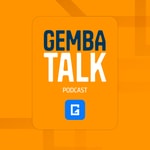
GembaTalk (GembaDocs)
Explore every episode of GembaTalk
Pub. Date | Title | Duration | |
---|---|---|---|
25 Feb 2025 | Why "Knowledge is Bad" - The Power of Standard Work in Manufacturing with Stephan Hilmer of Tridelta Meidensha | 00:31:09 | |
Tom Hughes sits down with Stephan Hilmer, COO of Tridelta Meidensha, to discuss how standard processes revolutionized their approach to efficiency and training. Stephan reveals how Lean methodologies helped their company navigate the challenges of the pandemic and optimize production. "Knowledge is really, really bad. Knowledge is bad until you put it on paper. You are the expert when you get everybody able to do whatever you are doing right now." - Stephan Hilmer Key Topics:
"Trust your people, train your people, and then you will explode. The sky is the limit." - Stephan Hilmer Takeaways:
Links and Resources:
Connect with Us:🎙️ Subscribe to GembaTalk podcast for more insights on Lean culture, SOPs, and manufacturing excellence. | |||
11 Feb 2025 | How Seating Matters Achieved Process Excellence with Ryan Tierney | 00:24:54 | |
In this episode, Tom Hughes, founder of GembaDocs, sits down with Ryan Tierney from Seating Matters to explore the transformative power of standardized operating procedures (SOPs). Discover how Seating Matters became a world-class Lean organization, the challenges they faced during implementation, and practical tips for success. “We wasted so much money, so much time with systems that weren't up to scratch.” - Ryan Tierney Key Topics:
“..it wasn't until we documented the process we saw how much waste there was. So there was probably 45 or 46 steps in this before. But the physical act of going through the documenting process forced us to improve it and see the waste.” - Ryan Tierney Takeaways:
Links and Resources:
Connect with Us:🎙️ Subscribe to GembaTalk podcast for more insights on Lean culture, SOPs, and manufacturing excellence. | |||
04 Mar 2025 | How a bang on the head sparked a Lean business with Pablo Scarpatti of Scarpatti Amoblamientos | 00:34:02 | |
Pablo Scarpatti, co-owner of Scarpati Amoblamientos, chats with Tom about how Lean principles have helped scale his custom woodworking business. Pablo shares insights on the birth of his lean business starting with an accident, how he developed workforce understanding of processes with QR codes, the process standardization, and the role of a strong skills matrix (and how it inspired GembaDocs Skills Module!) in driving growth. "Knowledge alone is not enough—if it's not documented and shared, it doesn’t exist." - Pablo Scarpatti Key Topics:
"So teach them everything and releasing from them the fear. It's a roof that many people have. They don't want to do things because they're frightened. And sometimes in the production culture, the owners, like myself, have the fear of holding people because you don't want them to go because who else is going to do that task that only he can do. So yeah with the skills matrix, everybody can do it because everybody can learn. So you don't have a specialist. Everybody can be a specialist." - Pablo Scarpatti Takeaways:
“If a 10-year-old can follow our SOPs, then we know we’ve done it right” - Pablo Scarpatti [talking with pride about his daughter knowing how to start and use their machines, and even get the factory up and running with the electricity generator!] Links and Resources:
Connect with Us: 🎙️ Subscribe to GembaTalk podcast for more insights on Lean culture, SOPs, and manufacturing excellence. | |||
11 Mar 2025 | “Just Start!” to overcome perfection and implement lean, with Brian Meyers from Fat American Manufacturing | 00:23:09 | |
Tom talks with Brian Meyers, founder of Fat American Manufacturing (FAM) and multiple off-road manufacturing brands to find out how traveling to Japan and Europe gave Brian a new perspective on Lean - and how his company has rapidly implemented standardized work to improve efficiency. By embracing standard work, giving employees ownership, and integrating SOPs into daily operations, Fat American Manufacturing (FAM) has made incredible progress in just five months. If you’re struggling to get started with Lean, Brian’s advice is simple: “Just start.” "When I got to Japan I saw everything and I was like this is crazy and then I came home and I was really frustrated and I was like we suck but I had no idea how to do it and I didn't know what I was looking at [...] And then all of a sudden everything was like click, click, click, click, click, and I was like, it's lean, I saw lean!" - Brian Meyers" - Brian Meyers Key Topics:
"Yesterday alone, we made 35 SOPs. If you have 10 people doing SOPs, you won’t get far. If you have 40, you’ll get there fast.." - Brian Meyers Takeaways:
Links and Resources:
Connect with Us:🎙️ Subscribe to GembaTalk podcast for more insights on Lean culture, SOPs, and manufacturing excellence. | |||
18 Feb 2025 | Scoring Goals through process with Dwain Steele of Hampton Conservatories | 00:31:56 | |
Hampton Conservatories are one of the original GembaDocs customers, so Tom got Dwain Steele, Production Manager, to dive into how standard processes with GembaDocs took the chaos and burden out of their workflow in the last three years to create a book of knowledge. "The power it gives my team - ’I did a process today’ - this is fantastic, they went home, they feel great, because they've created this process that never existed at Hampton Conservatories, they've scored the goal.' - Dwain Steele Key Topics:
"It took me 22 years to become a production manager, I could have done that in half the time I reckon, because GembaDocs was there. Would have made life so much easier." - Dwain Steele And find out how every GembaDoc at Hamptons follows their own set standard, with clear start, finish and pencil to paper plan first before the app is even open. "you're training them on how to create the SOP to the standard you're expecting" - Tom Hughes Takeaways:
Links and Resources:
Connect with Us:🎙️ Subscribe to GembaTalk podcast for more insights on Lean culture, SOPs, and manufacturing excellence. | |||
18 Mar 2025 | How "What's in it for me" revolutionized IOTAFLOW's culture with Pankaj Malik | 00:26:41 | |
In this episode, Tom Hughes talks with Pankaj Malik, founder of IOTAFLOW, about how finding Lean principles 20years into business revolutionized his company. From quality issues to a world-class system with 1,000 SOPs, Pankaj shares how small changes created a massive culture shift in his organization. This shift has not only improved efficiency but has also enhanced employee well-being, with increased trust, better working conditions, and even company-funded medical care and dividends for staff. "...it's completely mistake proof, they have that drawing to which work, one, and second they don't have to hunt for SOP or drawing anymore" - Pankaj Malik Key Topics:
"I'm doing business for 25 years now. And 21, 22 years, I was struggling so much with quality and timely delivery. And when I read about 2 Second Lean and you know it's a panacea [cure] for all these problems, I wanted to jump right into it, do everything, whatever I could. So including the SOPs and the Kanban. So we really started all together, asked my people to make SOPs. There is a struggle. There is a communication gap. If there is a quality problem, let's have a look at what is the SOP. If it is not there, let's make SOP." - Pankaj Malik Takeaways:
Links and Resources:
Connect with Us:🎙️ Subscribe to GembaTalk podcast for more insights on Lean culture, SOPs, and manufacturing excellence. |