure. Some of the construction costs are the same. You will need lumber for framing, nails, screws, drywall, electrical, heating and cooling, paint, trim, you get the picture. However, some costs are soundproof specific. These are things like:
These costs can add up and lead to a higher dollar amount on average per square foot for your build.
3) Let's Look At An Example Soundproof RoomMany people want to build a soundproof room in an existing structure like a basement or a garage. In this example we will have a 200 square foot room. If we type 200 into my soundproof calculator here is what you get: For ease of teaching, I only included one door in this example and there is not a window. You can add the square footage of any windows in your room and get an added cost. We can see in the right hand side, the the black box is for a studio built in an existing structure. I removed some of the costs for ground up build to give you a more accurate estimate. This includes:
We see that our total studio cost could be around $15,692.34. With a 20% buffer (which I highly recommend) you are looking at $18,830.81. Now is when you say you could do it for cheaper. That is totally fair. These were my costs and I surely may have paid too much in some areas. The labor includes paying my contractor $40/hour and occasionally some other labor at $15-25 per hour. So if you don't do any work yourself I guarantee it will cost more. I worked alongside my contractor on the entire project and did not pay myself so keep that in mind.
ConclusionSoundproofing a room correctly is not the cheapest endeavor. I created this calculator to give you a gut check before you build. My contractor had never built a studio before and he estimated we could build it for $20-25K dollars. In the end it costed closer to $48,000 when it was all said and done. Yeah...that one hurt a bit. I don't want that for you, so take my calculator seriously and then do your own research on costs before you dive in. Don't let a contractor with no soundproof construction experience say they can do it for less, because either they will do it wrong or have you on the line for way more money than anticipated. Just my words of wisdom from someone who has built and designed 5 soundproof projects and is always working on more.
Works Cited: Bartolone, Ginny. “How Much Do Home Additions Cost in 2023?” Forbes, Forbes Magazine, 30 May 2023, www.forbes.com/home-improvement/home/home-additions-cost/.
| |||
28 Aug 2023 | From Backyard Shed To Soundproof Studio - Part 3 | 00:06:36 | |
FREE Soundproofing Workshop: https://www.soundproofyourstudio.com/workshop This is the final installment of a soundproof studio built inside a prefabricated shed here in Nashville. There are two other videos that document the entire build. You can watch all of them at this link - https://www.youtube.com/playlist?list=PLZ5pr-thcSKymQJ80Vg4Y1hkJf_9_Zkcv | |||
04 Sep 2023 | Soundproofing Cathedral Ceilings | 00:06:16 | |
FREE Soundproofing Workshop: https://www.soundproofyourstudio.com/workshop In my studio I have cathedral ceilings, these may also go under the name vaulted ceilings. When you vault a ceiling you have to worry about moisture issues developing under your roof sheathing. In this article I will describe to of the best ways to design and build a soundproof cathedral ceiling. 1) The Traditional MethodThe traditional way to build a cathedral ceiling is to leave a space for an air vent between the underside of your roof sheathing and the insulation in the ceiling cavity. This allows air to pass under the wood sheathing and up through your roof cap vent, which prevents the build up of condensation under your roof. The best way to do this is to build soffits under both eaves that allow air to enter under the roof cavity up the vent air space and out through your roof cap vent. This is one of the best methods for venting cathedral ceilings, however, it is not the best method for soundproofing your cathedral ceiling. The reason is that that air circulation means the space above your drywall is open to the outside and sound will easily enter in.
I will say that I did this system in my studio and the soundproofing is still adequate, however, if I were to build my studio again I would use on of the following other systems to prevent moisture build up under my roof sheathing. 2) Using Spray FoamAnother option to prevent moisture buildup under your roof is to use spray foam on the underside of your roof sheathing. This means you no longer need to have an air space and you can close up your roof so that it is airtight. With soundproofing we always want our systems to be airtight. Using spray foam allows us to seal the entire roof cavity so sound will not enter. It is important to use closed cell spray foam. I also highly recommend you hire a professional who does this daily so that the job is done quickly and correctly. You want to make sure that the spray foam never touches your hat channels, acoustic clips or drywall.
3) Insulate The Top Of Your Roof SheathingThe third option to prevent moisture buildup under your roof sheathing is to add rigid insulation on top of your roof sheathing before you apply your shingles. This method will prevent the buildup of moisture under your roof. As with spray foam I highly recommend you find an experienced professional to install the insulation. Any small gaps in the insulation could lead to water damage over time.
ConclusionIf you want vaulted ceilings in your soundproof room make sure to use one of the methods I recommended above. Remember option 2 and 3 will give you superior soundproofing while option one may arguably give you better water vapor protection.
| |||
11 Sep 2023 | Building A Soundproof Studio In A Bedroom | 00:45:13 | |
FREE Soundproofing Workshop: https://www.soundproofyourstudio.com/workshop Some of you may know that I do Soundproof and Acoustics Consulting through my program The Soundproof Studio Blueprint. Recently, one of my clients Colin of Tone Lab Studios finished the program. We did a full podcast interview and video on his entire build. In this interview you will learn some of the key aspects of soundproofing an upstairs bedroom, the difficulties we faced and our solutions to those problems. Here is a list of minute markers in case you would like to jump around in the video: 0:00 - Intro 1:30 - Podcast Interview Start 2:50 - Soundproofing Goals 4:07 - Soundproofing Results 7:54 - Floating Floor Design 9:44 - Wall Design 12:42 - Doors 18:46 - Ceiling 24:10 - Ventilation 31:31 - Acoustic Treatment 42:40 - Work With Tone Lab
1) Soundproofing Goals and ResultsThe goal with Colin's studio was to soundproof enough so that his roommate would not hear him mixing and recording. In the end he is very happy with the results and says that the only thing you can hear is the kick drum. This is very normal for a second story soundproof studio. Without having a concrete slab it is very hard to stop those 40 Hz frequencies from the kick. However, we knew going into the design that we were working within the constraints we had which included having to float a floor and a tight budget.
2) Floating FloorBecause we were building on a second story of his home we had to float the floor. Below is a diagram of the type of floating floor method we used with some modifications.
This design uses a layer of 2" thick Corning 703 across the whole floor while leaving a 1" piece upturned around the edges. The key is to try and decouple your inside drywall and floor from the existing floor. To do this, I recommend using backer rod and acoustic caulk under your two layers of drywall and under the 1x6" baseboard. Remember this system is not perfect, but it was a solution given our budget and location of the studio.
3) Wall and Ceiling DesignColin did not want to lose too much space in his studio so we opted for using a hat channel system with acoustic clips. This made it so all of his walls were decoupled from the existing studs. We used two layers of 5/8" thick drywall on all the walls and ceiling. The hat channel and clips were also used to decouple our ceiling from the existing ceiling rafters. We did not use Green Glue to save cost, but if you have the budget I would put Green Glue on all the walls, ceiling and in between the two layers of plywood on the floor.
4) DoorsColin had 2 doorways. The first door way already had a place to frame in another wall in the bedroom making it a perfect rectangle. This allowed us to create a communicating door system with a sizable airspace in between. We used two solid core doors with Zero International seals all the way around each door. He also had a door directly in the middle of the back wall to a bathroom. We decided to use only one solid core door with the same seals on this door because the bathroom did not need as much soundproofing from his roommates.
5) Ventilation and Heating and CoolingEvery soundproof room needs a ventilation system. For Colin's studio we used a Fantech AEV 80 to supply fresh air from the outside to his new room and remove stale air. We ran the supply ducts through two baffle boxes in the attic that vented down into the ceiling. Because Colin's studio is in Colorado we did not need to worry about humidity issues with the ventilation system. To heat and cool the room we opted for a Mr. Cool Mini Split, which Colin could install himself. The Mr. Cool runs extremely quiet and is my number one recommendation for soundproof studios, especially budget conscious builds.
6) Acoustic TreatmentWe finished Colin's consulting program by designing and installing his acoustic treatment. I told him to build to giant bass traps in his front corners to help absorb frequencies down to 125 Hz. We added a ceiling cloud and panels on his side walls to create a reflection free zone for mixing and mastering. We added panels along the back side walls and back wall to help reduce reflections. In the future Colin can extend a cloud into the back half of his room, add bass traps along his back wall and build or buy pressure traps to help attenuate a room mode he had at 40Hz. We used Room EQ Wizard and a measurement mic to make sure his room was dialed in and we used Sonarworks to correct his speakers for any final issues he has in his room. In the end Colin says his mixes translate to the car and beyond and he can mix songs with greater accuracy and speed than he ever could before! If you want to see if the Soundproof Studio Blueprint is the right fit for you then please feel free to fill out an application here: Soundproof Studio Blueprint Application. | |||
18 Sep 2023 | How To Soundproof Exterior Walls | 00:12:00 | |
FREE Soundproofing Workshop: https://www.soundproofyourstudio.com/workshop I have gotten so many questions about how to soundproof the outside exterior wall of a double wall system. This makes sense since all the double wall diagrams show two interior walls with sheetrock on both sides. This leads you to wonder, well how do I replace the sheet rock with an exterior wall material and still have it be soundproof? In this article I will answer exactly that question.
1) Double Wall ConstructionFirst, let's take a brief look at how our walls are constructed to help us understand how we can modify this design. A typical interior double wall will have two layers of 5/8" drywall on a wood or metal framed stud wall. Then there will be at least a 1" air gap. After that there is another wood or metal frame wall. Insulation is installed in the wall cavity either filling both framing bays or having insulation in the bays of each wall. Either is fine. Lastly, the outer wall has 2 layers of 5/8" drywall. This is your typical double wall design and it would look something like the far right wall design in the diagram below:
This gives you an STC of 63 and everything is great, but what about if that left or right side of that wall is an exterior wall. You can't just put drywall on the outside of a building, so what are you to do?
2) How To Soundproof Exterior WallsSo to solve this problem we just need to understand some soundproofing theory. The reason we use 5/8" drywall is twofold. First, it is relatively cheap and is a common building material. Second, it has mass. It weighs 2.2lb per square foot whereas 1/2" drywall is much lighter. Knowing that our inside wall will weigh 2.2lb per square foot per sheet of 5/8" drywall we can do some super simple math and know that our inside walls weights 4.4lb per square foot. Instead of focusing on the drywall, the key is to focus on the mass of the wall it self. Now we can build our exterior wall knowing it needs to be 4.4lb per square foot or more.
3) A Real World ExampleIn my studio, most of my walls are exterior outside walls, meaning they face the outside. This means my second wall has one layer of 9/16" sheathing and one layer of hardy plank siding. Let's calculate how much that weighs. 9/16" Sheathing (nominal 5/8") = 66.37lb (4'x8' sheet) = 2.07lb per square foot *(jonathan) Hardy Plank Siding = 2.3lb per square foot *(James Hardie® Siding FAQs - Homescapes of New England: 603.734.4282) This means my total outside wall mass or weight = 4.37lb per square foot. This is just shy of my inside wall mass, but actually worked out perfectly. Now, I will be honest. I did not think about any of the math when I was building my studio. It was my first studio build and I really didn't know what I know now. So, to save you some trouble simply match your studio mass on both walls. Easy and you don't have to overthink it. 4) But What About Green Glue???Yup, I knew we had to go there next. So, if you use Green Glue on your inside wall you certainly could use it between your sheathing and outside exterior siding. This would guarantee you have equal walls. I did not do this in my studio and I don't really need it. You could also say that Green Glue is adding soundproofing to your inside wall and thus add more mass to your outside wall. How much mass, well that is up for debate. At one point Rod Gervais had said that GG is like having four layers of drywall. He has since pulled back that claim, but it is adding to transmission loss, especially at low frequencies. My advice, would be to not obsess over these minor details. Green Glue or no green glue, mass is still more important in my humble opinion. Focus on the mass and then add Green Glue if you want that extra boost. 5) But wait...Wilson, my walls are too thin on the exterior.If you are building in an existing structure then your walls may not have much mass. A shed or garage may have thin low mass construction. In this case you can add mass as long as the structure can handle it. You can add drywall to the inside of the exterior wall or add more mass to the outside. How you do it is not as important as that you do it and the mass is correct. That magic 4.4lb per square foot is your mark. That is the number that matters on both walls.
Works Cited: James Hardie® Siding FAQs - Homescapes of New England: 603.734.4282. 26 Mar. 2010, www.homescapesofne.com/services/information-about-james-hardie-siding/#:~:text=Hardieplank%20weighs%202.3%20lbs%20per. Accessed 12 Sept. 2023. jonathan. “How Much Does OSB Weigh? (+ OSB Weight Calculator).” ToolCrowd, 17 Oct. 2021, www.toolcrowd.com/how-much-does-osb-weigh/#google_vignette. Accessed 12 Sept. 2023.
| |||
25 Sep 2023 | Top 5 Soundproofing Mistakes | 00:13:45 | |
FREE Soundproofing Workshop: https://www.soundproofyourstudio.com/workshop When we start to design a soundproof home recording studio there is always a deep fear in the back of our minds. What if I spend all this money and then it is not soundproof enough? In this article I will talk about the 5 biggest soundproofing mistakes you can make and how to avoid them.
5) Use The Wrong Glass In Your WindowsIt is so tempting to buy a pre-hung window from a window supplier when building your studio. It is cheaper and easier than building your own windows or buying expensive soundproof windows. However, this is a corner you don't want to cut! I have heard of many people buying casement windows, double glazed windows, tripple glazed windows and all sort of designs to try and save money thinking it will be good enough. The problem is that most windows use float glass and float glass is not a good sound insulator. For soundproof windows we want to use tempered glass and/or laminate glass and we need a large airgap of at least 4" and two differing, but thick pieces of glass. Below is a simplified diagram of the windows in my recording studio.
4) Only Putting In One DoorIn my studio I used a design by the studio designer, Rod Gervais. He recommends that you can build a single soundproof door rather than having two communicating doors. Having built the single door I do not agree with him. I now believe that all soundproof doors, especially to the outside must be double communicating doors. See the diagram below.
By using two doors we can maintain the mass, air gap and decoupling needed to properly maintain the STC rating of our wall where the door is placed.
3) Think You Must Use MLV or Green GlueThere is so much talk on the internet arguing over should you use mass loaded vinyl, Green Glue or even carpet glue between you two layers of 5/8" drywall. I have taken the stance that MLV and Green Glue are nice to have and may increase the isolation of your wall, but they are not critical to the isolation of your wall. This is important to understand, because many people come to me and think they must use Green Glue. My response is always, well what is your budget. If they cannot afford Green Glue then I recommend not using it and simply doing two layers of 5/8" drywall on each side of their walls or even 3-4 layers if that is cheaper. MLV and Green Glue provide damping. Damping is a form of friction that turns sound into heat. This added physical phenomenon in your walls is a good thing, but as I said before a double wall without Green Glue or MLV will still give you an STC of 63, which is plenty good for a home recording studio.
2) Don't Know Your Budget Before You BuildWe all think we know a person who has a great deal on materials. Everyone has a brother-in-law who is really handy with construction and everyone underestimates how much their soundproof studio will cost. Before you begin building it is extremely wise to open a spreadsheet and input all the materials and labor costs for your studio to see if you can afford to build one. Most people look up a couple costs, try and estimate and don't really know how much their studio will cost in the end. Then half way through the project they are already over budget. At that point it is too late to find places to cut costs and they are stuck footing the bill for something they cannot afford. Don't be this person. Get accurate estimates and costs before you build and then add 20% on top of that estimate and that will be a healthy budget for your studio. Yes, it will be more than you expected, but it will be more accurate in the long run. Plus, wouldn't it be nice to finish under budget for once?
1) Forget To Install VentilationThe number one thing I see home studio enthusiasts do is forget to design and install a ventilation system in their studio. You can have the most soundproof studio in the world, but if it does provide fresh air and circulate out stale air then it is not going to be a good space to work in. Ventilation means fresh air exchange. It does not mean heating and cooling. Those are usually two seperate systems in a build. They can be combined, but they don't have to. Your air handler in your house will take the internal air and heat and cool it. It does not take outside air and condition it unless you have a system to do so. In a soundproof room the room is airtight. Unlike our houses where there are cracks and windows, and small openings where air can get in and out, our studio does not have those. We need a way to bring in fresh air and remove C02 laden stale air. To do this I recommend using and ERV or HRV. Both units will pull in fresh air from outside and pump into your studio, while removing stale air and pumping it back outside. The catch is we also need to silence the ducts and air flow in and out of our studio. To do that we add in a baffle box system so sound and the air flow do not create unwanted noise in our studio.
ConclusionI hope this article was helpful in addressing some of the major mistakes people make when trying to soundproof a room. Now that you are aware of them you can dive deeper into how to create solutions to avoid these soundproofing pitfalls.
| |||
02 Oct 2023 | This Soundproof Material Blew My Mind! | 00:13:10 | |
FREE Soundproofing Workshop: https://www.soundproofyourstudio.com/workshop Recently, a member of our community asked me to make a video about ICF or Insulated Concrete Forms. I had never heard of it and so I did some research. I was pleasantly surprised to see that ICF would be a great building material for soundproof home recording studios. Let me tell you why.
1) Why ICF Is Great For SoundproofingICF is a construction technique where concrete is poured into pre-fabricated blocks, kinda like lego blocks. These blocks are made out of styrofoam and are hollow to allow for concrete to be poured in. They are essentially a 6" to 12" concrete wall that is relatively easy to build and offers insulation as well as durability. So for soundproofing the styrofoam is not that important. What is important is the mass of the concrete itself. According to one ICF producer, LOGIX ICF, you can get blocks in foam to foam dimensions of 4"-12." All budget aside, the 12" blocks would be the best and the 4" blocks the least best. Below is an image from LOGIC ICF of their block system.
According to Jenkins Design Build, ICF has a consistent STC rating of 54. That is really good for just one wall (Solutions and Technology). Now I would still recommend framing an inside wall with a 1" air gap, but you wouldn't need MLV or Green Glue and you would be fine with the standard two layers of 5/8" drywall. I would imagine drummers, loud bands and most home studio enthusiasts would be blown away by this type of design. Another benefit to ICF is that the blocks fit together seamlessly and are therefore air tight. This is another benefit to soundproofing and recording studio design. Lastly, let's look at another source just to understand how soundproof a concrete wall really is. According to the Master Handbook of Acoustics, two 6" concrete walls with 6" air gap will give you an STC rating of 59. That is without fiberglass insulation in the middle, which would increase isolation. A single 12" concrete wall would give you an STC rating of 51. The air gap and insulation is still a critical part of your soundproof wall system. (Everest, Frederick A., and Ken C. Pohlmann) As a side note, concrete and brick massive, but do have the drawback of transmitting impulse noise easily. This means if you tapped on your concrete wall with a hammer, the sound would ring clearly on the other side. This is another reason the air gap and double wall system is desirable.
2) Other Benefits of ICFBeyond soundproofing it is important to see other benefits to ICF. First you may save 2-4 months in construction time on a new build because the blocks fit together so easily. You may also save money on heating and cooling your structure. Jenkins Design Build estimates you may save 25-50% on heating and cooling costs. According to Marion Saxton with Ph.D. in Environmental Design and Planning, ICF can last up to 100 years, it does not need a vapor barrier, and it can save anywhere from 4.8%-14% in energy consumption over a 70 year lifespan. Both Saxton and Jenkins Design Build mention the benefits of ICF for homes prone to natural disasters like fire, hurricanes and flooding. (“Myth Busting: How Sustainable Is ICF Construction?”) 3) The Downsides To ICFYou may wonder why all homes are not built with ICF. There are some downsides. The first is the added upfront cost of building with ICF. According to Saxton, ICF cost around $150 per square foot. She also notes you will spend around 5-10% more in total construction costs than a wood framed house (“Myth Busting: How Sustainable Is ICF Construction?”). According to Jenkins Design Build, ICF costs have just about caught up with wood frame construction. They say ICF blocks cost around $3.50 to $4.00 per square foot plus the added cost of concrete, rebar and labor costs. They say this still can add 15-20% more than stud framing, however, the total cost over time may be better with ICF (Solutions and Technology). Another downside to ICF is it is not DIY friendly. Whereas the average homeowner can learn to frame walls, it is not easy to learn how to install ICF. From my own research it would be wise to hire a contractor who has experience building with ICF to save you time and money in the long run. This means you might be limited by budget and availability in your area.
ConclusionWould I recommend using ICF? Yes, 100% if you can find a contractor and a quote that fits your budget. I feel ICF is a great choice for people looking for a way to build studios in their backyards. It doesn't work as well in basements and garages and for those people I would still recommend using a double stud wall system. The downsides don't seem to out weight the upsides in my experience and ICF seems especially appealing for studio designers. I look forward to hopefully designing and building a home studio with ICF in the near future and will let you know what I think.
Works Cited Everest, Frederick A., and Ken C. Pohlmann. “Sound Isolation: Walls, Floors and Ceilings.” Master Handbook of Acoustics, McGraw-Hill, New York, 2015. “Myth Busting: How Sustainable Is ICF Construction?” Rise, 28 Aug. 2017, www.buildwithrise.com/stories/mythbusting-icf-sustainable. Standard | Logix ICF (Insulated Concrete Forms). logixicf.com/products/standard/. Accessed 29 Sept. 2023. Solutions, Bethany Jenkins under Home, and Technology. “Insulated Concrete Forms: Pros and Cons.” Jenkins Custom Homes, 8 May 2020, newhousebuilder.com/insulated-concrete-forms/. | |||
13 Oct 2023 | Should You Use SilentFX Drywall To Soundproof? | 00:11:33 | |
FREE Soundproofing Workshop: https://www.soundproofyourstudio.com/workshop There are several acoustic drywall brands on the market and one is SilentFX by Certain Teed. This is a Saint Gobain company who also make Green Glue. In this article I will go over the pros and cons of using SilentFX drywall in your soundproof studio build.
1) What is SilentFX DrywallAccording to Certain Teed, "SilentFX Noise-Reducing Gypsum Board is specifically designed to reduce airborne sound transmission between two adjoining spaces when used in wall or floor/ceiling assemblies." They go on to say that, "SilentFX features a viscoelastic polymer that dampens sound energy. Application of the viscoelastic polymer between two specially formulated dense gypsum cores results in a combination that significantly improves sound attenuation and is ideal for systems requiring high STC performance." It is important to note that Green Glue and Mass Loaded Vinyl are both used to dampen sound energy as well. This middle layer viscoelastic polymer in SilentFX is meant to replace the need for Green Glue or Mass Loaded Vinyl.
2) What Is A Viscoelastic Polymer
According to a paper from Taiyuan University of Science and Technology, "The viscoelastic damping layer, most of which is rubber or rubberlike polymers, represents hysteresis under a dynamic load. Part of the mechanical energy is absorbed and finally dissipated as heat due to the internal friction of the molecular chains." So, in plain english, these means that the material vibrates in such a way that acoustic energy is transformed to heat, thus eliminating some of the sound or noise coming through your wall.
3) How Does Silent FX Compare to Regular DrywallOne of the best ways to soundproof a wall is to build a double wall system with an air gap in between the two walls. This system involves two layers of 5/8" drywall on either side of each wall. The STC rating you get from this design is 63.
According to Certain Teed's technical data sheet their equivalent double wall system gets an STC rating of 62. Their wall uses one layer of 5/8" on one side and a layer of 5/8" SilentFX drywall with a layer of 5/8" type X drywall on the other side. The biggest difference between the two wall designs is one has two layer of 5/8" on each side while the Certain Teed wall uses three layers with one being their patented SilentFX drywall.
4) What Is The Cost Difference Between SilentFX and Regular Drywall?SilentFX costs $73.01 per 4x8ft sheet. This is from Campbell Supply Company. (“5/8" Acoustic Drywall, Silent FX”) Type X 5/8" drywall costs $17.87 for a 4x8ft sheet. The cost of installing a the Certain Teed double wall would be a total of $126.62. The cost of a double wall without Silent FX would cost you $71.48. That is a difference of $55.14 and you are not getting a better STC rating.
ConclusionI wouldn't recommend SilentFX drywall for most home recording studios. It might be helpful if you are building a normal wall system and want some added acoustic benefit over regular drywall. However, the cost of acoustic drywalls like SilentFX never seems to justify the added acoustic benefits. For this reason I never recommend specialty drywalls to my clients. I always like to stick with regular Type X 5/8" drywall. You get the better results for less money.
Works Cited: “5/8" Acoustic Drywall, Silent FX.” Campbell Supply Company, campbellsupplycompany.com/5-8-acoustic-drywall-silent-fx/. Accessed 2 Oct. 2023. Wang, J.; Sun, D.; Liu, S.; Zhang, X. Damping Characteristics of Viscoelastic Damping Structure under Coupled Condition. Math. Comput. Appl. 2017, 22, 27. https://doi.org/10.3390/mca22010027 Websites Referenced: https://www.certainteed.com/resources/CTG_2480_SilentFX_Brochure_Eng.pdf https://www.homedepot.com/b/Building-Materials-Drywall-Drywall-Sheets/5-8-in/N-5yc1vZbb52Z1z0ppqa
| |||
16 Oct 2023 | How To Fix Low Frequency Problems - Panel Diaphragmatic Absorbers | 00:15:18 | |
FREE Acoustic Treatment Guide: https://www.soundproofyourstudio.com/acoustic Low frequency issues are the biggest problem for soundproofing and acoustically treating a room. In this article I will discuss how to treat low frequency issues below 125Hz in your room using panel bass traps.
1) What Is A Diaphragmatic Panel Bass Trap?Low frequencies below 125Hz are hard to treat with acoustic panels made from fiberglass batts. To treat these lower frequencies we need a different tool. The best tool for the job are pressure traps that use a closed air space to attenuate low frequencies. These traps are efficient at reducing low frequencies, but they have a narrow Q, meaning they only work in a narrow frequency band. For this reason I only recommend building these traps after you have extensively treated your room with velocity traps aka insulation with fabric over it. The bass trap I will be discussing has many names ranging from diaphragmatic absorber, low-bass panel trap, resonant absorber and so on, but the theory remains the same. These traps use an enclosed box with a calculated airspace depth to create a resonant chamber that attenuates bass at a specific frequency. To calculate our panel mass and depth we need to use the following formula to ensure our bass panel trap will attenuate the correct bass frequency. The formula is as follows: f (frequency) = 170 / square root of (mass x depth) *For metric change 170 to 60 - m = mass is in pounds per square foot of resonate panel d = depth in inches
Now the easiest way to calculate potential panel depth and materials is to create a spreadsheet for plywood thicknesses and depths and see what materials you need and depth you need to attenuate the correct frequency. Adding loose glass fiber to the back of your panel will increase absorption, but it also will move the peak absorption lower down the frequency spectrum. These panels are only effective when placed at a pressure maximum in your room for the desired frequency you are trying to treat. This means that you need to find out where a room mode is ringing out in your room and place the panels on that wall or ceiling. To do this you can use a calculator like, AMROC online to see where room modes in your room are, or you can play a sine wave through your speakers and walk around the room noting where the bass note sounds louder or completely gone. The places where the bass notes are louder is a pressure maximum and is where you should place a trap. Lastly, it is important to make each panel absorber at least 5 sq/ft to have an affect on the room. You will need to place one or two in your room to and re-measure your rooms response to see how many absorbers you will need.
2) So What Frequencies Do You Need To Treat?This is a good question. We know we have bass problems in our room, but now what? First, you need to measure your room. You must use REW or equivalent room software and a measurement mic that is properly calibrated to measure your room. This will show you what frequency problems you have in the low end. Let's use my studio as an example. Below is a picture of my REW results for the spectogram. I like to look at the spectogram because it shows which room modes are "ringing" out in my room at my listening position. Notice how most of my room is flat in the upper frequencies, but down low we get those flame like peaks. Those are my room modes ringing out where I mix. This will make my bass a bit muddy to hear since those frequencies don't decay at the same rate as ones nearby. The solution is to build traps that target those frequencies. It is analogous to a sniper rifle vs a shotgun approach. The panel trap can isolate those problem frequencies. So, the first ring out is at 106 Hz. Let's now look at where to place that panel.
3) Where To Place Your PanelsAs I mentioned before, you can use AMROC or sine waves to find your pressure maxima at 106Hz in my example. For this example I will use AMROC to show you where that frequency modal issue is at a maximum. That 106Hz frequency is a tangential and oblique mode that is maximul at the blue and red areas on the Room 3D visualizer on AMROC. AMROC plays the tone when you hover over it so I also could hear a huge peak in the middle of my back wall. To treat this frequency I would build probably build a 2x4' trap and place it in the middle, bottom or top of my back wall. Let's now look at what mass and air depth I need to treat that 106 Hz frequency.
4) Calculating Box DepthBased on the math here we know that the thicker the plywood the thinner our box can be. I like saving floor space so I was going to use 19/32 OSB Sheathing. This is affordable and readily available at my hardware store. 19/32 OSB weighs roughly 2 psf. This means we have to do a little algebra to solve for the depth. 106hz = 170/ square root (2 * d) square root (2*d) = 170/106 2*d = 1.6 squared 2*d = 2.56 d = 1.28" The answer ends up being 1.28 or 1 9/32". Yay! Okay so we have our box depth, now let's design the box. *it is a good idea to weigh your panel before building just to double check the math is correct. **You could use 2 lb MLV and absorption would be greater, since a limp mass membrane will add to absorption through damping. I might do this depending on cost and availability of 2 lb MLV.
5) How To Build The PanelOkay we did our room analysis, we did some math, we got our panel material, now it is time to build this bad boy. Here is a mock up I did of how I would build a trap to have a center resonating frequency of 60hz.
With a 106 Hz panel like in our example the box is so thin that I would forgo the insulation or use really thin insulation. With lower frequencies you can use the Corning 703 or a similar insulation to help improve absorption. Make sure to acoustically seal all corners with your MDF to make sure the box is truly airtight. When finished you can test the box using a sign wave at the resonant frequency you were hoping to absorb. Ideally you will feel the panel vibrate at that frequency.
ConclusionBass trapping is much more labor intensive than velocity traps, but you can really tighten up your low end if you put them in the right spot and build them correctly. In the end you may want to buy a pre-made panel. Either way, remember to fully treat your room with normal acoustic panels before attacking your low end.
| |||
23 Oct 2023 | Tame Low Frequency Issues In Your Room | 00:11:25 | |
FREE Acoustic Treatment Guide: https://www.soundproofyourstudio.com/acoustic Do you have mixes that alway have too much or too little bass? Does your low end sound muddy on your speakers? Most rooms have low end problems and even acoustic panels cannot fix them. We need low frequency pressure traps to attenuate low frequencies. This article focuses on one such bass trap known as a corner slot resonator. It is fairly easy to build and give fairly broadband absorption down to the low bass frequencies in that 20-50hz range.
1) Corners Are Where Bass Builds UpThe corners of the room are where most bass builds up and is therefore the best place to absorb all modal problems in your room. By putting a slot resonator in your corners you can target problem frequencies in your room. Now, notice how I said target frequencies. These acoustic bass traps are built custom to your room, so you need to know what frequencies are causing issues. To figure this out you need to measure your room using a measurement microphone and a software like REW. I go over this in other posts, so check that out before continuing.
2) How To Build A Slot ResonatorOnce you have measured your room and found some offending low bass frequencies also known as room modes, then you are ready to attack them! Okay, just absorb them, but let's look at how to do that. A slot resonator is a form of Helmholtz resonator. These resonators use airspaces between wood slats and a depth behind that slat to attenuate bass. Here is the formula to figure out the depth of your corner trap, the width between your wood slats and the depth behind the wood slats. f = 2160* square root r/((d*D)*((r+w)) f = resonant frequency r = slot width w = slat width d = Effective depth of slot (1.2 times the actual slat thickness) D = depth of box to the inside slat face Now, the best thing to do is plug this equation into a spreadsheet to solve for the frequencies you want to attenuate. Another option is to use an online calculator like this one: https://www.acoustic.ua/forms/calculator5.en.html For a diagonal trap in a corner your slot depth will very with each wood slat and you can vary the width between slats. The trap I have shown above has a center depth of 1' 7 1/4" with a 1/16" width between the 1x6" wood slats, which will attenuate at 46Hz. For my clients building home studios I like to build these traps custom so that each slot width and depth is targeting a specific problem frequency in their room. This will help get a smoother bass response at their mixing position. Designing these traps in 3D CAD program will allow you to accurately measure and design your traps to the 1/16." Accuracy is important with these traps since, a 1/16" difference can changer your resonant frequency by 20 or more Hz.
3) The Overall DesignStart by building a frame using 2x4 lumber for the bottom, sides and top plate. Then put in a 2" thick piece of Cornings 703 Insulation. Place fabric over the insulation and wood frame. This should be fabric you can breath through and feel air on your hand on the other side of the fabric. I recommend Guildford Of Maine's acoustic fabric. Last, you will attach the 1x6" wood slats to your frame on top of the fabric. The width between your wood slats and the depth behind the inside face of each slat will determine the resonant frequency your trap will absorb. Below is a diagram of how to build these traps.
ConclusionIf you want to reduce low bass frequencies in your room and have a fairly broadband trap than these slot resonator corner traps are a great cost effective solution. Just take care to measure carefully and do the math to get the trap as accurate as possible so it absorbs the frequencies you want it too.
| |||
30 Oct 2023 | My Simple Soundproofing Method | 00:07:48 | |
FREE Soundproofing Workshop: https://www.soundproofyourstudio.com/workshop I don't know about you, but life can be pretty stressful and chaotic. When I build and design soundproof home recording studios I try to make my job as easy as possible. This means eliminating as many decisions as possible and focusing on the overall goal of creating a quiet space that is enjoyable to work in. What I find is many people in our community and even clients of mine tend to overcomplicate the process. I think a lot of this stems from a fear that if they don't look at every option on the market in depth then their hard earned dollars will be wasted on a studio that does not live up to the high expectations they have in their mind. In this article I want to focus on what matters in studio design and what is mostly a waste of time. Let's dive in!
1) Don't buy into the hypeThere are so many soundproofing products that claim to help you eliminate noise. Some you might run into are:
And the list goes on and on. No wonder most of us spend hours, months and even years thinking about how to design a soundproof home recording studio without ever really moving forward with building it. The truth is, you can build a great soundproof home recording studio without any of the materials I listed above. Here is how. 2) Start With A Concrete SlabYou can float a floor, but it is not as effective or easy as simply starting with a concrete slab. Concrete is excellent at stopping sound, so I always recommend building your soundproof home recording studio on top of an existing slab or pouring a new one.
3) Use A Double Wall SystemIf you want some rock solid soundproofing then use a double wall system. This involves two layers of 5/8" drywall on either side of your wall with a 1" airgap and regular cheap insulation in the wall cavity. Simple! Easy! If you are really short on space you can use a system of acoustic clips and hat channels to decouple your drywall from your wall, but it does make things a bit more complicated.
4) Use A Hat Channel System For Your CeilingWhen I design studio, I almost always use a decoupled hat channel system on my ceilings. This means using special acoustic clips and metal furring channel attached to your ceiling rafters. You then drill the two layers of 5/8" drywall to your hat channels and wallah, you are done. Easy!
5) Use a mini split system for your heating and coolingThere are many ways to heat and cool a room, but my favorite design is to use a Mr. Cool mini split DIY kit. This allow you or your contractor to install the unit yourself, which saves thousands of dollars. I also love how quiet and efficient these units are.
6) Use and ERV or HRV and Baffle Box for Fresh AirYup, the mini split will not bring in fresh air into your air tight room. So, we need a seperate system to give you nice quality fresh air. I like using and ERV or HRV (depending on the climate) to bring in fresh air and pull out stale air from your studio. I run my ventilation lines through a baffle box which makes it so you can't hear the air noise or any noise transfer between your room and the outside. ConclusionDon't sweat the details and don't get lost in tone of soundproofing supplies. In my designs, the only true soundproofing supplies you need are acoustic clips for your hat channels and acoustic clips to help as sway braces for your inner walls. If you need more soundproofing add more mass. That means use 3-4 layers of type x 5/8" drywall instead of two. Simple, easy and straightforward. Don't overcomplicate something that is by nature very complicated to begin with.
| |||
06 Nov 2023 | Should You Use Tecsound to Soundproof? | 00:13:38 | |
FREE Soundproofing Workshop: https://www.soundproofyourstudio.com/workshop There are many soundproofing underlayments on the market and one of those materials is Tecsound. Now Tecsound is sold in the UK and throughout Europe, so it doesn't apply to those of us in North America. That said this type of product is similar to MLV and other visco elastic polymers that add mass to a structure and dampen sounds. In this article I am going to go over what Tecsound is and when and if you should use it on your soundproofing project.
1) What Is Sound DampingBefore we dive in on what Tecsound is I wanted to go over what damping is. According to Technicon Acoustics: "Damping removes vibration energy from a structure or system by eliminating the dynamic stresses associated with vibration." - Technicon Acoustics The way sound and vibrations are eliminated is because the product will flex and move converting acoustic vibrations to heat. Now damping is a useful tool when soundproofing, but it must be used with a soundproofing system to be effective. Simply hanging Tecsound on your wall would not make it soundproof.
2) What Is Tec Sound?According to the Tecsound Data Sheet: "TECSOUND® is a high density polymer-based, asphalt-free, synthetic soundproofing membrane, that offers good acoustic insulation in different building elements.." It is used in the following ways: · Soundproofing against airborne noise in ceilings and lightweight roofs. · Reduction of impact noise level in all types of floors, sandwiched between floor slabs and loose-laid flooring. · Damping of impact noise caused by atmospheric agents on metal decks. · Combined with sound-absorbent materials, it offers products with high acoustic performance. · Its applications in the industrial field cover from the soundproofing of booths to the acoustic insulation of machine-rooms, gutter pipes, sound damping of metal sheets, etc. It essentially is a mat that can be put on walls, ceilings, roofs or metal to help reduce sound energy and sound vibration.
3) How Much Does It Cost?Tecsound is not cheap. The cost per square meter for Tecsound100 (the best for soundproofing) runs at 14.87 Euros per square meter and that doesn't include shipping and tax. I wouldn't recommend the lower Tecsound ratings of 70, 50 or 35 because the mass is so much less than drywall. I don't think you are getting as much value for your money.
4) Do I recommend using Tecsound?For most soundproof rooms and home recording studios I would not recommend using Tecsound. The reason is that the cost doesn't really outweigh the benefits. Let me explain. When we soundproof we need a system. Let's look at a wall for example. If we build a double wall system with two layers of 5/8" drywall on either side of it we will get an STC rating of 63, which is plenty good for a soundproof home recording studio. Adding soundproofing materials like Tecsound and Mass Loaded Vinyl can increase that STC rating, but it is not really necessary and I would rather add more mass than a damping layer. Here is my point, if you were to add one more layer of 5/8" drywall to your wall it would cost you 5.70 euros per square meter. That is a 38% cost savings over Tecsound, plus you get more mass on your wall, which means greater soundproofing. Tecsound 100 weighs 10kg/sqm while 5/8" drywall weighs 10.7lb/sqm. The drywall costs 38% less and weighs more. Yes, you do not get the damping, but mass is ultimately what we are looking for to increase the transmission loss of our soundproof wall.
5) When You Should Use TecsoundNow, there are certainly times when Tecsound will be your best option. It would be great as an inner layer of an exterior wall to the outside both as a vapor barrier and added mass and damping. It would be great if you cannot lose the 5/8" of drywall in your room. It also is useful for soundproof machinery, metal decks, and things like cars or boats where traditional soundproofing methods are not practical. I am proposing that Tecsound is not necessary and an added cost when soundproofing a room or home studio.
| |||
15 Nov 2023 | My Three Soundproof Door Mistakes | 00:14:22 | |
FREE Soundproofing Workshop: https://www.soundproofyourstudio.com/workshop I had done a version of this article before, but this one builds on the last and introduces a new mistake or two! In this lesson I will go over three mistakes I made when building my soundproof door that really didn't not become apparent until years into its use.
1) Where Did I Learn To Build My First Soundproof DoorLike anyone, we all start with no experience. I only had Rod Gervais's book as a guide and being the person I am, I followed it to a T, you could say religiously. The problem is that Rod's design or more likely, my interpretation of his design did not end up working for me. No shade on Rod, I respect his book and ideas, but my point is that a simple book with a fairly quick run through of how to build a soundproof door never beats the experience of building soundproof doors over and over again and the experience of knowing what happens to that door over time.
2) Soundproof Door Mistake #1: Buy High Quality Door SealsIn his book, Gervais explains that he uses GM trunk rubber and magnetic seals to build custom seals around his doors. He does mention a company called Zero International as well. In my experience the trunk rubber he recommended or at least the one I bought using his recommendations to the best of my research ability, was too stiff. The door would bounce of the seal and it was very difficult to get a complete seal around the door. So, we took off most of the trunk rubber and used weather stripping we found at our local hardware store. The weather stripping we used is not amazing, but it did the trick. It is called Frost King here in the United States and comes in various widths and depths. You can customize the size to your door design. On top of using these Frost King weather seals I also recommend that you buy high end door seals to go on the inside of each of your doors. The seals I recommend are: Zero International Door Bottom 367AA Zero International Perimeter Seals 770AA These are not cheap and I spent $770 on my seals and am excited to install them in the coming weeks. If you cannot find these specific seals in your country then look for a similar item that is high quality and acoustically rated.
3) Soundproof Door Mistake #2: Buy A Mortised Door HandleThe second mistake I made was buying a relatively cheap and thus not sturdy door handle and deadbolt for my door. In a previous lesson I talked about buying a door handle with the wrong backset, but that is another story. Today I am saying not to buy a through the door door knob. The reason, mortised locksets don't go all the way through your door, thus improving soundproofing, but they also are usually made for heavier doors and can handle the pressure of a 300lb door. I have really enjoyed using a company called TruDoor here in the states. Mortised locks are available all over the world, so check your local supplier to pick the right one. You can also use a closed cell foam to help insulate the door handle from sound.
4) Soundproof Door Mistake #3: Buy Pre-Hung Solid Core DoorsIt can take a little digging, but getting a pre-hung solid core door is a great starting place. It might be a little more expensive, but you don't have to try and hang a door let alone a very heavy door. If you have not hung doors before it is a very labor intensive process = money/time = money in the end. Again, in the united states I really like TruDoor. They seem to have great support and a very efficient website, which is so helpful and worth extra money a lot of the time. If you can find pre-hung solid core doors locally then go with that. The install of the pre-hung doors is beyond the scope of this lesson, but that is another pieces of this complicated soundproofing puzzle I will save for another time.
ConclusionIn the end, buy high quality door seals, buy a mortised lockset, and try to buy pre-hung solid core doors if you can. This will save you time and money in the long run. Remember, I am speaking from years of experience now, so trust me when there are certain corners you just don't want to cut when soundproofing.
| |||
26 Nov 2023 | How To Soundproof A Door - Part 1 | 00:13:30 | |
FREE Soundproofing Workshop: https://www.soundproofyourstudio.com/workshop I have done many articles over the years on soundproof doors. Lately, I have changed how I build them from my earlier videos. I am going to do a multi part series on door design and building over the next few weeks. Today will be all about framing the door and where to source your solid core doors.
1) Framing Your DoorsFor this example I will be using two interior walls framed with a 1" air gap. The same principles apply if you are using a hat channel system on your walls or have one wall that is interior and one wall that is exterior. Below is a diagram of how to properly frame a soundproof door. Most of the framing is consistent with normal construction, however we want to add an extra king stud to support each or our 140+ lb doors.
I would recommend 24" OC framing if your wall can handle it. You should calculate the max load your wall can handle before framing 24" vs. 16" OC. From a soundproofing perspective the less wood to transfer sound in anyway the better.
2) Rubber Seals and Sway BracingOne very strange aspect of a double wall design is how to seal the air gap so that it is still soundproof, but also so that you don't smell or see into the wall cavity between your two doors. The solution is to use rubber. I recommend buying 1/16" x 8" rubber off amazon here in the states. This way your rubber seal will fit your two walls perfectly. Notice the diagrams below.
The rubber should be attached with screws and acoustic sealant to make sure it is airtight. I place the rubber on the outside king studs, because we will be using a prefinished steel door frame that will wrap around the inner jack studs and two layers of 5/8" drywall. The remaining gap between the rubber and inner door frame will be filled with 1" rigid Corning 703 insulation wrapped in Guilford of Maine Acoustic Fabric. Notice I recommend placing the rubber on top of your header and under the cripple studs. This will cover the 1" air gap at the top of your door. The bottom of the door will have a threshold and the studs will be cut away for entry.
To keep your walls from swaying with the weight of the door we need to add sway bracing to the interior walls. I like to use I-B3 clips from The Soundproofing Company. Place these clips every 48" OC on the top plate of your inside wall and connect it to the ceiling joists. This will still decouple your wall, but provide much needed support to your inner decoupled wall.
3) Doors and Door HardwareOver the years, I have moved beyond the Rod Gervais book and have begun designing my own system for soundproof doors. This has led me to a great site here in the states called TruDoor. They have everything we need to order all the door parts in one place. The following is what I recommend for each door. Simply double the materials to get your communicating door system. *If you don't live in the States then do your best to find these similar materials in your own market.
Total Door and Hardware Cost - 1,371.22 Total Entryway Cost = 2,742.44 If that number shocks you, then you probably have not researched pre-built soundproof doors. Custom Soundproof Doors can reach the $6,000-8,000 range. The lowest price I have found for a quality soundproof door is $3,260/door. So, you can cheap out on some of the items above, but it will sacrifice your level of soundproofing. Lastly, this is part one of a multi-part series. The solid core doors only weigh 60 lb so, we will need to add weight to each door. This will add some more costs in materials. We will also need to go over how to install the doors and ensure they are airtight. Stay tuned for part two.
| |||
27 Nov 2023 | How To Soundproof A Door - Part 2 | 00:26:39 | |
FREE Soundproofing Workshop: https://www.soundproofyourstudio.com/workshop Last week I wrote about how to build a soundproof door part 1, however, after lots of thinking and designing I have scrapped a lot of what I taught in part 1 of this series. This is an iterative process for me as I am designing the perfect doors for my clients. In part two of this series I will go over my new findings and my new design. The entire goal is to create an affordable yet solid soundproof door for all home studio enthusiasts. I have borrowed ideas from Rod Gervais, J.H. Brandt and my own building and design experience to create what I think will be a very effective and affordable soundproof door plan.
1) The Air Gap and WIC IsolationFirst, I found that the WIC isolation clips made by Mason Industries are 1 1/2" wide. Meaning your air gap between your walls must also be 1 1/2" not the usual 1" I recommend. The reason I am recommending using the WIC isolation clips is that they can each hold up to 250 lb and are much higher quality than the usual I-B3 sway bracing clips I recommend. The I-B3 clips hold 38 lb per clip. This said you could still use the I-B3 sway clips for our doors since the doors each weigh 123.5lb.
2) Where To Place Your Rubber SealsThe big discrepancy between JH Brandt's door design and Rod Gervais's is in leaving a gap between the double wall or connecting the two with wood. I like JH Brandt's design better because it keeps the integrity of our double wall system, whereas Gervais chooses to bridge the gap at the door with 5/4" wood stock because he feels the doors need the support. I agree with JH Brandt that we can support the doors using the WIC clips and not sacrifice our double wall system. However, if we do leave the air gap, Brandt points out that there will be odors that emanate from the double wall cavity. To block the odors we add a rubber seal around all four sides of the door opening. The rubber should extend from the edge of the outer wall to the edge of the inner wall. According to Brandt, you should also place rubber on the floor of the opening and ensure it is sealed against the two sides. I question whether this is necessary and may removed it in future plans, but for now it is part of the design. The rubber should be attached with screws, but you also should run three beads of acoustic sealant down the middle and sides of the rubber before adhering it to the studs and floor. You can see the rubber in the diagram below attached to our stud wall and concrete floor. *As a side note, in part 1 of this series I had the rubber on the outside of our king studs. I have changed that design because I no longer want to use pre-made door frames. I will explain why later on.
3) Building Your DoorThe actual door, meaning the swinging wood is going to be made from a solid core door that is 1 3/4" wide. This door should weigh around 66 lb (30 Kg). Now a 66 lb door alone is not enough mass to match our double drywall. The two layers of 5/8" drywall equals 4.4 lb per square foot (10.7 kg/ sqm). We need our 36" x 80" door to weight at least 4.4 lb x 20 square feet = 88 lb (40 kg). To do this I like to add 16 gauge plate steel to and 1/8" plywood to the back of each door. This is the side of the door facing the inner wall.
16 gauge steel weighs 2.66 lb/ sq/ft. And 1/8" plywood weighs 0.4lb / sq/ft. The steel and plywood will go on the back of each door leaving a 3/4" gap around the door. The gap is to create a bank vault seal as you can see in the diagram below. Because of this 3/4" gap the weight of our added plywood and metal is about 57.5 lb (26 kg). That brings the total weight of the door to about 123.5 lb (56 kg). This is well over the 88 lb we needed to match our walls. Going over is a good thing, because our doors are a natural week point and we want to beef them up as much as possible within reason. So how do we attach the door to the door frame. The answer is with our continuous hinge. I recommend using the ABH A110HD Heavy Duty Full Mortise Concealed Continuous Geared Hinge. This hinge will help with hanging the door plumb with the frame and will hold the added weight of a heavy door. Lastly, to finish building our doors, we will need a door lockset. Now from part 1 you noticed I recommend a mortise lockset. The reason is twofold. First, we want something that doesn't fully go through our door and second we want a lockset that can withstand the added weight of our heavy door. I recommend buying the Cal Royal NM Series Mortise Lock. This lockest has a 2 3/4" backset, which is just enough room to clear our bank vault seals. It also fits a 1 3/4" door. This is an important detail to note, your added metal and plywood will have to fit around the door handles in this case. This is not a huge deal, but does require a bit more care when cutting the metal and plywood to fit the back of the doors. An important detail is to add some thin closed cell foam that will go over the mortise lockset. Poke holes where the handle lever will be. This will create one more solid seal to prevent air and sound from traveling through the mortise lock. That covers the door itself. As a side note, it is a good idea to hang the door with just the solid core door first and then add the metal and plywood after it is hung. You can add the lockset towards the end as well. It might be easier to cut out the mortise for the lock before hanging the door.
4) Building Your Door FrameIn part one of this series I had said to use a pre-made steel frame, however, after much thought and consideration I have decided to stick with the tried and true method of building your own door frame. Because our doors are so heavy we are going to use 5/4" wood stock to frame our door. The frame will attach to each 2x4 stud in the rough opening and will protrude out 1 1/4" to run flush with the two layers of 5/8" drywall. See the diagram below.
After we have build the frame we need to add our first set of bank vault seals. I like to make these out of 1x3" lumber. I then attach 3/4" Frost King Weather striping to the ends of the 1x3" to create a tight seal against our solid core door. See the diagram below for an idea of how this works.
5) Adding Zero International Seals Around the DoorNow that you have the frame, the door, our added metal and plywood on, you are now ready to seal up the door completely. To do this we will use Zero International seals. I like these seal because they are high quality and have excellent acoustic ratings. The seals I recommend are:
These seals will go over the metal and plywood of the door. See the diagram below to see how the perimeter seal works.
These perimeter seals can be adjusted to fit snugly against the door ensuring no sound will enter or exit the door. The door bottom is a very important part of the this door system. The door bottom I recommend is a drop seal and will seal the air gap below the door when the door is fully closed. See the diagram below.
Once you have installed the door bottom your door should be air tight and ready to go. You can add some trim around the outside and seal it with acoustic caulk to finish off the door. Now you just have to repeat all the step for the second door and you will have your communicating door system.
6) Adding Rigid Insulation Between Your Door FramesThe last step to finishing our doors is to fill the gap between our two stud walls and rubber with rigid 3lb per square foot fiberglass batts. I recommend using either Corning 703 or Knauf Ecose insulation. Cut the fiberglass batts down to size so that the first layer fits snug up against the rubber and the two 2x4's in our framed wall as well as the two headers.
Next, we will add the second layer of insulation, but this time we will wrap it in acoustic fabric such as Guilford Of Maine. This will fill the gaps between our 1x3 boards around all three sides of the entryway. It has the added benefit of increasing isolation and making our door look nice and clean between the walls.
J.H. Brandt recommends adding two acoustic panels on the back side of each door in the air gap. He says this can increase the doors attenuation by 10 dB. I would recommend this if you have the budget and the space between your doors. 7) How Much Does This Door System CostIf we add up all the costs not including the framing of the wall itself we get the following:
Total Cost Per Door = $1,338.53 or $2,677.06 per entryway. Could you build these doors cheaper. Sure, you could get a cheap door handle, forgo the added perimeter gasketing. However, every corner you cut is a weak spot in your entire design. I try to balance cost with budget and things like the mortise lockset and perimeter seals are important in my opinion. *if you build your doors right, but don't use green glue you will have saved the cost difference anyway and will have a better soundproof room in the end.
| |||
04 Dec 2023 | Reaction - The MOST Effective Way to Soundproof any Room | 00:18:12 | |
This week I am doing something a little different. I had a member of our community reach out and ask me to do a reaction video to Home RenoVision's youtube video "The MOST Effective Way to Soundproof any Room." Well, after the watching the video I knew this member was right. I had to chime in on what made know sense in this widely watched video. This video goes over:
Enjoy! -Wilson
| |||
11 Dec 2023 | Soundproof Like A Pro - No Putty Pads | 00:09:25 | |
FREE Soundproofing Workshop: https://www.soundproofyourstudio.com/workshop I recently had a great long talk with the studio designer JH Brandt. Brandt has been designing recording studios for decades and he mentioned how he never uses putty pads to soundproof. I love the idea and wanted to share how to do it in this article.
1) Minimize holes in your soundproof shellNow, I call this method a pro method because it requires that we build our studio room with an outer soundproof shell and an inner acoustic shell. The two systems work together to both isolate and treat acoustics at the same time. This approach also allows us to hide our electrical behind the acoustic treatment and mount the electrical boxes and lights in the acoustic panel wall rather than the soundproof drywall. Here is a picture of this in action in one of JH Brandt's designs. Notice how the wall protrudes out from the door. This wall is made of lightweight wood and fabric with fiberglass batting behind it. It is not the soundproof wall. The electrical boxes can be framed directly into this fabric wall making it so you don't have to use putty pads.
2) How To Feed The Electrical In Your RoomThe electrical should enter through the front of the room through an electrical conduit pipe. There is an added benefit to this design where the audio electrical and audio XLR cables can run side by side eliminating ground loops, but that is a discussion I will save for another article. In the photo below, again courtesy of JH Brandt's free resources on his website: https://jhbrandt.net/resources/. In this photo the piping is coming in from the back of the room, but you could have your piping come in through the front wall. The key is to keep your soundproofing methods in tact when doing this. Run the pipe through the wall and use acoustic sealant where the pipe enters the drywall on each side. To increase isolation you can have the pipe enter the outside wall then have the pipe run through the wall for a several feet before having it enter into the inside wall. This makes it so both holes do not face each other in the wall system. Lastly, where the conduit enters the pipe you can seal up the opening around the wires with putty pad and acoustic caulk to reduce sound traveling through the pipe it self.
3) A Quick Note On Low Voltage WiringIf you are using lights with low voltage wiring, meaning they use a transformer to drop the voltage from the standard 120V in the United States, then you will need to run the low voltage wiring separate from an electrical that is supplying audio. A good rule of thumb is to run the low voltage wiring on the ceiling opposite the audio line on the floor. If you must cross the wires at any point it should be at a 90 degree angle.
Conclusion:Attaching all of your electrical boxes to your inside acoustic wall is a great way to increase isolation in a control room or home studio room. This can also be done in live rooms, but you would need an acoustic plan that covers your electrical runs and boxes. This method is not for every design, but is one I am am using more and more with home studio designs.
Work Cited: “Resources.” John H. Brandt Acoustic Designs, jhbrandt.net/resources/.
| |||
18 Dec 2023 | How To Build A Quadratic Residue Diffuser (QRD) | 00:21:43 | |
FREE Soundproofing Workshop: https://www.soundproofyourstudio.com/acoustic QRD Calculator: http://www.mh-audio.nl/Acoustics/diffusor.asp One of the most effective and efficient types of diffusers are reflection phase grating diffusers otherwise known as Schroeder diffusers. A type of Schroeder diffuser is the Quadratic Residue Diffuser (QRD) and in this article I will teach you how the diffusers work, the theory behind them, and how to build one.
1) How Does a QRD work?Manfred R. Schroeder developed the quadratic residue diffuser by using a series of wells of different depths with a constant width that are separated by thin dividers to evenly disperse sound back into the room. (Everest, 265). He found that a number sequence based on prime numbers can be used to calculate the depth of each well. This number sequence can also be repeated over and over (in periods) to expand diffusion across a wall or ceiling. When designing a QRD the maximum frequency for diffusion is determined by the well width and the minimum frequency is determined by the well depth. For example a QRD that needs to cover most of the audible spectrum would need to have very deep wells up to several feet and very thin well widths to cover say from 60 Hz to 10,000 Hz. This is one of the design limitations of QRD and phase grating diffusers in general.
2) The Math Behind QRD?So don't get scared, but I am going to talk about math. I am not a big math genius, so I always need to break down the numbers in simple terms, ideally, this makes me a better teacher for you! So, the equation behind the number sequence used to build the QRD is: Well depth proportionality factor = n^2 modulo p where n = integer greater than or equal to 0 p = prime number If you are like me, you had no idea what the heck modulo meant. Modulo is a calculation in number theory. It is a short cut for the following equation n^2 / p = x + remainder or residue n^2 modulo p = remainder or residue The modulo operation says take the n squared in our equation and divide so there is a whole number and a remainder. It says that the modulo will = the remainder not the whole number. If that still seems confusing let's do an example. Let's say we want to build a QRD with a prime number of 11. Now lets pick an integer of 5 in our number sequence from 0 to 11 for the diffuser. Again, I just chose 5 randomly for this example, when building the diffuser you would do 0 then 1 then 2 and so on up to 11. So, in our equation: Well depth = 5^2 modulo 11 Well depth = 25/11 = 2 with a remainder of 3 Well depth = 3 11 goes into 25 two times, which equals 22 and to get to 25 we have 3 left over. The remainder and residue terminology is interchangeable. Confusing, I know! So, the QRD are usually made from the following prime number sequences: 5, 7, 11, 13, 17, 19 and 23. Below is a chart from the Master Handbook of Acoustics that shows the well depth ratios for all of those prime number diffusers.
You will also notice the diagram showing one period or one diffuser length. Notice this period goes from 0 to 1 in the prime 17 sequence. This shows how diffusers can be placed side by side to continue the sequence across a wall or ceiling.
3) How To Design Your QRDSo, first we must choose a prime number to build our QRD. Each prime number has some benefits and limitations and ideally in a room design you might use a combination of different prime numbers to achieve a diffuse sound field across as much of the audible spectrum as possible. All that is a bit beyond this article. For this example, I will be building a QRD 13 based on the prime number 13 sequence. Now, the chart above is great in theory, but it is hard to imagine translating all those ratios to our actual physical diffuser. So, I recommend using a handy QRD calculator. There are a lot on the web, but this one does the trick: http://www.mh-audio.nl/Acoustics/diffusor.asp I will be doing this example in metric since my design is for a client in New Zealand, but you can do yours in imperial and all the concepts stay the same. My design is limited by space, as is the case for many home studios, so I will be working with a theoretical depth of 13 cm. I chose 13 cm because it will make the measurements whole numbers not decimals. I could have done a multiple of 13 like 26 cm, but my deepest well would be too deep for my room limitations. The width of my design should also be a multiple of 13. The reason is that this will make all of my well depths a whole number, so my design will be much easier to measure and build. With a theoretical depth of 13cm and a diffuser width of 65cm here are my well depths and well widths for my diffuser.
Notice, I get nice whole numbers. My well width is 5cm and my well depth are all whole numbers as well. We also get my low frequency cutoff and high frequency cut off. Ideally, I would diffuse from 20 Hz all the way to 20 kHz, but that is not really possible, so instead I am happy with a nice low mid to upper mid diffusion on the back wall of my design. This diffuser will help to widen and deepen the sound field when mixing and it will add back some of the life to the room, since I am using a lot of absorption to help control the low end and early reflections in my design. 4) How To Build Your QRDNow that you have all the well depths, and well widths you can design your diffuser. Use cabinet grade or marine AA grade plywood so the diffuser will look nice. In my design I am using 12mm marine AA plywood for my back, top, bottom and sides and 6mm marine AA grade plywood for my fins to separate the wells.
For my spacers I used 50 mm x 50 mm blocks on both the top and bottom of my diffuser to create the right well depth. To fill the wells you can use 12mm plywood to lay on top of your blocks. Here is a diagram to show how to do this.
Notice the well depth is the distance from the top of the diffuser fin to the to of the 12 mm plywood on top of your block. Each well is 1-13 from the chart above moving from left to right. It is good practice to dado out the well dividers on the back, top, and bottom so that you can simply slide your fins into the grooves. You can then attach the fins with wood glue. To build the top, bottom, back and sides you can use wood glue and some small screws to adhere the box together. Your spacer blocks and spacer faces can be attached using wood glue as well to keep the design clean and free of nails and screws.
ConclusionYou now know what a quadratic residue diffuser is, how the number sequence is derived, how to calculate your own design and how to build one. I hope this article was helpful in demystifing one of the more complex acoustic tools and allowing you to experiment with your own designs for your home studio.
Work Cited: Everest, Frederick A., and Ken C. Pohlmann. “Schroeder Diffusers.” Master Handbook of Acoustics, McGraw-Hill, New York, 2015.
| |||
25 Dec 2023 | Why Bigger Rooms Sound Better | 00:14:06 | |
FREE Acoustic Treatment Guide: https://www.soundproofyourstudio.com/acoustic We often here that big rooms sound better, but why is that. Why can't we get a small bedroom to sound awesome. I mean, we see home studios that look awesome online all the time, so why do they have to be big to sound good? This article will answer that question with the physics behind acoustics of small and large rooms and how this knowledge can help us understand and design our own studio builds.
1) A Quick Review Of Room ModesRoom modes require their own article, which I wrote here: Why Room Ratios Don't Work...Most of the time. But this article will focus on one aspect of room modes and room acoustics which is room volume. So, to quickly summarize, room modes are certain lower frequencies that create either peaks or nulls in your room. This means that when you walk around your room and play, say a 60hz tone, you will hear places in your room where the tone sounds louder, softer and miraculously even some places where you can't hear it all. I know freaky, but cool!
2) So what does this mean for small rooms?This is a problem for your listening environment and your recording environment too. We want to sit where the space in the room is as flat as possible. To get a "good room" we can start with a room that has even spacing of room modes in the lower frequencies below 300 Hz. Notice I said even spacing. It turns out having more room modes more evenly spaced sounds better. Weird, I thought we didn't want room modes is what you are probably thinking. Nope, we do want them and we want them evenly spaced so that none of them really poke out and cause big dips or nulls when we walk around our room. Here is a quote from the Master Handbook of Acoustics: " The short dimensions of a small room almost guarantee acoustical anomalies resulting from excessive spacing of room resonant frequencies." (Everest and Pohlmann, 436) Whoa, a lot to unpack there. This means the smaller the room the more likely you will have uneven, blurry, muddy sound in the low end due to too much space between your room modes, aka "resonant frequencies." 3) What is so great about large rooms?Here is another quote from the Master Handbook of Acoustics: "...large rooms have the inherent advantage of relatively more modes in the low-frequency region, and hence smoother low-frequency response"(Everest and Pohlmann, 436). The key word in this quote is smoother. The more modes means that the low frequency spectrum doesn't have big modal peaks followed by vast modal valleys where there aren't room modes. Remember, we want more room modes evenly spaced in the low-frequencies, 300 Hz and below. Now let's visually look at this using the AMROC calculator. I am going to input three dimensions using the Sepmeyer room ratio. This ratio of 1: 1.28 : 1.54 will get us the best room sound given our different sizes. However, even with an acousticians room ratios we will quickly see the limitations of our smaller room. First, here is the axial modes of a small studio with dimensions: 8ft ceiling, 10.24ft width and a 12.32ft length (2.44 m x 3.12m x 3.76m). The volume is 1,000 cubic feet. Second, here is a mid sized studio: 12 ft ceiling height, 15.36 width, and 18.48ft length (3.66m x 4.68m x 5.63m) Volume = 3,400 cubic feet. Third, let's look at a large studio: 16ft ceiling height, 20.48ft width, 24.64ft length (4.88m x 6.24m x 7.51m) Volume = 8,000 cubic feet. Okay, so what does all of this mean? Each of those red blocks is an axial room mode. Axial modes are the most powerful and problematic types of modes so I am showing those. To compare, let's look at 100 Hz and below. Small Room = 4 axial modes Medium Room = 7 axial modes Large Room = 9 axial modes Remember, we want more modes in the low-frequency range to smooth out the room's response. Also, notice that the larger rooms go lower down in the frequency spectrum. This is also good because we want that "smooth" response as low as possible. Ideally to the threshold of hearing at 20 Hz. ConclusionNow you know why bigger rooms sound better. The larger the room the more room modes you get in the low-frequency spectrum leading to a smoother more even response in the room, which translates to a cleaner more accurate low end. The high end of a room is easy to fix with basic acoustic treatment. The low end is very difficult to fix. In fact, the Master Handbook of acoustics says that "...anomalies encountered in studios having volumes less than 1,500 cubic feet are sometimes severe enough to make small studio rooms impractical" (Everest and Pohlmann, 436). Uggh! That totally bums us out right? What about your dreams of the bedroom studio or the small room in your basement. Great music is made everywhere, but know that for an accurate low end you will be always fighting an uphill battle in a small studio room. If you have the luxury of choosing a bigger and really higher ceilings then you should choose that room over the smaller room. This article was meant to give you some more tools in your arsenal of studio design, but not to discourage you altogether. I created amazing music in a very small room for many years and it did not stop me. Now, I create music in a bigger room and it has only made me better. You too can shoot for bigger and better rooms over time. Work Cited Everest, Frederick A., and Ken C. Pohlmann. “Modal Resonances.” Master Handbook of Acoustics, McGraw-Hill, New York, 2015. | |||
01 Jan 2024 | Why You Should Stagger Your Studs When Soundproofing | 00:07:56 | |
FREE Soundproofing Workshop: https://www.soundproofyourstudio.com/workshop When I built my first studio I did not stagger my double wall studs for soundproofing my recording studio. This was a small mistake, but nonetheless a mistake. I am going to give you two reasons why staggering your studs is important with recording studio design. 1) Structural IntegrityI had asked Rod Gervais, the author of Home Recording Studio: Build It Like The Pros about why he recommends staggering studs in a double wall system. His answer was that overtime studs can bend and if they bend inward they could actually touch each other thus short circuiting the system. He did admit, although this is rare he has seen it throughout his decades of building studios.
Staggered Stud Diagram (16" OC) 2) Weaker Soundproofing Due To CouplingI asked JH Brandt, a well respected and experienced studio designer the same question. Should you stagger studs? He also said it is a best practice in double wall design and the reason is that when studs are not staggered the drywall becomes a diaphragm that vibrates similar to a speaker cone. This pushes the air in the air cavity, which then starts to vibrate the other wall sympathetically. Once this process gets going it creates a bit of a feedback loop as well. This will weaken the system as a whole because sound can vibrate through the system more easily. Now, damping materials like MLV or Green Glue can help reduce the vibrations of the drywall, but simply staggering your studs, even by a few inches will reduce or eliminate the sympathetic vibration between your walls. 3) A Note On R Value and InsulationOne of the reasons we did not stagger our studs in my studio is because we needed an R30 insulation in the walls for our climate. However, R Value is additive, meaning if you need R30 you can use two insulations with an R15 value or one R20 and R10. You get the picture. This means if you don't have the space for R30 you can use two different insulations in each stud wall to make it work. Another option is to use a 2x6 exterior wall and a 2x4 interior wall and this will give you more space. ConclusionHaving two well respected studio designers teach me how I was wrong is honestly pretty cool. They both gave great and different answers for why you should stagger your studs. I hope these answers help you decide to stagger your studs when building a studio and give you the understanding on a deeper level to know why it is important. | |||
11 Jan 2024 | Why Vocal Booths Make Vocals Sound Bad | 00:09:58 | |
FREE Soundproofing Workshop: https://www.soundproofyourstudio.com/acoustic You read that right, vocal booth, the hallmark of any legitimate studio actually are bad for vocals. How you ask? In this article I will dive deep into the science, cite multiple reputable books and teach you what a vocal booth is really for.
1) What Are Vocal Booths Used For?To record vocals, right? No, they are used to separate the singer from the band when live tracking. Our modern notion of sticking singers in a dead small claustrophobic room with a terrible foldback system (headphone system) is not how final vocals are supposed to be recorded. Don't believe me? Richard Hilton who has recorded Diana Ross, Michael Bolton, SImon Le Bon, Tina Arena and many others will record the final vocals in the control room. Everyone wears headphones and can easily communicate and the room itself is way better sounding than a booth (more on that to come)(“RealTraps - Vocal Booths”). Moreover, some producers will even play the music softly over the speakers and forgo headphones all together to get a great vocal recording. Another thing to realize is that professional "vocal booths" actually are usually live rooms or fairly large neutral rooms. When you see an artist through the glass in a mulit-million dollar studio they are usually in a fairly large space, and if not it is to the deficit of the acoustics. Let's talk more about that.
2) Small Rooms Do Not Sound GoodPhysics cannot be changed. Small rooms, no matter how much acoustic treatment you put in them will always sound worse than a large room. Why? The first reason is that small rooms cannot support the massive wave lengths of low frequencies. This leads to the bass frequencies getting trapped (especially when the room is soundproof). This leads to a boomy boxing sounding room. You can add as much fiberglass panelling as you like, but those will not fix the low end. Bass traps, sure they can help a little, but they are not very effective below 100 Hz. Here is what the Master Handbook of Acoustics says about small vocal booths: "provide very little low frequency absorption. Thus important voice frequencies may be overly absorbed, whereas low frequency room modes are untreated" (Everest and Pohlmann, 480). The smaller rooms make it impossible to absorb low frequencies because you don't have the space for true low frequency absorption, plus room modes occur higher up in the frequency spectrum which means the bottom end of voices will ring out more than the higher end of the voice leading to a boomier and boxier vocal tone. You can spend $10,000 on your vocal chain, but if you record it in a bad sounding room then the vocal will always sound cheap. Just to drive this point home, here is an excerpt from Recording Studio Design by Philip Newell: "Simple attempts at absorption by placing of acoustically absorbent tiles on the walls and ceiling will not suffice. These will tend to absorb the higher frequencies but leave the lower-mid and low frequency modes largely untouched, yielding a room with a heavily coloured ambience which will lack life and add a thickness to the sound, robbing it of much clarity" (Philip Richard Newell, 153).
ConclusionThis is the argument against vocal booths and really small rooms in general. This is not to say you should never use a vocal booth. If you are tracking live bands then vocal booth are a useful for isolating the vocalist from the band. However, for most situations vocals should be tracked in a larger room. This could be the control room or a live room in a large studio.
Works CitedEverest, Frederick A., and Ken C. Pohlmann. “Acoustics of Audio/Video Rooms.” Master Handbook of Acoustics, McGraw-Hill, New York, 2015. Philip Richard Newell. Recording Studio Design. New York ; London, Routledge, Taylor & Francis Group, 2017. “RealTraps - Vocal Booths.” Realtraps.com, realtraps.com/art_booth.htm. Accessed 2 Jan. 2024.
| |||
15 Jan 2024 | My Mr. Cool Mini Spit Nightmare | 00:16:57 | |
FREE Soundproofing Workshop: https://www.soundproofyourstudio.com/workshop Over the past three years I have recommended the DIY Mr. Cool ductless mini split as a viable option for home studios. In this article I am going to explain why I no longer think this is a good option. 1) Three Weeks of No Heat at 4 DegreesEvery once in a while we learn from experience rather than books or videos. This is one of those situations. In theory the DIY Mr. Cool systems are great. They cost about $1200-$1500, you can install them yourself with a few tools, and they can heat and cool a room while staying somewhat quiet. You can always turn them off if they are too loud. Awesome, right? Well here is what happened to me so you can see where things go wrong. First, this past fall, three years after my mini split install the compressor stopped working. I think this was due to a a power surge hitting the unit and frying the logic board. The lesson here is to add a surge protector to your condenser. Through this experience I learned that most HVAC technicians have never heard of Mr. Cool and needed to call their tech support line. The tech could never get ahold of tech support. In fact, nothing happened until I emailed Mr. Cool and got involved. After several weeks of back and forth they finally decided to send me a new condenser outside unit free of cost except for the cost to ship it and hire someone to install it. This was great, minus the three to four weeks I didn’t have any heat in the studio because Mr. Cool’s tech support was not top notch. Then about two to three weeks after installing the new condenser I realized that the mini split was not putting out any hot air. I called another HVAC tech to come out and just yesterday he said that I had a refrigerant leak in the line set in my double wall system and that the only fix would be to open up the walls. Well, you can imagine that this is not an ideal scenario, so the lesson learned here is do not put your line set with the refrigerant lines where you cannot access them easily. It would have been best to run the line set on the outside of my studio so that we could easily check for leaks. This might lead you to wonder how a leak would open up? The HVAC tech said that a screw or nail could tag the line or the vibration of the line itself over time could rub against a sharp edge and open up. This could be what happened to me. We may never know. So here I am writing this in my studio with an oil based space heater (just to rub salt on the wound my internet is also out and Google Fiber can’t figure out what is wrong). What is the lesson for you in building your own soundproof home recording studio.
2) Ducted Mini Splits Vs. Ductless Mini SplitsThere are two types of mini splits and to be honest I am surprised at the the number of HVAC techs, contractors and even architects that don’t know this. The mini split I have is called a ductless mini split, meaning there is a condenser unit outside and a mini split wall or ceiling cassette unit on the inside. The condenser outside is connected with a refrigerant line set that runs to the head unit on the inside of your room. This system is great for most situations, but it is not great for soundproofing. First, the unit is quiet, but not that quiet. Now that it has not been working I am realizing how noisy it really was. In an ideal world you should not have any mechanical noises in your studio. This means no mini split head and only using solid state hard drives if possible. The other superior option is to use a ducted mini split. This is a system where the mini split is not attached to the wall or ceiling, but is instead installed in the attic or a separate mechanical room. The mini split unit is an air handler and it pulls air from the room heats or cools it and then pushes it back in the room. Simple right? Well, for a normal room, yes, but for a soundproof room, well it is a different story. More on that install in a second. So why didn’t I install the ducted mini split in the first place? Great question and with 20/20 hind site I sure wish I had. The reason I installed the DIY Mr. Cool Ductless mini split is the same reason you would. It is cheaper and seemingly a great option if you have never built a recording studio before. Experience is everything and I am learning that the really really hard way.
3) Overview of the Ducted Mini Split System
Short of finding a solution to my mini split problem that is an easy fix, I am really stuck between a rock and a hard place. I have to open up my walls and find the leak and repair it, but what if another leak happens? Option two is to run a new line set along the outside of the building and then punch a whole through my outside wall and connect the new line set to the existing mini split head. This is a cheaper solution, maybe, but it requires keeping my noisy mini split in the room and reducing my soundproofing by having a direct hole from the outside to the inside. This leads me to option three. Which, I think is the best option albeit maybe a little more expensive. I could buy the Olympus Mr. Cool 9000 BTU ducted mini split. I could install it in the ceiling of my bathroom attached to my studio. Then I could connect that mini split (hopefully) to my existing condenser outside unit. I could then tie in the mini split duct work with my ERV and baffle box system and have fresh hot and cold air supplied to my studio that is also quiet. Perfect right? The downsides to this solution are what keep most DIY people from doing this set up. The reason? Cost! But, this saying is very very true in recording studio builds. You get what you paid for. I repeat because this is the greatest knowledge and wisdom I can give you. You get what you pay for. All of your problems down the line in your studio will come from taking the cheaper DIY approach. So, to install a ducted mini split you must hire an HVAC tech. This will cost you thousands of dollars because those guys really know how to charge what they are worth. Lastly, if you want my best advice. Don’t buy a cheap unit. Buy a Mistsubishi or Fujitsu ducted mini split. Size it correctly for your room and you will avoid so many issues.
ConclusionLearn from my mistakes. They continue to cost me time and lots of money. Saving money on the front end doesn’t mean you saved money if you spend thousands of dollars fixing your mistakes on the back end. Buy a Mitsubishi or Fujitsu ducted mini split. If you can’t afford those units ask your HVAC installer for the next best option. I would stay away from Mr. Cool. There tech support alone is good reason to avoid them, but their units are cheap for a reason. That reason is that they are not built well and are prone to breaking in my experience. If you do use a ductless mini split system, run the line set outside of your studio and do your best to seal up the hole you run through your wall to help keep the wall soundproof. Remember, the ductless mini split should be a last resort not your first option. I hope this article was helpful and I hope you don’t go through what I am going through. Learn from my mistakes and you will thank me three to five years down the road. | |||
22 Jan 2024 | This Acoustic Panel Absorbs Down To 30Hz | 00:19:14 | |
FREE Acoustic Plan: https://www.soundproofyourstudio.com/acoustic Are you going crazy trying to find a way to absorb low frequencies in your recording studio? Look no further. Finally there is a way to absorb low frequencies using a broadband absorber. Let's dive in! 1) The Genius of Philip NewellIf you haven't heard or read any of Philip Newell's books, I suggest you do. He has been building and designing studios for decades and has worked with some of the biggest names (The Rolling Stones). In his book Recording Studio Design 4th Edition he describes a panel wall absorber system that can absorb down to 30Hz. Let's go over the design.
This is my rendition of Philip Newell's design. He of course does everything in metric and uses cotton waste felt instead of my recommendation of Knauf ECOSE insulation batts. I would love to use cotton waste felt, but I couldn't find any good suppliers in the United States that were cost effective. This said, let's dive into the design. A very important part of this acoustic wall is that it is built at least 2" from the isolation wall. 4" is better and one to three feet is even better than that. However, as Newell states in his book many studio owners do not see the benefit of better acoustics at the cost of floor space. For us home studio nuts we also need to find a balance between space, budget and our desire for pro level acoustics. I believe we can find that perfect balance and this design gets us closer to the truth we are seeking.
After the 2-4" air space we then have a 1" 3lb/ft3 Panel of Knauf ECOSE insulation. You can buy them in 2" panels and then cut them right down the middle for this design. Then Newell says to use a 5kg/m2 deadsheet (1lb/ft2). Now a deadsheet is really another name for a limp membrane having considerable inertia and little stiffness. In the United States we can use Mass Loaded Vinyl (MLV). Then we have another layer of Knauf Insulation. Then a 1/2" thick piece of drywall sandwiched over another layer of MLV and another 1/2" piece of drywall. Finally, we reach the stud wall frame. Fill this with R13 Owens Corning unfaced insulation. Then seal the frame wall with a layer of 1 lb MLV and one last layer of 1" Knauf Ecose Insulation. Wow, that was a lot. You might be wondering why we need all these layers. 2) How this panel works?Yes, it is more of an acoustic wall although you could build a panel out of this design if you wanted to save money. The key to this system working is the multiple materials working together to stop soundwaves through absorption and damping at different frequencies. Let's take a trip through the wall as a soundwave. Yay!!! So we start off hitting the Knauf Insulation. This will absorb our mid to high frequencies from say 500-20K Hz. Then we will fly through a deadsheet and this will dissipate some of the mid and low frequencies through damping. Then we will fly through our Owens Corning Insulation and even more of the soundwave will dissipate as heat. Then the low frequencies that remain will hit the drywall - deadsheet - drywall and get absorbed in the pressure cavity of the mass spring mass system we created with the sealed framed wall. Lastly, any remaining sound would hit the insulation - deadsheet - insulation and lose even more energy. Finally, the sound will hit our isolation wall. Depending on the type of wall (drywall vs mortar) the energy may get absorbed again or reflected back and sent right back through the whole system again. Needless to say, the low end frequencies really do get trapped in this system. Hence, it's ability to absorb down to 30Hz. In an ideal studio room you would line all four walls with this system. In a control room or a mix/production studio as is so common today you should use this system on three of the four walls and leave one wall and the floor reflective to keep the live of the room intact. 3) How much does this dang thing cost?Great question! The total wall costs $8.65/sqft if you use the materials I mentioned above. That does not include the cost of the wood frame. To acoustically treat a room that is 15ftx20ft you would be looking at around $2,500 in materials. Yes, that is a lot of money, but honestly insulation panels that only absorb down to 125hz would cost you that much as well if you bought professional ones. We also did not look into the ceiling, that will come in another article, but that will add another 1,000-2,000 as well. However, if you have looked at Acoustic Fields then you know getting this type of acoustic paneling can cost 20-40 thousand dollars, so why not use basic construction materials and get the same if not better results. Don't trust me, trust Philip Newell. He is the one who has taught me all these great studio design philosophies. Again, if you are serious about studio design I encourage you to pick up his Recording Studio Design book. Work Cited: Philip Richard Newell. Recording Studio Design. New York ; London, Routledge, Taylor & Francis Group, 2017. | |||
29 Jan 2024 | The Importance of Fire Stops In A Double Wall System | 00:07:23 | |
FREE Soundproofing Workshop: https://www.soundproofyourstudio.com/workshop One of the least sexy topics in soundproofing is fire stopping. Okay there may be no sexy topic in soundproofing, but this one is not fun, but important. In this article you will learn what firestopping is, why we need it and how to incorporate it into your soundproof wall system. 1) What is fire stoppingFire stopping is a construction technique where you use a fire retardant barrier to block a cavity so fire cannot spread through that cavity. In soundproofing this is important in our double wall and double ceiling cavities. In normal wall framing our walls have bays with insulation. If a fire were to break out inside of one of the bays it would not be able to spread easily to the next bay or to your ceiling. See the diagram below. Notice how fire cannot escape the through the bottom, sides or top of a typical stud wall. However, with a double stud wall there is essentially a chimney in between your two walls. See below: This gap at the top means a fire could easily spread to your ceiling and throughout the inside of your wall system without you even knowing. For fire safety it is important to seal that opening at the top of the wall, but how do you do that without bridging your two walls and negating all the benefits of a double wall system? 2) How To Build A FirestopI learned this fire stop technique from Rod Gervais in his book, Home Recording Studio: Build It Like the Pros. He says to use compressed rockwool or any rigid insulation batt to decouple the fire stop from the inside wall. See the diagram below: Here is a side view section of a design I am working on for a client. Notice the rigid batt insulation sitting on top of the top plate. This insulation could be 3lb/ft3 of Rockwool, Thermafiber or any similar brand. In this diagram it is 2" thick and is compressed 50% to 1". This compression is what keep the isolation intact. We don't want to compress the batt 100 percent because then the drywall would touch both walls. On top of the insulation batt is 1/2" drywall that is cut to span the gap between the two walls. It should be screwed in to the inner wall top plate on top of the insulation with as few screws as possible or you could use contact adhesive to minimize the connection points. Then you should seal between the rockwool and 1/2" drywall with fire caulk to create an airtight seal. Below is another diagram with a perspective view of the fire stop around two walls. Notice how the firestop seals the gap around the entire room making it much more difficult for fire to spread up into the ceiling. ConclusionAlthough this adds extra cost and labor to a build it is, nonetheless, an important part of the double wall design. It is always good to keep fire safety in mind when we are building a typical structures for sound isolation.
Work Cited Gervais, Rod. Home Recording Studio: Build It Like The Pros. 2nd Edition, Course Technology Cengage Learning, 2011.
| |||
05 Feb 2024 | How To Build A Pro Control Room (Part 1: Isolation) | 00:18:15 | |
FREE Soundproofing Workshop: https://www.soundproofyourstudio.com/workshop We can't all build professional control rooms, but we can learn a thing or two from how they are built and hopefully apply it to our own control room design. This will be a multi-part series in which I go through a control room design by world renowned studio designer, Philip Newell.
1) Site SelectionProfessionals would never build a studio in an unsuitable location for recording. In this design the building was already inside a concrete shell. The concrete floor ceiling and block masonry walls were an excellent starting point for a high level studio. The space was also massive. The control room had 7m x 7m of floor space to work with and 8m of height! That is roughly 23' x 23' and 26' tall ceilings. That is unheard of in the home studio word. Ironically, over 50% of that space would be used for isolation and acoustic control of the room.
2) Isolation WallsThe first step in designing the professional control room is to design the isolation walls. Newel used a concrete block or cinder block filled with sand for his interior isolation wall. In his design he angled the walls slightly, but he states in his book, Recording Studio Design, that both angled isolation walls and room ratios are not of much importance because they will not greatly fix low frequency modal issues. However, angled walls in the acoustic wall can be helpful for the reduction of flutter echo. The isolation walls are built with a 5cm-10cm gap from the exterior walls of the building. That is roughly 2-4" of space between the walls. I don't think he added insulation between the walls, but this would help with some added isolation, however the extra cost and labor would probably not add a noticeable difference in the isolation of this structure. Lastly, the isolation walls for this design were 4.5 meters tall or roughly 14.7 feet. Remember, when the studio is finished much of that height will be lost to acoustic control.
3) Isolated Concrete Slab FloorBecause this mix room is not the main floor of the building and it will share a foundational floor with a tracking room, Newell is using a floated concrete slab. For home studio, I usually urge people not to float floors due to cost and expertise, but again this is a professional studio with millions of dollars in investment and profits at stake. The first layer of the floor is a 10cm 70kg/m3 (4" 4lb/ft3) layer of mineral wool. This is the spring that will isolate the concrete slab. You can use isolation springs, but they are more costly and difficult to use. I believe Newell felt the isolation would be adequate for this design. He also states that this method could lead to better isolation because of the damping of the structural floor beneath the mineral wool. After the mineral wool you need to add a layer of plastic to prevent the concrete from soaking into the mineral wool. After that he added two layers of overlapping OSB took prevent the mineral wool from getting trampled by the workers laying the slab. Lastly, they poured a 10cm concrete slab (4") over top of the OSB sheathing.
To keep the concrete from touching the isolation walls they added a vertical layer of mineral wool between the isolation floor and the isolation walls. This ensures that concrete never reaches and connects the interior walls with the interior floor.
4) Ceiling Joists (Isolation Ceiling)Now the exterior ceiling of this room is at 8m and is a concrete ceiling. The second wall to complete the isolation shell is made of huge reinforced wood beams. The beams are made of two 20cmx5cm (2x8) boards glued and nailed together. Then a 10cm x 5cm (2x4) added on the top and bottom and finally two 25mm (1/2") plywood sheets glued and nailed to each side. See the diagram below.
I put these beams at 16" OC, but for construction of this nature it would be wise to have a structural engineer on your team to verify loads and make sure you are not over sizing or undersizing your beams. Below is another image of the finished beams attached to the inner isolation wall. You may be wondering if this short circuits isolation. I wondered the same thing. My thinking is that Newell knows the acoustic shell will be also helping with isolation and the need to decoupe the ceiling a second time is probably not necessary. Plus, the isolation cap, as he calls it, is far below the true ceiling of the room. This will also help with isolation.
Now I am not going over how the isolation ceiling is finished, because that will happen last after the acoustic shell ceiling is finished. We will go over this next week in part 2 of this series.
ConclusionHome studio soundproofing and pro studio soundproofing may look very different. If someone gave me a big enough budget I would use Newell's design, but for most of us mere mortals we must use the best materials we can within our budgets and space constraints. This said, using concrete sand filled blocks and choosing a suitable location for your control room will always put you in some of the top designed studio in the world, at least in terms of what you are starting with. My hope is that this helps you learn more about how the pros design studios so you can glean some wisdom from this approach.
Works Cited - Philip Richard Newell. Recording Studio Design. New York ; London, Routledge, Taylor & Francis Group, 2017. By The Book (affiliate link): https://amzn.to/4b7zyxd
| |||
12 Feb 2024 | Double Wall, Half Truth: Reaction Podcast | 00:27:02 | |
FREE Soundproofing Workshop: https://www.soundproofyourstudio.com/workshop It's time for another reaction video, this time I am reacting to one of Acoustic Fields video's on the "half truth" of the double wall system. In this video I go over:
| |||
19 Feb 2024 | How To Build A Pro Control Room - Part 2 | 00:18:53 | |
FREE Soundproofing Workshop: https://www.soundproofyourstudio.com/workshop This is part two of my series on Philip Newell's control room design. In this podcast I will go over the acoustic interior system. We will cover: - How much space room acoustics use up - Ceiling Isolation System - The Acoustic Ceiling System - The Ceiling Wave Guide Panels - Back Wall Acoustics - Side Wall Acoustics - Front Wall Acoustics -Room Liveliness Vs. Anechoic - Final Thoughts on how this is all relevant to your own home studio design and build.
| |||
26 Feb 2024 | Does My Studio Soundproof Drums? | 00:16:19 | |
FREE Soundproofing Workshop: https://www.soundproofyourstudio.com/workshop This is a question someone in our community asked me on youtube. Well, I made a video to answer that exact question. In this video I will go over:
In conclusion you will find out if my studio soundproofs drums and what I would do to increase that isolation in the future. |